Maintenance
Recommended Maintenance Schedule(s)
Maintenance Service Interval | Maintenance Procedure |
---|---|
After the first 25 operating hours |
|
Before each use or daily |
|
Every 50 hours |
|
Every 100 hours |
|
Every 200 hours |
|
Every 300 hours |
|
Monthly |
|
Disconnecting the Spark-Plug Wire
Before performing any maintenance on the engine, disconnect the spark-plug wire from the spark plug (Figure 17).
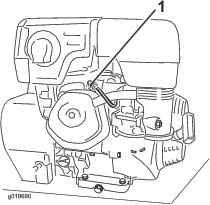
Engine Maintenance
Servicing the Spark Plug
Use an NGK BPR6ES spark plug or equivalent.
-
Shut off the engine and wait for all moving parts to stop.
-
Disconnect the wire from the spark plug.
-
Clean around the spark plug.
-
Remove the spark plug from the cylinder head.
Important: Replace a cracked, fouled, or dirty spark plug. Do not clean the electrodes because grit entering the cylinder can damage the engine.
-
Set the gap on the plug to 0.76 mm (0.03 inch) as shown in .
-
Carefully install the spark plug by hand (to avoid cross threading) until it is hand tight.
-
Tighten the spark plug an additional 1/2 turn if it is new; otherwise, tighten it an additional 1/8 to 1/4 turn.
Important: A loose spark plug can become very hot and can damage the engine; overtightening a spark plug may damage the threads in the cylinder head.
-
Connect the wire to the spark plug.
Servicing the Air Cleaner
Removing the Air Filter
Important: Do not operate the engine without the air filter assembly; extreme engine damage will occur.
-
Set the throttle to slow, shut off the engine, and wait for all moving parts to stop.
-
Disconnect the spark-plug wire from the spark plug.
-
Wipe the air filter cover (Figure 19) so that it is clean.
-
Remove the wing nut that secures the air-filter cover to the carburetor and remove the cover (Figure 19).
Note: Be careful to prevent dirt and debris from falling into the base.
-
Remove the foam filter element from the paper filter element (Figure 19).
-
Inspect the foam element for damage.
Note: If the foam filter element is damaged, replace it. If the foam element is dirty, clean it; refer to Cleaning the Foam Filter.
-
Remove the wing nut that secures the paper filter element to the carburetor (Figure 19).
-
Remove the paper element and inspect the paper filter element for damage and excessive amounts of dirt in the element.
Note: Replace the paper filter element if it is damaged or excessively dirty.
Note: Never try to clean the paper element; only replace it.
Cleaning the Foam Filter
-
Clean the foam filter element in warm soapy water and rinse the element in clean water, or clean the foam filter element in a nonflammable solvent.
Note: Do not use fuel to clean the foam element because it could create a risk of fire or explosion.
-
Allow the foam filter element to completely dry.
-
Dip the foam element in clean engine oil, then squeeze out the excess oil.
Note: If too much oil is left in the foam element when the engine is started, the engine will smoke. Excess oil in the foam element may also restrict the air flow through the element and may reach the paper filter and clog it.
-
Assemble the foam element onto the paper filter element (Figure 19).
Installing the Air Filter
-
Wipe clean the dirt from the carburetor base and the inside of the cover with a moist rag (Figure 19).
Note: Do not allow dirt and debris to enter the air duct leading into the carburetor.
-
Ensure that the rubber gasket is aligned and seated onto the mounting base of the carburetor (Figure 19).
Note: The rubber gasket might stick to the bottom of the old paper filter element. Remove it from the old paper element and install it onto the carburetor.
-
Align the paper filter element with the carburetor and ensure that the hold-down rod of the carburetor passes through the top plate of the filter (Figure 19).
-
Secure the filter to the carburetor with the filter wing nut and tighten it finger tight (Figure 19).
-
Align the air-filter cover over the air filter elements with the hold-down rod of the carburetor passing through the top cover (Figure 19).
-
Secure the cover to the engine with the cover wing nut and tighten it finger tight (Figure 19).
Cleaning the Sediment Cup
Danger
In certain conditions, fuel is extremely flammable and highly explosive. A fire or explosion from fuel can burn you and others and can damage property.
-
Set the throttle to slow, shut off the engine and keep heat, sparks, and flame away.
-
Handle fuel only outdoors.
-
Wipe up spills immediately.
-
Do not smoke while handling fuel.
-
Shut off the engine and wait for all moving parts to stop.
-
Disconnect the wire from the spark plug.
-
Move the fuel-shutoff valve to the OFF position.
