Maintenance
Recommended Maintenance Schedule(s)
Maintenance Service Interval | Maintenance Procedure |
---|---|
After the first 25 operating hours |
|
Before each use or daily |
|
Every 40 hours |
|
Every 50 hours |
|
Every 100 hours |
|
Every 150 hours |
|
Every 200 hours |
|
Every 300 hours |
|
Yearly or before storage |
|
Pre-Maintenance Procedures
Disconnecting the Spark-Plug Wire
Before performing any maintenance on the engine, belts, or blades, disconnect the spark-plug wire from the spark plug (Figure 13).
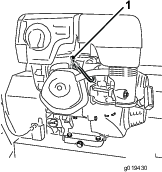
Lubrication
Lubricating the Blade Arms
Grease Type: General-purpose grease.
-
Clean around each grease fitting with a rag and lift the plastic cap off each grease fitting.
-
Pump several shots of grease into each fitting until it starts to ooze out of the bearing (Figure 14 and Figure 15).
Important: Pump grease in slowly and carefully to prevent damage to the bearing seals.
-
Wipe up any excess grease.
Engine Maintenance
Servicing the Air Cleaner
Important: Do not operate the engine without the air-cleaner assembly; extreme engine damage will occur.
-
Set the Dyna-Clutch lever to the STOP position, shut off the engine, and wait for all moving parts to stop.
-
Disconnect the wire from the spark plug.
-
Remove the nut that secures the air-cleaner cover (Figure 16 Box A).
-
Remove the cover (Figure 16 Box B).
Note: Be careful to prevent dirt and debris from falling into the base.
-
Remove the foam and paper elements from the base (Figure 16 Box C).
-
Remove the foam element from the paper element (Figure 16 Box D).
-
Inspect the foam and paper elements, and replace them if they are damaged or excessively dirty.
Note: Never try to brush dirt off the paper element; brushing forces the dirt into the fibers.
-
Clean the foam element in warm, soapy water or in a nonflammable solvent.
Note: Do not use fuel to clean the foam element because it could create a risk of fire or explosion.
-
Rinse and dry the foam element thoroughly.
-
Dip the foam element in clean engine oil, then squeeze out the excess oil.
Note: Excess oil in the foam element restricts the air flow through the element and may reach the paper filter and clog it.
-
Wipe dirt from the base and the cover with a moist rag.
Note: Be careful to prevent dirt and debris from entering the air duct leading to the carburetor.
-
Install the air cleaner elements and ensure that they are properly positioned.
-
Securely install the cover with the nut.
Servicing the Engine Oil
Oil Type: 4-cycle engine oil that meets or exceeds the requirements for API service category SJ or higher
Models | Crankcase Capacity |
---|---|
68048 and 68049 | 0.58 L (0.61 US qt) |
68050 and 68051 | 1.1 L (1.2 US qt) |
Important: If the oil level in the crankcase is too low or too high and you run the engine, you may damage the engine.
Viscosity: Use SAE 10W-30 for general use. You can use the other viscosities shown in the chart when the average temperature in your area is within the indicated range (Figure 8).
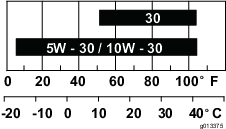
Changing the Engine Oil
Warning
Oil may be hot after the engine has been run, and contact with hot oil can cause severe personal injury.
Avoid contacting the hot engine oil when you drain it.
-
Position the machine on a level surface.
-
Set the Dyna-Clutch lever to the STOP position, shut off the engine, and wait for all moving parts to stop.
-
Disconnect the wire from the spark plug.
-
Place a pan under the drain plug to catch the oil.
-
Remove the drain plug (Figure 18).
-
Replace the plug when the oil has drained completely.
Note: Dispose of the used oil at a certified recycling center.
-
Remove the dipstick (Figure 9) and slowly pour oil into the fill hole until the oil is between the upper and lower fill marks on the dipstick.
-
Install and secure the dipstick.
-
Wipe up any spilled oil.
Servicing the Gearcase Oil
Oil Type: 80W-90 gear oil that meets or exceeds API service category GL-5.
