Maintenance
Note: Determine the left and right sides of the machine from the normal operating position.
Recommended Maintenance Schedule(s)
Maintenance Service Interval | Maintenance Procedure |
---|---|
After the first 50 hours |
|
Before each use or daily |
|
After each use |
|
Every 25 hours |
|
Every 50 hours |
|
Every 100 hours |
|
Every 200 hours |
|
Every 400 hours |
|
Every 500 hours |
|
Before storage |
|
Important: Refer to your engine operator's manual for additional maintenance procedures.
Caution
If you leave the key in the ignition switch, someone could accidently start the engine and seriously injure you or other bystanders.
Remove the key from the ignition and disconnect the wire from the spark plug before you do any maintenance. Set the wire aside so that it does not accidentally contact the spark plug.
Pre-Maintenance Procedures
Raising the Seat
Make sure that the parking brake is engaged, and lift the seat forward.
The following components can be accessed by raising the seat:
-
Serial plate
-
Service decal
-
Seat-adjustment bolts
-
Fuel filter
-
Battery and battery cables
Raising the Front of the Machine
If the front of the machine needs to be raised, use the very front edge as show in Figure 22.
Important: To prevent damage to the steering mechanism, ensure the very front edge of the machine is used for jacking points.
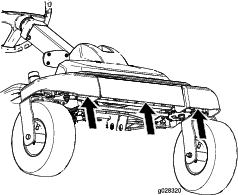
Lubrication
Greasing the Bearings
Maintenance Service Interval | Maintenance Procedure |
---|---|
Every 25 hours |
|
Grease Type: No. 2 general-purpose, lithium-based grease
-
Park the machine on a level surface, and disengage the blade-control switch.
-
Ensure the parking brake is engaged, stop the engine, remove the key, and wait for all moving parts to stop before leaving the operating position.
-
Clean the grease fittings (Figure 23 and Figure 24) with a rag.
Note: Make sure to scrape any paint off of the front of the fitting(s).
-
Connect a grease gun to each fitting (Figure 23 and Figure 24).
-
Pump grease into the fittings until grease begins to ooze out of the bearings.
Engine Maintenance
Servicing the Air Cleaner
Maintenance Service Interval | Maintenance Procedure |
---|---|
Before each use or daily |
|
Every 50 hours |
|
Every 100 hours |
|
This engine is equipped with a replaceable, high density paper air-cleaner element. Check the air cleaner daily or before starting the engine. Check for a buildup of dirt and debris around the air-cleaner system. Keep this area clean. Also, check for loose or damaged components. Replace all bent or damaged air-cleaner components.
Note: Operating the engine with loose or damaged air-cleaner components could allow unfiltered air into the engine, causing premature wear and failure.
Note: Service the air cleaner more often under extremely dusty, dirty conditions.
-
Rotate the latches outward.
-
Remove the cover to access the air-cleaner element (Figure 25).
-
Remove the paper element.
-
Gently tap the paper element to dislodge dirt.
Note: Do not wash the paper element or use pressurized air, as this will damage the element.
Note: Replace a dirty, bent, or damaged element. Handle the new element carefully; do not use if the sealing surfaces are bent or damaged.
-
Clean the air-cleaner base as required, and check the condition.
-
Install the paper element onto the air-cleaner base.
-
Install the cover, and secure it with the latches (Figure 25).
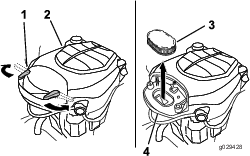
Servicing the Engine Oil
Oil Type: Detergent oil (API service SJ or higher)
Crankcase Capacity: 1.9 L (64 oz) when the filter is changed
Viscosity: See the table below.
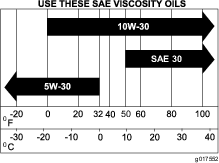
Checking the Engine-Oil Level
Maintenance Service Interval | Maintenance Procedure |
---|---|
Before each use or daily |
|
-
Park the machine on a level surface, disengage the blade-control switch, stop the engine, and remove the key.
-
Make sure the engine is stopped, level, and is cool, so the oil has time to drain into the sump.
