Maintenance
Warning
Failure to properly maintain the machine could result in premature failure of machine systems causing possible harm to you or bystanders.
Keep the machine well maintained and in good working order as indicated in these instructions.
Note: Determine the left and right sides of the machine from the normal operating position.
Note: Download a free copy of the electrical or hydraulic schematic by visiting www.Toro.com and searching for your machine from the Manuals link on the home page.
Important: Refer to your engine owner's manual for additional maintenance procedures.
Caution
If you leave the key in the ignition switch, someone could accidently start the engine and seriously injure you or other bystanders.
Remove the key from the ignition and disconnect the wires from the spark plugs before you do any maintenance. Set the wires aside so that they do not accidentally contact the spark plugs.
Recommended Maintenance Schedule(s)
Maintenance Service Interval | Maintenance Procedure |
---|---|
After the first operating hour |
|
After the first 10 operating hours |
|
After the first 25 operating hours |
|
After the first 50 operating hours |
|
Before each use or daily |
|
Every 50 hours |
|
Every 100 hours |
|
Every 200 hours |
|
Every 800 hours |
|
Every 2 years |
|
Pre-Maintenance Procedures
Maintenance Safety
-
Before adjusting, cleaning, repairing, or leaving the machine, do the following:
-
Park the machine on a level surface.
-
Move the throttle switch to the low-idle position.
-
Disengage the cutting units.
-
Lower the cutting units.
-
Ensure that the traction is in neutral.
-
Engage the parking brake.
-
Shut off the engine and remove the key.
-
Wait for all moving parts to stop.
-
Allow machine components to cool before performing maintenance.
-
-
If the cutting units are in the transport position, use the positive mechanical lock (if available) before you leave the machine unattended.
-
If possible, do not perform maintenance while the engine is running. Keep away from moving parts.
-
Use jack stands to support the machine or components when required.
-
Carefully release pressure from components with stored energy.
Removing the Seat Assembly
Note: If you remove the seat assembly frequently, you can replace the roll pin with an R-key pin (Part No. 3290-467).
Remove the seat assembly to access the valve block area of the machine.
-
Unlatch and raise the seat, securing it with the prop rod.
-
Disconnect the 2 wire-harness connectors under the seat.
-
Lower the seat and remove the roll pin securing the seat-pivot rod to the frame (Figure 28).
-
Slide the seat-pivot rod to the left.
-
Move the seat forward and lift it out of the machine.
-
Reverse the procedure to install the seat.
Raising the Machine
Caution
If the machine is not properly supported, it could fall, crushing you or others.
Before servicing, support the machine with jack stands or blocks of wood.
Before raising the machine, lower the cutting units. The jacking points are as follows:
-
Right side—under the jack pad and adjacent to the ROPS-support bracket (Figure 29)
-
Left side—under the step
-
Rear—at the caster fork
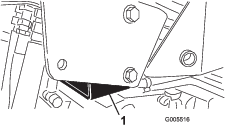
Lubrication
Greasing the Machine
Lubricate the grease fittings regularly with No. 2 lithium grease.
Locate the grease fitting as follows:
-
Rear-roller-hub assembly or, if equipped with a 3-wheel-drive kit, rear-wheel-roller clutches and external ball bearing (1) (Figure 30)
-
Steering-fork shaft (1) (Figure 31)
-
Steering-cylinder-rod end (Figure 31)
-
Lift-arm pivot (3) and pivot hinge (3) (Figure 32)
-
Pull-frame shaft and roller (12) (Figure 33)
-
Steering-cylinder end (Figure 34)
-
Lift cylinders (3) (Figure 35)
-
Traction pedal (Figure 36)
-
Speed-selector linkage (Figure 37 and Figure 38)
-
Wipe the grease fitting clean so foreign matter cannot be forced into the bearing or bushing.
-
Pump grease into the bearing or bushing until the grease is visible. Wipe up excess grease.
-
Apply grease to the reel motor spline shaft and onto the lift arm when you remove the cutting unit for service.
