Maintenance
Note: Determine the left and right sides of the machine from the normal operating position.
Important: You can tip the machine backward or on its side to clean or service it, but no longer than 2 minutes. If you hold the machine this position for too long, fuel can drain into the crankcase and damage the engine. Should this happen, perform an extra oil change on the engine. Then turn the engine over a few revolutions with the starter handle before starting the engine again.
Recommended Maintenance Schedule(s)
Maintenance Service Interval | Maintenance Procedure |
---|---|
After the first 20 hours |
|
Before each use or daily |
|
Every 50 hours |
|
Every 100 hours |
|
Every 300 hours |
|
Every 600 hours |
|
Yearly or before storage |
|
Important: Refer to your engine owner’s manual for additional maintenance procedures.
Lubrication
Greasing the Machine
Maintenance Service Interval | Maintenance Procedure |
---|---|
Before each use or daily |
|
Grease Type: General-purpose grease.
-
Park the machine on a level surface and engage the parking brake.
-
Shut off the engine and wait for all moving parts to stop.
-
Clean the grease fittings with a rag.
-
Connect a grease gun to each fitting.
-
Lubricate the 2 fittings, 1 on each cutting-wheel bearing.
-
Pump grease into the fittings until grease begins to ooze out of the bearings (approximately 3 pumps).
Important: Pump grease in slowly and carefully to prevent damage to the bearing seals.
-
Wipe up any excess grease from the fitting and bearing area.
Engine Maintenance
Servicing the Air Cleaner
Maintenance Service Interval | Maintenance Procedure |
---|---|
Before each use or daily |
|
Every 50 hours |
|
Every 600 hours |
|
The cyclone air filter collects the largest contaminant particles, which collect in the container. When you can see a layer of dirt at the bottom of the container, clean the cyclone housing, air channels, and air-intake screen.
Servicing the Cyclone Housing
-
Park the machine on a level surface and engage the parking brake.
-
Shut off the engine and wait for all moving parts to stop.
-
Remove the 3 screws holding the cyclone housing to the air-cleaner cover.
-
Remove the housing with the air-intake screen and remove the air channels.
-
Clean the components with water, detergent, and a brush then dry the components carefully.
-
Place the air channels in the cyclone housing.
-
Insert cyclone housing into position and make sure that it fits in the upper portion.
Important: Do not use force; align it in place before fitting the screws.
-
Secure the cyclone housing using the 3 screws.
Servicing the Air-Cleaner Elements
Removing the Foam and Paper Elements
-
Park the machine on a level surface and engage the parking brake.
-
Shut off the engine and wait for all moving parts to stop.
-
Remove the wing nut and lift off the air-cleaner cover with the air-filter cowling (Figure 15).
-
Remove the foam element (Figure 15).
-
Remove the wing nut on top of the paper element and remove the paper element (Figure 15).
Servicing the Foam Air-Cleaner Element
-
Wash the foam element using a mild detergent and water.
-
Squeeze it dry with a clean cloth.
-
Soak it with new engine oil.
-
Gently squeeze out excess oil from the element in an absorbent cloth.
Servicing the Paper Air-Cleaner Element
-
Clean the paper element by tapping it gently to remove dust. If it is very dirty, replace the paper element (Figure 15).
-
Inspect the element for tears, an oily film, or damage to the rubber seal.
-
Replace the paper element if it is damaged.
Important: Do not clean the paper filter.
Installing the Foam and Paper Elements
-
Mount the paper element in the air-cleaner housing and secure it with the wing nut.
-
Position the foam element over the paper element.
-
Install the air-cleaner cover and secure it with the wing nut.
Servicing the Engine Oil
Maintenance Service Interval | Maintenance Procedure |
---|---|
After the first 20 hours |
|
Before each use or daily |
|
Every 100 hours |
|
Yearly or before storage |
|
Engine-Oil Specifications
Note: Change the oil more frequently when the operating conditions are extremely dusty or sandy.
Oil Type: Detergent oil with an API service of SJ or higher.
Crankcase Capacity: 1.1 L (1.2 US qt)
Viscosity: Refer to the figure below.
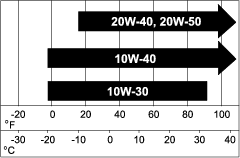
Checking the Engine-Oil Level
-
Park the machine on a level surface and engage the parking brake.