-
Check the engine-oil level (Figure 27).
Changing the Engine Oil and the Engine-Oil Filter
Maintenance Service Interval | Maintenance Procedure |
---|---|
Every 100 hours |
|
Note: The drain plug is attached to the drain hose.
Note: Dispose of the used oil at a recycling center.
Fill with oil as specified in the “Viscosity Grades” table (Figure 26).
-
Park the machine, so that the drain side is slightly lower than the opposite side, to ensure that the oil drains completely.
-
Disengage the blade-control switch and move the motion controls outward to the park position.
-
Stop the engine, remove the key, and wait for all moving parts to stop before leaving the operating position.
-
Torque the plug to 14 N-m (125 in-lb).
-
Slowly pour approximately 80% of the specified oil into the filler tube (Figure 30).
Servicing the Spark Plug
Maintenance Service Interval | Maintenance Procedure |
---|---|
Every 200 hours |
|
Every 500 hours |
|
The spark plug is RFI compliant. Equivalent alternate brand plugs can also be used.
Type: Champion XC12YC (or equivalent)
Air Gap: 0.76 mm (0.03 inch)
Removing the Spark Plug
-
Disengage the blade-control switch, move the motion controls outward to the park position, stop the engine, and remove the key.
-
Before removing the spark plug(s), clean the area around the base of the plug to keep dirt and debris out of the engine.
-
Remove the spark plug (Figure 31).
Checking the Spark Plug
Important: Do not clean the spark plug(s). Always replace the spark plug(s) when it has: a black coating, worn electrodes, an oily film, or cracks.
Note: If you see light brown or gray on the insulator, the engine is operating properly. A black coating on the insulator usually means the air cleaner is dirty.
Set the gap to 0.76 mm (0.030 inch).
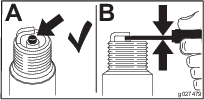
Installing the Spark Plug
Tighten the spark plug to 25 to 29 N-m (18 to 22 ft-lb).
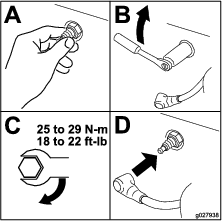
Cleaning the Blower Housing
Maintenance Service Interval | Maintenance Procedure |
---|---|
Every 100 hours |
|
To ensure proper cooling, make sure the grass screen, cooling fins, and other external surfaces of the engine are kept clean at all times.
Annually, or every 100 hours of operation (more often under extremely dusty, dirty conditions), remove the blower housing, and any other cooling shrouds. Clean the cooling fins and external surfaces as necessary. Make sure the cooling shrouds are installed. Torque the blower housing screws to 7.5 N-m (5.5 ft-lb).
Important: Operating the engine with a blocked grass screen, dirty or plugged cooling fins, and/or cooling shrouds removed, will cause engine damage due to overheating.
Fuel System Maintenance
Danger
In certain conditions, gasoline is extremely flammable and highly explosive. A fire or explosion from gasoline can burn you and others and can damage property.
-
Perform any fuel related maintenance when the engine is cold. Do this outdoors in an open area. Wipe up any gasoline that spills.
-
Never smoke when draining gasoline, and stay away from an open flame or where a spark may ignite the gasoline fumes.
Replacing the In-Line Fuel Filter
Maintenance Service Interval | Maintenance Procedure |
---|---|
Every 100 hours |
|
Every 200 hours |
|
Never install a dirty filter if it is removed from the fuel line.
-
Park the machine on a level surface and disengage the blade-control switch.
-
Ensure the brake is engaged, stop the engine, remove the key, and wait for all moving parts to stop before leaving the operating position.
Servicing the Emissions Filter
Maintenance Service Interval | Maintenance Procedure |
---|---|
Every 100 hours |
|
Note: This machine is equipped with a maintenance free emissions canister and a serviceable emissions filter.
Locate the emissions filter and replace it with a new one (Figure 35).