-
Remove the sediment cup and O-ring (Figure 6).
-
Wash the sediment cup in a nonflammable solvent and dry it thoroughly.
-
Place the O-ring in the fuel valve and install the sediment cup, tightening it securely.
-
Move the fuel-shutoff lever to the On position.
Note: If any fuel leaks, repeat this procedure and replace the O-ring.
Servicing the Engine Oil
Oil Type: Detergent oil (API service SJ or higher)
Oil crankcase capacity:
-
0.56 L (0.59 US qt) for Model 68025
-
0.58 L (0.61 US qt) for Models 68026 and 68027
Viscosity: See table below
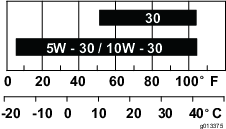
Changing the Engine Oil
Warning
Oil may be hot after the engine has been run, and contact with hot oil can cause severe personal injury.
Avoid contacting the hot engine oil when you drain it.
-
Shut off the engine and wait for all moving parts to stop.
-
Disconnect the wire from the spark plug.
-
Remove the drain plug (Figure 22).
Note: You may have to tip the compactor backwards to drain the oil.
-
When the oil has drained completely, replace the plug.
Note: Dispose of the used oil at a certified recycling center.
-
Remove the dipstick (Figure 7) and slowly pour oil into the filler hole until the oil pours out of the filler hole.
-
Replace and secure the dipstick.
-
Wipe up any spilled oil.
Servicing the Eccentric Oil
Oil type: 10W30 (API service SJ or higher)
Oil capacity:
-
1.3 L (1.4 US qt) for Model 68025
-
3.3 L (3.5 US qt) for Model 68026
-
3.5 L (3.7 US qt) for Model 68027
Checking the Eccentric-Oil Level
-
Set the throttle to slow, shut off the engine, and wait for all moving parts to stop.
-
Place a drain pan under the oil plug and remove the oil-plug screw on the side of the eccentric housing (Figure 23).
-
Verify that the eccentric oil is level with the bolt hole.
-
Wipe up any spilled oil.
-
Replace the oil-plug screw.
Changing the Eccentric Oil
-
Set the throttle to slow, shut off the engine, and wait for all moving parts to stop.
-
Place an oil drain pan under the oil plug and remove the fill plug and the oil plug screw (Figure 23).
-
Tip the plate compactor forward slightly and use a suction gun to remove the oil through the filler hole (Figure 23).
-
Slowly pour oil into the filler hole until the oil comes out the oil plug (Figure 23).
-
Wipe up any spilled oil.
-
Replace the fill plug and the oil plug screw.
Belt Maintenance
Removing the Belt Cover
Checking the Belt Tension
Important: The best belt tension for the machine is the lowest tension at which the belts do not slip under full power.
-
Lay a straight edge on the belt and across the pulleys (Figure 26).
-
With a force gauge, push down on the belt, midway between the pulleys (Figure 26).
Note: The belt should deflect 7.6 mm (0.3 inch) from the straight edge when pushing down on the belt with 1.4 to 2.3 kg (3 to 5 lb) of force (Figure 26).
Note: If the belt tension is too low or too high, adjust the belt tension; refer to Adjusting the Belt Tension.
Adjusting the Belt Tension
-
Remove the water tank; refer to Adding Water with the Tank Removed.
-
Loosen the 2 hex-socket bolts (5/16-24 x 1.75 inches) that secure the front of the engine (Figure 27).
-
Loosen the 2 flange nuts (8 mm) that secure the back of the engine (Figure 28).
-
Loosen the jam nut, and rotate the belt-tensioning bolt clockwise to tension the belt, or rotate the belt-tensioning bolt counterclockwise to loosen the tension on the belt (Figure 28).
-
Check the belt tension; refer to Checking the Belt Tension.
-
When the correct tension is reached, tighten the jam nut on the belt-tensioning bolt.
-
Tighten the 2 hex-socket bolts (5/16-24 x 1-3/4 inches) that secure the front of the engine to 12.5 to 16.4 N∙m (9.2 to 12.1 ft-lb) as shown in Figure 27.
-
Tighten the 2 flange nuts (8 mm) that secure the back of the engine to 23 to 29 N∙m (17 to 21 ft-lb) as shown in Figure 28.
-
Apply medium-grade thread-locking compound to the threads of the flanged-head bolts that you removed in step 1 of Removing the Belt Cover.
-
Align the belt cover to the machine and secure the cover with the flanged-head bolts that you removed in step 1 of Removing the Belt Cover.
-
Torque the bolts to 972 to 1198 N∙cm (86 to 106 in-lb).