Capacity: 1.18 L (1.25 US qt)
-
Set the Dyna-Clutch lever to the STOP position, shut off the engine, and wait for all moving parts to stop.
-
Disconnect the wire from the spark plug.
-
Place a pan under the drain plug to catch the oil.
-
Remove the gearcase plug (Figure 18).
-
Tip the machine and drain the oil completely out of the gearcase.
Note: Dispose of the used oil at a certified recycling center.
-
Return the machine to an upright, level position.
-
Place a 3.8 cm (1-1/2 inch) block under the stationary blade guard (outer ring) so that the side of the gearbox with the plug is approximately 6 mm (1/4 inch) higher than the other side of the gearbox.
-
Slowly pour oil into the plug hole until the oil reaches the threads of the hole.
Note: If necessary, use a flexible funnel.
-
Apply thread-sealing compound to the threads of the plug.
-
Install and tighten the plug until it is secure, and return the machine to an upright, level position.
Note: The oil level in the sight glass of the plug should be 3/4 full (Figure 20).
Servicing the Spark Plug
Use an NGK BPR6ES spark plug or equivalent.
-
Set the Dyna-Clutch lever to the STOP position, shut off the engine, and wait for all moving parts to stop.
-
Disconnect the wire from the spark plug.
-
Clean around the spark plug.
-
Remove the spark plug from the cylinder head.
Important: Replace a cracked, fouled, or dirty spark plug. Do not clean the electrodes, because grit entering the cylinder can damage the engine.
-
Set the gap on the plug to 0.76 mm (0.030 inch); refer to Figure 21.
-
Carefully install the spark plug by hand (to avoid cross threading) until it is hand tight.
-
Tighten the spark plug an additional 1/2 turn if it is new; otherwise, tighten it an additional 1/8 to 1/4 turn.
Important: A loose spark plug can become very hot and can damage the engine; overtightening a spark plug may damage the threads in the cylinder head.
-
Connect the wire to the spark plug.
Belt Maintenance
Checking the Belt, Pulley Alignment, Belt Tension, and Belt-Guide Gap
-
Remove the belt guard; refer to Removing the Belt Guard.
-
Move the Dyna-Clutch lever to the STOP position.
-
Check the condition of the belt for wear or damage.
Note: If the belt is worn or damaged, replace the belt; refer toRemoving the Belt and Installing the Belt.
-
Move the Dyna-Clutch lever to the RUN position.
-
Check that the belt is aligned straight between pulleys.
Note: If the belt does not run straight between pulleys, align the pulleys; refer to Aligning the Pulleys.
-
Check that the belt has enough tension to flatten it between the engine pulley and the belt tension pulley.
Note: If belt tension is too low, adjust the tension of the belt-tension pulley; refer to Adjusting the Dyna-Clutch.
-
Measure the gap between the belt and the belt guide. The air gap should be approximately 6 mm (1/4 inch).
Note: If the air gap is larger or smaller than 6 mm (1/4 inch), adjust the belt guide (Figure 26); refer to Adjusting the Belt Guide.
-
Install the belt guard; refer to Installing the Belt Guard.
Removing the Belt Guard
Installing the Belt Guard
-
Align the holes in the belt guard with the holes in the belt-cover bracket (Figure 22).
-
Secure the belt guard to the bracket with the 2 hex-washer head bolts (5/16 x 1 inch).
Removing the Belt
-
Position the machine on a level surface, place the Dyna-Clutch lever in the STOP position, shut off the engine, and disconnect the spark-plug wire.
-
Remove the belt guard; refer to Removing the Belt Guard.
-
Slip the belt off the belt-tension pulley (Figure 23).
-
Slip the belt off the gearbox pulley (Figure 23).
-
Slip the belt off the engine pulley and remove the belt (Figure 23).
Installing the Belt
-
Ensure the Dyna-Clutch lever in the STOP position.
-
Align the belt over the engine pulley (Figure 23).
-
Align the belt over the gearbox pulley (Figure 23).
-
Slip the belt over the belt-tension pulley (Figure 23).
