Maintenance
Replacing Light Bulbs
Replacing a Worklight Bulbs
-
Ensure that the light switch is in the OFF position.
-
Remove the 6 screws securing the worklight (Figure 73).
-
Remove the worklight cover (Figure 73).
-
Remove the lamp bulb with the open circuit across the filament wire.
-
Install the new light bulb.
-
Secure the worklight cover with the 6 screws.
Replacing a Taillight Bulb
-
Ensure that the light switch is in the OFF position.
-
Remove the 2 screws that secure the cover and lens to the taillight base.
-
Remove the taillight cover.
-
Pushing down on the pin on the light bulb, rotate the light bulb to the left, and pull the light bulb out (Figure 75).
-
Insert the new light bulb into the socket from which you removed the old light bulb.
-
Rotate the new light bulb to the right until the pin of bulb aligns with the slot in the light-bulb casing (Figure 75).
-
Install the taillight cover with the 2 screws.
Replacing a License Plate Bulb
-
Remove the 2 screws that secure the cover to the base of the license-plate light, and remove the cover (A of Figure 76).
-
Push down the bulb slightly and rotate it counterclockwise until it is unlocked from the light socket, and remove the bulb (B of Figure 76).
-
Insert the new light bulb into the bulb socket (B of Figure 76).
-
Press down the bulb slightly and rotate it clockwise until the bulb locks into the socket (B of Figure 76).
-
Align the cover to the base of the license-plate light with the lens down (A of Figure 76).
-
Secure the lens to the base with the 2 screws that you removed in step 1.
Replacing Fuses
Replacing the Taillight Fuse
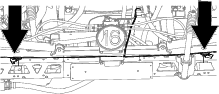
Note: Your machine has separate fuses for the left and right taillights.
-
Remove the cover from the fuse socket (Figure 78).
-
Remove the open fuse (Figure 78).
-
Insert the new fuse into the socket until the fuse is fully seated (Figure 78).
Note: Use only a fuse that is rated for the same current load as the fuse that you are replacing.
-
Assemble the cover onto the fuse socket (Figure 78).
Replacing Fuse Block Fuse
The electrical system is protected by fuses, and requires no maintenance. If a fuse blows, check the component or circuit for a malfunction or short.
-
Pull out the open fuse.
-
Replace the open fuse with a new fuse (Figure 79).
Note: Ensure that the correct-size fuse is installed.