-
Shut off the engine and wait for all moving parts to stop.
-
Check the engine-oil level as shown in Figure 17.
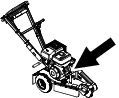
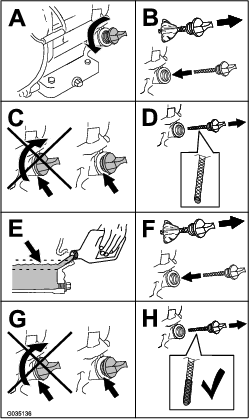
Changing the Engine Oil
-
Start the engine and let it run for 5 minutes.
Note: This warms the oil so that it drains better.
-
Park the machine on a level surface and engage the parking brake.
-
Shut off the engine and wait for all moving parts to stop.
-
Change the oil as shown in (Figure 18).
-
Slowly pour approximately 80% of the specified oil into the filler tube and slowly add the additional oil to bring it to the Full mark (Figure 19).
-
Dispose of the used oil at a recycling center.
Servicing the Spark Plug
Maintenance Service Interval | Maintenance Procedure |
---|---|
Every 100 hours |
|
Every 300 hours |
|
Ensure that the air gap between the center and side electrodes is correct before installing the spark plug. Use a spark plug wrench for removing and installing the spark plug and a gapping tool/feeler gauge to check and adjust the air gap. Install a new spark plug if necessary.
Type: BPR6ES (NKG) or equivalent
Air Gap: 0.70 to 0.80 mm (0.28 to 0.031 inch)
Removing the Spark Plug
-
Park the machine on a level surface and engage the parking brake.
-
Shut off the engine, wait for all moving parts to stop, and allow the engine to cool.
-
Locate and remove the spark plug (Figure 20).
Checking the Spark Plug
Important: Do not clean the spark plug(s). Always replace the spark plug(s) when it has: a black coating, worn electrodes, an oily film, or cracks.
If you see light brown or gray on the insulator, the engine is operating properly. A black coating on the insulator usually means the air cleaner is dirty.
Set the gap to 0.70 to 0.80 mm (0.28 to 0.031 inch).
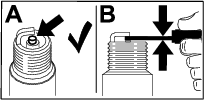
Installing the Spark Plug
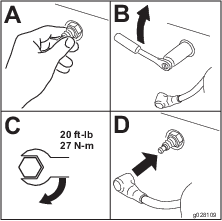
Fuel System Maintenance
Cleaning the Sediment Cup
Maintenance Service Interval | Maintenance Procedure |
---|---|
Every 100 hours |
|
Yearly or before storage |
|
Underneath the fuel valve is a sediment cup to catch dirt in the fuel.
-
Park the machine on a level surface and engage the parking brake.
-
Shut off the engine and wait for all moving parts to stop.
-
Move the fuel valve to the OFF position, all the way to the left.
-
Unscrew the sediment cup (Figure 23).
-
Clean the reservoir and the O-ring using a cleaning solvent and dry carefully.
Note: Make sure not to misplace the O-ring.
-
Place the O-ring in the groove of the cup and replace the sediment cup.
-
Turn the fuel valve to the ON position, all the way to the right, and check for leaks.
Note: If it leaks, replace the O-ring.
Cooling System Maintenance
Cleaning the Engine Screen
Maintenance Service Interval | Maintenance Procedure |
---|---|
Before each use or daily |
|
Before each use, remove any buildup of grass, dirt, or other debris from the engine screen. This helps ensure adequate cooling and correct engine speed and reduces the possibility of overheating and mechanical damage to the engine.
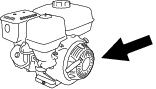
Brake Maintenance
Adjusting the Parking Brake
-
Park the machine on a level surface and engage the parking brake.
-
Shut off the engine and wait for all moving parts to stop.
-
Loosen the set screw on the side of the brake-lever knob. Turn the knob clockwise to tighten the brake; turn the knob counterclockwise to loosen the brake.
Note: The left wheel should lock completely when you engage the brake.
-
Tighten the set screw.
Belt Maintenance
Adjusting the Drive-Belt Tension
Maintenance Service Interval | Maintenance Procedure |
---|---|
Before each use or daily |
|
Note: Inspect the drive belt through the slot on top of the belt cover. Adjust as required.