-
Install the belt guard; refer to Installing the Belt Guard.
Aligning the Pulleys
-
Place a straight-edge ruler across the engine pulley and the gearbox pulley (Figure 24).
-
If the pulleys are out of alignment, perform the following steps:
-
Loosen the 2 setscrews that secure the engine pulley to the engine shaft (Figure 24).
-
Gently tap the engine pulley toward or away from the engine until the gearbox and engine pulleys align to the straight-edge ruler (Figure 24).
-
Tighten the 2 setscrews that secure the engine pulley to the engine shaft (Figure 24).
-
Adjusting the Dyna-Clutch
Important: This adjustment procedure affects the operation of the Dyna-Clutch and is critical to the safe operation of the machine.
Adjust the tension-pulley spring as needed to tighten the belt.
-
Move the Dyna-Clutch lever to the STOP position; refer to Dyna-Clutch Lever.
-
Loosen the 2 jam nuts that secure the barrel of the clutch cable to the clutch bracket, and rotate the nuts to either end of threads on the barrel (Figure 25).
-
Grasp the barrel with 1 hand and lift the cable housing lightly (Figure 25).
Note: Lifting the cable housing at the barrel should remove the slack from the cable but apply no tension to the spring.
-
While holding tension on the cable, use your other hand, rotate the jam nuts until the nuts are flush to the clutch bracket (Figure 25).
-
Tighten the jam nuts to secure the barrel to the bracket (Figure 25).
-
Check the tension of the control cable. Repeat steps 2 through 4 until there is tension on the Dyna-Clutch cable but no tension on the spring.
Note: If there is too much tension on the cable and spring, the Dyna-Clutch will not release completely. If there is not enough tension on the cable, the cable may disconnect from the pulley bracket.
-
If you need to make a finer cable adjustment, perform the following:
-
Start the machine and set Dyna-Clutch to the RUN position for a few moments, then move the Dyna-Clutch to the STOP position.
Note: If the blades continue to rotate when the Dyna-Clutch is in the STOP position, there is too much tension on the clutch cable. Shut off the engine and repeat step 7 until the blades do not rotate when the engine is running and the Dyna-Clutch is in the STOP position.
Adjusting the Belt Guide
-
Place the Dyna-Clutch lever in the RUN position.
-
Measure the air gap between the belt and the belt guide (Figure 26).
The air gap should be approximately 6 mm (1/4 inch). If an adjustment needs to be done, perform the following:
-
Loosen the hex-flange head bolt that secures the belt guide to the engine plate (Figure 26).
-
While keeping the top of the belt guide parallel to the belt, move the belt guide toward or away from the belt until the air gap is correct (Figure 26).
-
Tighten the hex-flange head bolt that secures the belt guide to the engine plate (Figure 26).
Controls System Maintenance
Adjusting the Tilt Knob
-
Set the Dyna-Clutch lever to the Stop position, shut off the engine, and wait for all moving parts to stop.
-
Disconnect the wire from the spark plug.
-
Attach an overhead lift to the lifting point on the machine and lift it off of the ground.
-
Turn the tilt knob until there is enough cable slack to access the tilt locknut (Figure 27).
-
Tighten the locknut against the bearing then loosen it slightly. Set it with the set screw (Figure 27).
-
Adjust the nuts inside the tilt block to take up any cable slack.
Note: Replace the cables if full tilt is no longer obtainable.
Adjusting the ProPitch Linkage Rod
-
Set the Dyna-Clutch lever to the Stop position, shut off the engine, and wait for all moving parts to stop.
-
Disconnect the wire from the spark plug.
-
Attach an overhead lift to the lifting point on the machine and lift if off of the ground.
-
Loosen the nut on the upper end of the linkage rod to allow slack in the lift cable (Figure 28).
-
Position the ProPitch handle in the full tilt position.
-
Adjust the nut on the backside of the swivel at the upper end of the linkage rod until you achieve the proper gap of approximately 0.4 mm (1/64 inch) between the tilt lever and the gearcase.