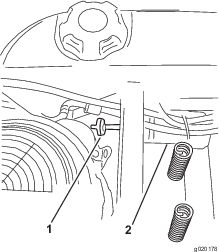
Electrical System Maintenance
Warning
Battery posts, terminals, and related accessories contain lead and lead compounds, chemicals known to the State of California to cause cancer and reproductive harm. Wash hands after handling.
Charging the Battery
Removing the Battery
Warning
Battery terminals or metal tools could short against metal machine components causing sparks. Sparks can cause the battery gasses to explode, resulting in personal injury.
-
When removing or installing the battery, do not allow the battery terminals to touch any metal parts of the machine.
-
Do not allow metal tools to short between the battery terminals and metal parts of the machine.
-
Park the machine on a level surface and disengage the blade-control switch.
-
Ensure the parking brake is engaged, stop the engine, remove the key, and wait for all moving parts to stop before leaving the operating position.
-
Raise the seat to access the battery.
-
Disconnect the negative (black) ground cable from the battery post (Figure 36). Retain all fasteners.
Warning
Incorrect battery cable routing could damage the machine and cables causing sparks. Sparks can cause the battery gasses to explode, resulting in personal injury.
-
Always disconnect the negative (black) battery cable before disconnecting the positive (red) cable.
-
Always connect the positive (red) battery cable before connecting the negative (black) cable.
-
-
Slide the rubber cover up the positive (red) cable. Disconnect the positive (red) cable from the battery post (Figure 36). Retain all fasteners.
-
Remove the battery hold-down (Figure 36) and lift the battery from the battery tray.
Charging the Battery
Maintenance Service Interval | Maintenance Procedure |
---|---|
Before storage |
|
-
Remove the battery from the chassis; refer to Removing the Battery.
-
Charge the battery for a minimum of 1 hour at 6 to 10 amps. Do not overcharge the battery.
-
When the battery is fully charged, unplug the charger from the electrical outlet, then disconnect the charger leads from the battery posts (Figure 37).
Installing the Battery
-
Position the battery in the tray (Figure 36).
-
Install the positive (red) battery cable to the positive (+) battery terminal using the fasteners removed previously.
-
Install the negative battery cable to the negative (-) battery terminal using the fasteners removed previously.
-
Slide the red terminal boot onto the positive (red) battery post.
-
Secure the battery with the hold-down (Figure 36).
-
Lower the seat.
Servicing the Fuses
The electrical system is protected by fuses. It requires no maintenance; however, if a fuse blows, check the component/circuit for a malfunction or short.
Fuse:
-
Main F1-30 amp, blade-type
-
Charge Circuit F2-25 amp, blade-type
-
Remove the screws securing the control panel to the machine. Retain all fasteners
-
Lift the control pane up to access the main wiring harness and fuse block (Figure 38).
-
To replace a fuse, pull out on the fuse to remove it (Figure 38).
-
Return the control panel to its original position. Use the screws removed previously to secure the panel to the machine.
Drive System Maintenance
Checking the Tire Pressure
Maintenance Service Interval | Maintenance Procedure |
---|---|
Every 25 hours |
|
Maintain the air pressure in the front and rear tires as specified. Uneven tire pressure can cause uneven cut. Check the pressure at the valve stem (Figure 39). Check the tires when they are cold to get the most accurate pressure reading.
Refer to the maximum pressure suggested by the tire manufacturer on the sidewall of the caster wheel tires.
Inflate the rear drive wheel tires to 90 kPa (13 psi).
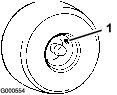
Releasing the Electric Brake
The electric brake releases by manually rotating the link arms forward. Once the electric brake is energized the brake will reset.
To release the brake:
-
Turn the ignition key to the Off position or disconnect the battery.
-
Locate the shafts where the brake-link arms are connected on both sides of the electric brake (Figure 40).
-
Rotate the shafts forward to release the brakes.
Hydraulic System Maintenance
Hydraulic System Oil Specification
Oil Type: Toro HYPR-OIL® 500 or 20w-50 motor oil.
System Capacity:approximately 4.495 L (152 oz) with a filter change.
Checking the Hydraulic Oil Level
Maintenance Service Interval | Maintenance Procedure |
---|---|
Every 25 hours |
|
Check expansion reservoir and if necessary add the specified oil to the Full Cold line.