-
Apply a few drops of SAE 30 engine oil or spray lubricant (WD 40) to all pivot points daily after cleaning.
Engine Maintenance
Engine Safety
-
Shut off the engine before checking the oil or adding oil to the crankcase.
-
Do not change the governor speed or overspeed the engine.
Servicing the Air Cleaner
-
Clean the air-cleaner cover (Figure 39).
-
Release the locking clips and remove the air-cleaner cover.
-
Remove the wing nut securing the elements to the air-cleaner body (Figure 40).
-
If the foam element is dirty, remove it from the paper element (Figure 40). Clean it thoroughly, as follows:
-
Wash the foam element in a solution of liquid soap and warm water. Squeeze it to remove dirt.
-
Dry it by wrapping it in a clean rag. Squeeze the rag and foam element dry.
Important: When drying the foam element, do not twist it; the foam may tear.
-
-
Check the condition of the paper element. Clean it by gently tapping it on a flat surface or replace it if needed.
-
Install the foam element, paper element, wing nut, and air-cleaner cover.
Important: Do not operate the engine without the air-cleaner element because extreme engine wear and damage will likely result.
Servicing the Engine Oil
The engine is shipped with oil in the crankcase; however, you must check the oil level before and after starting the engine the first time.
Engine Oil Specification
API Oil Service Classification: SJ or higher
Oil Viscosity: SAE 30
Note: Uses any high-quality detergent oil.
Checking the Engine Oil
-
Park the machine on a level surface, shut off the engine and remove the key.
-
Unscrew the dipstick, remove it, and wipe it with a clean rag.
-
Insert the dipstick into the dipstick tube and thread it into the tube (Figure 41).
-
Unscrew the dipstick, pull it out of the tube, and check the oil level.
-
If the oil level is low, remove the filler cap from the valve cover and add oil into the engine through the filler neck until the oil level is up to the FULL mark on the dipstick.
Add the oil slowly and check the level often during this process.
Important: Do not overfill the engine with oil.
-
Install the filler cap and dipstick.
Changing the Engine Oil and Filter
Engine oil quantity: 1.4 L (1.5 US qt) with filter
-
Remove the drain plug (Figure 42) and let the oil flow into a drain pan.
-
Clean the threads of the drain plug, apply PTFE sealant, and install the drain plug (Figure 42).
-
Remove the oil filter (Figure 42).
-
Apply a light coat of clean oil to the new filter gasket.
-
Thread the oil filter onto the engine by hand until the gasket contacts the filter adapter, then tighten the filter 3/4 to 1 turn further.
Important: Do not overtighten the oil filter.
-
Add oil to the crankcase; refer to Engine Oil Specification and Checking the Engine Oil.
-
Dispose of the oil filter and used oil properly.
Replacing the Spark Plugs
Spark plug specification: Champion RC 14YC
Air gap specification: 0.76 mm (0.030 inch)
-
Clean the area around the spark plugs so that foreign matter cannot fall into the cylinder.
-
Pull the wires off the spark plugs and remove the plugs.
-
Check the condition of the side electrode, center electrode, and center electrode insulator to ensure that there is no damage.
Important: Replace a cracked, fouled, dirty, or otherwise malfunctioning spark plug. Do not sand blast, scrape, or clean electrodes by using a wire brush because grit may eventually release from the plug, fall into the cylinder, and damage the engine.
-
Set the air gap between the center and side of the electrodes at 0.76 mm (0.030 inches) as shown in Figure 43.
-
Install the spark plug and gasket seal, and torque the plug to 23 N∙m (200 in-lb).
Fuel System Maintenance
Replacing the Fuel Filter
The in-line fuel filter is in the fuel line between the fuel tank and carburetor (Figure 44).
Danger
In certain conditions, fuel is extremely flammable and highly explosive. A fire or explosion from fuel can burn you and others and can damage property.
-
Drain fuel from the fuel tank when the engine is cold. Do this outdoors in an open area. Wipe up any fuel that spills.
-
Never smoke when draining fuel, and stay away from an open flame or where a spark may ignite the fumes.