-
Park the machine on a level surface and engage the parking brake.
-
Shut off the engine and wait for all moving parts to stop.
-
Loosen the 2 bolts securing the belt guard to machine until you can remove the belt guard (Figure 25).
Note: The bolts and washers will remain attached to the belt guard.
-
Remove the belt guard (Figure 25).
-
Loosen the 4 engine-plate mounting bolts and the 2 bolts securing the rear of the belt guard to the engine (Figure 26 and Figure 27).
-
Loosen the belt-tension bolt and jam nut. Slide the engine toward the flywheel housing to loosen the belt (Figure 27).
-
Adjust the drive-belt tension by tightening tension bolt and jam nut against the engine mounting plate, pushing the engine rearward.
-
Lay a straightedge across the clutch and flywheel pulleys. Tighten the belt-tension bolt so there is 10 mm (0.40 inch) of flex in the belt when pushing down with 6.8 kg (15 lb) force at mid-span (when re-tensioning a belt in use), or with 8 kg (18 lb) force when installing a new belt (Figure 28).
-
Ensure that the pulleys are aligned and the engine is parallel with the frame (not angled toward the side), then tighten the 4 engine-plate mounting bolts and the 4 bolts securing the rear of the belt guard to the engine.
-
Install the belt guard and tighten the bolts (Figure 25).
Replacing the Drive Belt
Maintenance Service Interval | Maintenance Procedure |
---|---|
Every 100 hours |
|
Note: Replace the belt if it shows any signs of wear, cracks, glazing, or damage.
-
Park the machine on a level surface and engage the parking brake.
-
Shut off the engine and wait for all moving parts to stop.
-
Loosen the bolts securing the belt guard to machine until you can remove the belt guard.
-
Remove the belt guard (Figure 25).
-
Loosen the 4 engine-plate mounting bolts and the 2 bolts securing the rear of the belt guard to the engine (Figure 26 and Figure 27).
-
Loosen the belt tension bolt and jam nut and slide the engine toward the flywheel housing to loosen the belt (Figure 27).
-
Replace the drive belt.
-
Adjust the tension of the new belt to 8 kg (18 lb) force and 10 mm (0.40 inch) belt deflection at mid-span; refer to Adjusting the Drive-Belt Tension..
-
Tighten the 4 engine-plate mounting bolts and the 4 bolts securing the rear of the belt guard to the engine.
-
Install the belt guard and secure it with the previously removed washers and bolts.
Grinder Maintenance
Replacing the Teeth
Maintenance Service Interval | Maintenance Procedure |
---|---|
Before each use or daily |
|
Due to the high amount of wear placed on the teeth, you need to rotate and replace them periodically (Figure 29). Before you rotate or replace them, inspect each tooth holder on the wheel, including the flat lands that prevent the teeth from rotating. If the tooth holder is damaged, replace the wheel. Torque the nuts 68 N∙m (50 ft-lb) for any teeth that you are not rotating or replacing.
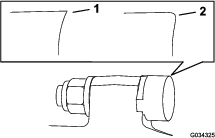
Each tooth is indexed with 3 positions so you can rotate it twice, exposing a new sharp edge before replacing the tooth. To rotate a tooth, loosen the nut securing the tooth (Figure 30). Push the tooth forward and rotate it 1/3 of a turn, bringing an unused edge to the outside. Torque the nut securing the tooth to 68 N∙m (50 ft-lb).
To replace a tooth, remove the nut securing the tooth, then install a new tooth, washer, and nut in the same position (Figure 30). Torque the nut securing the tooth to 68 N∙m (50 ft-lb).
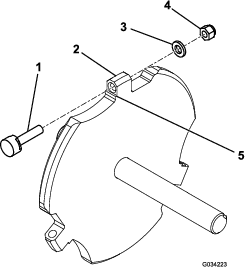
Cleaning
Removing Debris from the Machine
Maintenance Service Interval | Maintenance Procedure |
---|---|
Before each use or daily |
|
Regular cleaning and washing increases the life span of the machine. Clean the machine directly after use, before the dirt hardens.
Before cleaning, check that the fuel-tank cap is properly in place to avoid getting water in the tank.
Use care when using a high-pressure sprayer, because it can damage warning decals, instruction signs, and the engine
Important: Lubricate the cutting wheel bearings after cleaning.