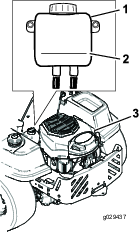
Changing the Hydraulic System Oil and Filters
Maintenance Service Interval | Maintenance Procedure |
---|---|
After the first 50 hours |
|
Every 400 hours |
|
Important: The bleeding process is repeated until the oil remains at the Full Cold line in the reservoir after purging. Failure to properly perform this procedure can result in irreparable damage to the transaxle drive system.
Note: The filter and oil are changed at the same time. Do Not reuse oil. Once the new filter is installed and oil is added any air in the system must be purged.
Removing Hydraulic System Filters
-
Stop engine, wait for all moving parts to stop, and allow engine to cool. Remove the key and engage the parking brake.
-
Raise the rear of machine up and support with jack stands (or equivalent support) just high enough to allow drive wheels to turn freely.
-
Locate the filter and filter guards on each transaxle drive system (Figure 43). Remove three screws securing the filter guard and guard.
-
Carefully clean area around filters. It is important that no dirt or contamination enter hydraulic system.
-
Place a container below the filter to catch the oil that drains when the filter and vent plugs are removed.
-
Locate and remove the vent plug on each transmission
-
Unscrew the filter to remove and allow oil to drain from drive system.
Repeat this procedure for both filters.
Installing the Hydraulic System Filters
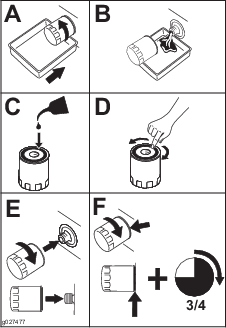
-
Apply a thin coat of the specified oil on the surface of the rubber seal of each filter.
-
Turn the filter clockwise until rubber seal contacts the filter adapter then tighten the filter an additional 3/4 to 1 full turn. Repeat for the other filter
-
Install the filter guards over each filter as previously removed. Use the three screws to secure the filter guards.
-
Verify the vent plugs are removed before adding the oil (Figure 43).
-
Slowly pour the specified oil through expansion reservoir until oil comes out of one of the vent plug holes. Stop and install that vent plug. Torque the plug to 20.3 N-m (180 in-lb).
-
Continue to add oil through the expansion reservoir until oil comes out of the remaining vent plug hole on the second transmission. Stop and install that vent plug. Torque the plug to 20.3 N-m (180 in-lb).
-
Continue to add oil through the expansion reservoir until it reaches the Full Cold line on the expansion reservoir.
-
Proceed to the Bleeding the Hydraulic System section.
Important: Failure to perform the Bleeding the Hydraulic System procedure after changing hydraulic filters and oil can result in irreparable damage to the transaxle drive system.
Bleeding the Hydraulic System
-
Enter the operator's position. Start engine and move throttle control ahead to 1/2 throttle position. Disengage parking brake.
-
Move the bypass levers into the pushing the machine position; refer to Pushing the Machine by Hand. With the bypass valves open and the engine running, slowly move the motion control pedal in both forward and reverse (5 or 6 times).
-
Move the bypass levers into the operating the machine position. With the bypass valve closed and the engine running, slowly move the traction-control pedal in both forward and reverse directions (5 to 6 times).
-
Stop the engine and check the oil level in the expansion reservoir. Add the specified oil as until it reaches the Full Cold line on the expansion reservoir.
-
-
Repeat step 1 until all the air is completely purged from the system.
When the transaxle operates at normal noise levels and moves smoothly forward and reverse at normal speeds, then the transaxle is considered purged.
-
Check the oil level in the expansion reservoir one last time. Add the specified oil as until it reaches the Full Cold line on the expansion reservoir if necessary.
Mower Maintenance
Servicing the Cutting Blades
Maintain sharp blades throughout the cutting season because sharp blades cut cleanly without tearing or shredding the grass blades. Tearing and shredding turns grass brown at the edges, which slows growth and increases the chance of disease.