-
Close the fuel-shutoff valve (Figure 44).
-
Place a drain pan under the filter, loosen the hose clamp on the carburetor side of filter, and remove the fuel line from the filter (Figure 44).
-
Loosen the other hose clamp and remove the filter (Figure 44).
-
Install the new filter with the arrow on the filter body pointing away from the fuel tank.
Inspecting the Fuel Lines and Connections
Inspect the fuel lines for deterioration, damage, or loose connections.
Electrical System Maintenance
Electrical System Safety
-
Disconnect the battery before repairing the machine. Disconnect the negative terminal first and the positive last. Connect the positive terminal first and the negative last.
-
Charge the battery in an open, well-ventilated area, away from sparks and flames. Unplug the charger before connecting or disconnecting the battery. Wear protective clothing and use insulated tools.
Servicing the Battery
Properly maintain the battery electrolyte and keep the top of the battery clean. Store the machine in a cool place to prevent the battery from running down.
The battery cables must be tight on the terminals to provide good electrical contact.
Danger
Battery electrolyte contains sulfuric acid which can be fatal if consumed and causes severe burns.
-
Do not drink electrolyte and avoid contact with skin, eyes, or clothing. Wear safety glasses to shield your eyes and rubber gloves to protect your hands.
-
Fill the battery where clean water is always available for flushing the skin.
-
Check the electrolyte level in the cells of the battery.
-
If needed, add distilled or demineralized water into the cell of the battery.
Note: Only raise the electrolyte level to the bottom of the split ring inside each cell.
-
Clean the top of the battery by washing it periodically with a brush dipped in ammonia or bicarbonate of soda solution.
-
Flush the top surface of the battery with water after cleaning it.
Important: Do not remove the fill caps while cleaning the battery.
Warning
Incorrect battery cable routing could damage the machine and cables causing sparks. Sparks can cause the battery gasses to explode, resulting in personal injury.
-
Always disconnect the negative (black) battery cable before disconnecting the positive (red) cable.
-
Always connect the positive (red) battery cable before connecting the negative (black) cable.
If corrosion occurs at the terminals, disconnect the cables, negative (-) cable first, and scrape the clamps and terminals separately. Connect the cables, positive (+) cable first, and coat the terminals with petroleum jelly.
Locating the Fuses
The fuses in the electrical system of the machine are located under the seat (Figure 45).

Drive System Maintenance
Checking the Tire Pressure
Vary the tire pressure for the front wheels, depending upon your turf conditions, from a minimum of 55 kPa (8 psi) to a maximum of 83 kPa (2 psi).
Vary the tire pressure for the rear wheel from a minimum of 55 kPa (8 psi) to a maximum of 103 kPa (15 psi).
Checking the Torque of the Wheel Nuts
Warning
Failure to maintain proper torque of the wheel nuts could result in personal injury.
Torque the wheel nuts to the specified torque at the specified intervals.
Wheel nut torque specification: 95 to 122 N∙m (70 to 90 ft-lb)
Note: To ensure even distribution, torque the wheel nuts in a X pattern.
Adjusting the Transmission for Neutral
If the machine creeps when the traction control pedal is in the NEUTRAL position, adjust the neutral-return mechanism.
-
Block up under the frame so that one of the front wheels is off of the floor.
Note: If the machine is equipped with a 3-Wheel Drive Kit, raise and block the rear wheel.
-
Start the engine, move the throttle to the SLOW position, and ensure that the front wheel that is off of the floor is not rotating.
-
If the wheel is rotating, shut off the engine and proceed as follows:
-
Loosen both jam nuts securing the traction-control cable to the bulkhead on the hydrostat (Figure 46). Ensure that the jam nuts are loosened equally and sufficiently to allow adjustment.
Note: Loosen the nut securing the eccentric to the top of the hydrostat (Figure 46).
-
Move the functional-control lever to the NEUTRAL position and the throttle lever to the SLOW position.
-
Start the engine.
-
Rotate the eccentric until creep does not occur in either direction.