-
Tighten the nut on the outside of the swivel to lock the linkage rod into position.
Testing the Dyna-Clutch Lever
Testing the Dyna-Clutch Operation
Ensure that the area is clear of any debris or bystanders before beginning the testing procedures.
-
Start the trowel, engage the Dyna-Clutch lever, and run the machine for a few moments.
-
Move the Dyna-Clutch lever to the Stop position.
-
Watch the blades for any sign of continued rotation.
If the blades do not stop, there is too much tension on the cable and spring. Shut off the engine and decrease the amount of tension to allow the Dyna-Clutch lever to disengage completely.
Ensure that there is still enough tension on the cable and spring to prevent parts from coming unhooked during operation. If the tendency for the blades to rotate when the Dyna-Clutch lever is disengaged cannot be adjusted out of the system without taking all tension off of the cable and spring, carefully inspect the drive belt and Dyna-Clutch lever system for wear or damage. Ensure that all parts are operating freely. If the Dyna-Clutch lever does not stop the blades, see an Authorized Service Dealer.
Testing the Dyna-Clutch Lever Adjustment
Important: Ensure that the testing of the Dyna-Clutch lever is done is a clear and open area.
Important: Clear the test area of bystanders.
-
Move the Dyna-Clutch lever to the STOP position; refer to Dyna-Clutch Lever.
-
Start the trowel.
-
Move the fuel valve to the OFF position (Figure 29).
Important: You must move the fuel valve to the OFF position before continuing this procedure.
-
Hold onto the handle and engage the Dyna-Clutch lever; refer to Dyna-Clutch Lever.
-
Let go of the handle.
The Dyna-Clutch lever should switch to the STOP position within 1 rotation. If it does not, keep clear of the area and wait for the machine to run out of fuel.
Note: If the Dyna-Clutch does not stop the machine within 1 rotation, adjust the Dyna-Clutch or bring the machine to an authorized service location; refer to Adjusting the Dyna-Clutch.
-
Move the Dyna-Clutch lever to the STOP position.
Adjusting the Blades
Adjust the blades to remove excessive shaking of the machine.
-
Disconnect the spark plug wire and move the Dyna-Clutch lever to the STOP position.
-
Place 3 or 4 blocks of equal height under the stationary blade guard (outer ring) to raise the blades off of the floor.
Note: Ensure that the blocks are clear of the blades so that the blades can be rotated without touching the blocks.
-
Measure from the floor to the leading edge of the blade. Note the measurement.
-
Place a mark on the blade and on the spot on the floor from where the measurement was taken (Figure 31).
-
Rotate the blades until the next blade is in the same position as the previously measured blade.
-
Measure the second blade from the spot previously marked on the floor to the second blades leading edge (Figure 32).
-
Compare the 2 measurements.
If the height of the second blade is not within 0.8 mm (1/32 inch) of the height of the first blade, adjust the second blade.
-
Loosen the locknuts on the blade (Figure 33).
-
Adjust the blade arm lever up or down as necessary to make the second blade height the same height of the first blade that was measured.
-
Tighten the locknuts.
-
Repeat as necessary for the remaining blades.
Adjusting the Blade Arms
Adjust the blade arms if the machine still shakes excessively after the blades have been adjusted.
-
Place the machine on a flat surface.
-
Disconnect the spark plug.
-
Turn the tilt adjustment knob counter clockwise until all of the tension is off of the tilt adjustment cable and the blades are flat against the floor.
Blade arms should be unbent and flat to the floor. If a blade is bent, continue this procedure to adjust the blade arm. If blades are unbent and flat to the floor, examine the machine for other worn parts.
Note: Do not screw the knob completely out of the handle.
-
Loosen the bolts 3 to 4 turns (Figure 34).
-
Loosen the locknut and tighten the outermost bolt until the blade lays flat against the floor.
-
Tighten the locknut and bolts.
-
Repeat for other blades as necessary.
If the blade arm cannot be adjusted to lay flat, replace the blade arm.
If the machine continues shaking excessively after the blade arms have been adjusted, examine the remainder of the machine for any other worn parts.