Check the cutter blades daily for sharpness, and for any wear or damage. File down any nicks and sharpen the blades as necessary. If a blade is damaged or worn, replace it immediately with a genuine Toro replacement blade. For convenient sharpening and replacement, you may want to keep extra blades on hand.
Warning
A worn or damaged blade can break, and a piece of the blade could be thrown into the operator's or bystander's area, resulting in serious personal injury or death.
-
Inspect the blade periodically for wear or damage.
-
Replace a worn or damaged blade.
Before Inspecting or Servicing the Blades
Park the machine on a level surface, disengage the blade-control switch, and ensure the parking brake is engaged. Stop the engine and remove the key.
Inspecting the Blades
Maintenance Service Interval | Maintenance Procedure |
---|---|
Before each use or daily |
|
-
Inspect the cutting edges (Figure 45). If the edges are not sharp or have nicks, remove and sharpen the blades; refer to Sharpening the Blades.
-
Inspect the blades, especially the curved area (Figure 45). If you notice any damage, wear, or a slot forming in this area (items 3 and 4 in Figure 45), immediately install a new blade.
Checking for Bent Blades
Note: The machine must be on a level surface for the following procedure.
-
Raise the mower deck to the highest height-of-cut position; also considered the 'transport' position.
-
While wearing thickly padded gloves or other adequate hand protection slowly rotate blade to be measured into a position that allows effective measurement of the distance between the cutting edge and the level surface the machine is on.
-
Measure from the tip of the blade to the flat surface here.
-
Rotate the same blade 180 degrees so that the opposing cutting edge is now in the same position.
-
Measure from the tip of the blade to the flat surface here. The variance should be no more than 1/8 inch (3mm).
Warning
A blade that is bent or damaged could break apart and could seriously injure or kill you or bystanders.
-
Always replace bent or damaged blade with a new blade.
-
Never file or create sharp notches in the edges or surfaces of blade.
-
If the difference between A and B is greater than 1/8 inch (3mm) replace the blade with a new blade. Refer to Removing the Blades and Installing the Blades.
Note: If a bent blade is replaced with a new one and the dimension obtained continues to exceed 1/8 inch (3mm), the blade spindle could be bent. Contact an Authorized Toro Dealer for service.
-
If the variance is within constraints, move to the next blade..
-
Repeat this procedure on each blade.
Removing the Blades
The blades must be replaced if a solid object is hit, if the blade is out of balance, or the blade is bent. To ensure optimum performance and continued safety conformance of the machine, use genuine Toro replacement blades. Replacement blades made by other manufacturers may result in non-conformance with safety standards.
Hold the blade end using a rag or thickly-padded glove. Remove the blade bolt, curved washer, and blade from the spindle shaft (Figure 50).
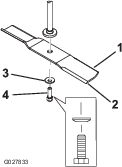
Sharpening the Blades
-
Use a file to sharpen the cutting edge at both ends of the blade (Figure 51). Maintain the original angle. The blade retains its balance if the same amount of material is removed from both cutting edges.
-
Check the balance of the blade by putting it on a blade balancer (Figure 52). If the blade stays in a horizontal position, the blade is balanced and can be used. If the blade is not balanced, file some metal off the end of the sail area only (Figure 51). Repeat this procedure until the blade is balanced.
Installing the Blades
-
Install the blade onto the spindle shaft (Figure 50).
Important: The curved part of the blade must be pointing upward toward the inside of the mower to ensure proper cutting.
-
Install the curved washer (cupped side toward the blade) and the blade bolt (Figure 50).
-
Torque the blade bolt to 35-65 ft-lb (47-88 N-m).
Leveling the Mower Deck
Check to ensure the mower deck is level any time you install the mower or when you see an uneven cut on your lawn.
The mower deck must be checked for bent blades prior to leveling; any bent blades must be removed and replaced. Refer to the Checking for Bent Bladesbefore continuing.
The mower deck must be leveled side-to-side first then the front to rear slope can be adjusted.
Requirements:
-
The machine must be on a level surface.
-
All four tire must be properly inflated. Refer to Checking the Tire Pressure.