-
When the wheel stops rotating, tighten the nut locking the eccentric and the adjustment (Figure 46).
-
Verify the adjustment with the throttle lever in the SLOW and FAST position.
-
From each side of the bulkhead, tighten the locknuts evenly, securing the traction cable to the bulkhead (Figure 46). Do not twist the cable.
Note: If cable tension exists when the functional-control lever is in the NEUTRAL position, the machine may creep when you move the lever to the MOW or TRANSPORT position.
-
Adjusting the Transport Speed
Obtaining the Maximum Transport Speed
The traction pedal comes adjusted for maximum-transport speed, but you may need to adjust it if the pedal reaches full stroke before it contacts the pedal stop, or if you want to a decrease the transport speed.
To obtain the maximum-transport speed, put the functional control lever in the TRANSPORT position and press down on the traction pedal. If the pedal contacts the stop (Figure 47) before you feel tension on the cable, perform the following adjustment procedure:
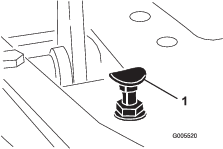
-
Put the functional-control lever in the TRANSPORT position and loosen the locknut securing the pedal stop to the floor plate (Figure 47).
-
Tighten the pedal stop until it does not contact the traction pedal.
-
Continue applying a light load on the transport pedal and adjust the pedal stop so it contacts the pedal rod and tighten the nuts.
Important: Ensure that the tension on the cable is not excessive or you will reduce the cable life.
Reducing the Transport Speed
-
Press down on the traction pedal and loosen the locknut securing the pedal stop to the floor plate.
-
Loosen the pedal stop until you obtain the desired transport speed.
-
Tighten the locknut securing the pedal stop.
Adjusting the Mowing Speed
Factory setting: 6.1 km/h (3.8 mph)
-
Loosen the jam nut on the trunnion bolt on the side of the traction pedal (Figure 48).
-
Rotate the trunnion bolt counterclockwise to increase the mowing speed and clockwise to decrease it.
-
Tighten the jam nut without turning the trunnion bolt and check the ground speed. Repeat this procedure, if required.
Brake Maintenance
Burnishing the Brakes
Firmly apply the brakes and drive the machine at mowing speed until the brakes are hot, as indicated by their smell. You may need to adjust the brakes after the break-in period; refer to Adjusting the Brakes.
Adjusting the Brakes
A brake adjustment rod is located at each side of the machine so that you can adjust the brakes equally.
-
While moving forward in transport speed, press the brake pedal; both wheels should apply equally.
Caution
Testing the brakes in a confined area where others are present could cause injury.
Always check the brakes in a wide, open-spaced, flat area free from people and obstructions before and after the adjustment.
-
If the brakes do not apply equally, adjust the brakes as follows:
-
Disconnect the brake rods by removing the cotter pin and clevis pin (Figure 49).
-
Loosen the jam nut and adjust the clevis accordingly (Figure 49).
-
Assemble the clevis to the brake shaft (Figure 49).
-
When you press the brake pedal, the pedal should move 13 to 26 mm (1/2 to 1 inch) travel before the brake shoes contacts the brake drums. Adjust the clevis on the brake shaft, if necessary, to achieve this setting.
-
While moving forward in transport speed, press the brake pedal; both brakes should apply equally. Adjust them, if necessary.
-
Important: Burnish the brakes annually; refer to the Burnishing the Brakes section.
Controls System Maintenance
Adjusting the Cutting Unit Lift/Drop
The cutting unit lift/drop circuit comes with a flow-control valve (Figure 50). This valve is preset at the factory at approximately 3 turns open, but you may need to adjust it to compensate for differences in hydraulic fluid temperatures, mowing speeds, etc.
Note: Allow the hydraulic fluid to reach full operating temperature before adjusting the flow-control valve.
-
Locate the flow-control valve below the seat (Figure 50).
-
Loosen the jam nut at the adjusting knob on the flow control valve.
-
Adjust the flow control valve as follows:
-
Rotate the knob counterclockwise if the center cutting unit is dropping too late or
-
Rotate the knob clockwise if the center cutting unit is dropping too early.