Leveling from Side to Side
-
Park the machine on a level surface and disengage the blade-control switch.
-
Ensure the parking brake is engaged, stop the engine, remove the key, and wait for all moving parts to stop before leaving the operating position.
-
Set the height-of-cut lever to middle position.
-
Carefully rotate the blade(s) so that they are all side to side (Figure 53).
-
Measure between the outside cutting edges and the flat surface (Figure 53). If both measurements are not within 5 mm (3/16 inch), an adjustment is required; continue with this procedure.
-
Move to the left side of the machine.
-
Loosen the side locking nut.
-
Raise or lower the left side of the mower deck by rotating the rear nut. (Figure 54).
Note: Rotate the rear nut clockwise to raise the mower deck; rotate the rear nut counter-clockwise to lower the mower deck.
-
Check the side-to-side adjustments again. Repeat this procedure until the measurements are correct.
-
Continue leveling the deck by checking the front-to-rear blade slope; refer to Adjusting the Front-to-Rear Blade Slope.
Adjusting the Front-to-Rear Blade Slope
Check the front-to-rear blade level any time you install the mower. If the front of the mower is more than 7.9 mm (5/16 inch) lower than the rear of the mower, adjust the blade level using the following instructions:
-
Park the machine on a level surface and disengage the blade-control switch.
-
Ensure the parking brake is engaged, stop the engine, remove the key, and wait for all moving parts to stop before leaving the operating position.
-
Set the height-of-cut lever to middle position.
Note: Check and adjust the side-to-side blade level. If you have not checked the setting; refer to Leveling from Side to Side.
-
Carefully rotate the blades so they are facing front to rear (Figure 55).
-
Measure from the tip of the front blade to the flat surface and the tip of the rear blade to the flat surface (Figure 55). If the front blade tip is not 1.6-7.9 mm (1/16-5/16 inch) lower than the rear blade tip, adjust the front locknut.
-
To adjust the front-to-rear blade slope, rotate the adjustment nut in the front of the mower (Figure 56).
-
To raise the front of the mower, tighten the adjustment nut. To lower the front of the mower, loosen the adjustment nut.
-
After adjustment, check the front-to-rear slope again. Continue adjusting the nut until the front blade tip is 1.6-7.9 mm (1/16-5/16 inch) lower than the rear blade tip (Figure 55).
-
When the front-to-rear blade slope is correct check the side-to-side level of the mower again; refer to Leveling from Side to Side.
Removing the Mower
-
Park the machine on a level surface and disengage the blade-control switch.
-
Ensure the parking brake is engaged, stop the engine, remove the key, and wait for all moving parts to stop before leaving the operating position.
-
Lower the height-of-cut lever to the lowest position.
-
Remove the hairpin cotter from the front support rod and remove the rod from the deck bracket (Figure 57). Carefully lower the front of the mower deck to the ground.
-
Using the mower deck handles, lift the mower deck and hanger brackets clear of the rear lift rod and lower the mower carefully to the ground (Figure 58 and Figure 59).
-
Slide the mower deck rearward to remove the mower belt from the engine pulley.
-
Slide the mower deck out from underneath the machine.
Note: Retain all parts for future installation.
Mower Belt Maintenance
Inspecting the Belts
Maintenance Service Interval | Maintenance Procedure |
---|---|
Every 25 hours |
|
Check the belts for cracks, frayed edges, burn marks, or any other damage. Replace damaged belts.
Replacing the Mower Belt
Squealing when the belt is rotating, blades slipping when cutting grass, frayed belt edges, burn marks, and cracks are signs of a worn mower belt. Replace the mower belt if any of these conditions are evident.
-
Park the machine on a level surface and disengage the blade-control switch.
-
Ensure the parking brake is engaged, stop the engine, remove the key, and wait for all moving parts to stop before leaving the operating position.
-
Set the height-of-cut at the lowest cutting position [1-1/2 inch (38 mm)].
-
Using a spring removal tool, (Toro part no. 92-5771), remove the idler spring from the deck hook to remove tension on the idler pulley and roll the belt off of the pulleys (Figure 59).
Warning
The spring is under tension when installed and can cause personal injury.
Be careful when removing the belt.
-
Route the new belt around the engine pulley and mower pulleys (Figure 59).
-
Using a spring removal tool, (Toro part no. 92-5771), install the idler spring over the deck hook and placing tension on the idler pulley and mower belt (Figure 59).
Installing the Mower
-
Park the machine on a level surface and disengage the blade-control switch.
-
Ensure the parking brake is engaged, stop the engine, remove the key, and wait for all moving parts to stop before leaving the operating position.
-
Slide the mower under the machine.
-
Lower the height-of-cut lever to the lowest position.
-
Lift the rear of the mower deck and guide the hanger brackets over the rear lift rod (Figure 58).
-
Attach the front support rod to the mower deck with the clevis pin and hairpin cotter (Figure 57).
-
Install the mower belt onto the engine pulley; refer to Replacing the Mower Belt.
Replacing the Grass Deflector
Maintenance Service Interval | Maintenance Procedure |
---|---|
Before each use or daily |
|
Warning
An uncovered discharge opening could allow the lawn mower to throw objects in the operator’s or bystander’s direction and result in serious injury. Also, contact with the blade could occur.
Never operate the lawn mower unless you install a mulch plate, discharge deflector, or grass collection system.
Inspect the grass deflector for damage before each use. Replace any damaged parts before use.
-
Disengage the spring from the notch in the deflector bracket and slide the rod out of the welded deck brackets, spring, and discharge deflector (Figure 60). Remove the damaged or worn discharge deflector.
-
Position the new discharge deflector with the bracket ends between the welded brackets on the deck as shown in Figure 60.
-
Install the spring onto the straight end of the rod. Position the spring on the rod as shown in so the shorter spring end is coming from under the rod before the bend and going over the rod as it returns from the bend.
-
Lift the loop end of the spring and place it into the notch on the deflector bracket (Figure 61).
-
Secure the rod and spring assembly by twisting it so the short end of the rod can be placed behind the front bracket welded to the deck (Figure 61).
Important: The grass deflector must be spring loaded in the down position. Lift the deflector up to test that it snaps to the full down position.
Cleaning
Cleaning under the Front of the Machine
Maintenance Service Interval | Maintenance Procedure |
---|---|
After each use |
|
Remove debris under the front of the machine with compressed air or by hand with a brush (Figure 62).
Note: Do not use water to clean under the front of the machine, this can cause build up of debris.
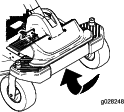
Washing the Underside of the Mower Deck
Maintenance Service Interval | Maintenance Procedure |
---|---|
After each use |
|
Important: You can wash the machine with mild detergent and water. Do not pressure wash the machine. Avoid excessive use of water, especially near the control panel, under the seat, around the engine, hydraulic pumps, and motors.
Wash the underside of the mower after each use to prevent grass buildup for improved mulch action and clipping dispersal.
-
Park the machine on a level surface and disengage the blade-control switch.
-
Ensure the parking brake is engaged, stop the engine, remove the key, and wait for all moving parts to stop before leaving the operating position.
-
Attach the hose coupling to the end of the mower washout fitting, and turn the water on high (Figure 63).
Note: Spread petroleum jelly on the washout fitting O-ring to make the coupling slide on easier and protect the O-ring.
-
Lower the mower to the lowest height-of-cut.
-
Sit on the seat and start the engine. Engage the blade-control switch and let the mower run for one to three minutes.
-
Disengage the blade-control switch, stop the engine, and remove the ignition key. Wait for all moving parts to stop.
-
Turn the water off and remove the coupling from the washout fitting.
Note: If the mower is not clean after one washing, soak it and let it stand for 30 minutes. Then repeat the process.
-
Run the machine and mower blades again for one to three minutes to remove excess water.
-
Turn off the mower blades.
Warning
A broken or missing washout fitting could expose you and others to thrown objects or blade contact. Contact with blade or thrown debris can cause injury or death.
-
Replace broken or missing washout fitting immediately, before using mower again.
-
Never put your hands or feet under the mower or through openings in the mower.
-