Note: You should not need to rotate it more than 1/32 to 1/16 of a turn.
-
-
Test the adjustment and repeat step 3 as needed; when finished, tighten the jam nut.
Adjusting the Lift Cylinders
To regulate the height of the front-cutting units when in the raised (transport) position, you can adjust the front-lift cylinders.
-
Lower the cutting units to the ground.
-
Remove the bolts that secure the cover plate of the lift cylinder that you are adjusting from the support brackets of the chassis (Figure 51).
-
Loosen the jam nut securing the clevis fitting to the cylinder of the cutting-unit that needs to be adjusted (Figure 52).
-
Remove the retaining pin and clevis pin (Figure 52)
-
Rotate the clevis until you attain the desired height (Figure 53).
-
Assemble the clevis fitting to the lift arm with the clevis pin and retaining pin, and tighten the jam nut (Figure 52 and .Figure 53).
-
Install the cover plate and bolts that you removed in step 2.
Hydraulic System Maintenance
Hydraulic System Safety
-
Seek immediate medical attention if fluid is injected into skin. Injected fluid must be surgically removed within a few hours by a doctor.
-
Ensure that all hydraulic-fluid hoses and lines are in good condition and all hydraulic connections and fittings are tight before applying pressure to the hydraulic system.
-
Keep your body and hands away from pinhole leaks or nozzles that eject high-pressure hydraulic fluid.
-
Use cardboard or paper to find hydraulic leaks.
-
Safely relieve all pressure in the hydraulic system before performing any work on the hydraulic system.
Servicing the Hydraulic Fluid
Important: Regardless of the hydraulic fluid type used, any traction unit used for off-green applications, verticutting or used during ambient temperatures above 29°C (85°F) should have the Oil Cooler Kit (Part No. 105-8339) installed.
Hydraulic Fluid Specifications
The hydraulic-fluid reservoir is filled at the factory with approximately 32.2 L (8.5 US gallons) of high quality hydraulic fluid. Check the level of the hydraulic fluid before operating the machine each day. If the fluid is low, add an appropriate fluid as described in the following sections:
Toro Premium All Season Hydraulic Fluid (Available in 5-gallon pails or 55-gallon drums. See the Parts Catalog or your authorized Toro distributor for part numbers.) |
Alternate fluids: If the Toro fluid is not available, other fluids may be used provided they meet all the following material properties and industry specifications. Do not use synthetic fluid. Consult with your lubricant distributor to identify a satisfactory product
Note: Toro will not assume responsibility for damage caused by improper substitutions, so use only products from reputable manufacturers who will stand behind their recommendation.
High Viscosity Index/Low Pour Point Anti-wear Hydraulic Fluid, ISO VG 46 | |
Material Properties: | |
Viscosity, ASTM D445 | cSt @ 40° C 44 to 50cSt @ 100° C 7.9 to 8.5 |
Viscosity Index ASTM D2270 | 140 to 160 |
Pour Point, ASTM D97 | -34° F to -49° F |
Industry Specifications: | |
Vickers I-286-S (Quality Level), Vickers M-2950-S (Quality Level), Denison HF-0 |
Important: The ISO VG 46 Multigrade fluid has been found to offer optimal performance in a wide range of temperature conditions. For operation in consistently high ambient temperatures, 18°C (65°F) to 49°C (120°F), ISO VG 68 hydraulic fluid may offer improved performance.
Premium Biodegradable Hydraulic Fluid-Mobil EAL EnviroSyn 46H
Important: Mobil EAL EnviroSyn 46H is the only synthetic biodegradable fluid approved by Toro. This fluid is compatible with the elastomers used in Toro hydraulic systems and is suitable for a wide-range of temperature conditions. This fluid is compatible with conventional mineral oils, but for maximum biodegradability and performance the hydraulic system should be thoroughly flushed of conventional fluid. The oil is available in 19 L (5 US gallon) containers or 208 L (55 US gallon) drums from your Mobil distributor.
Note: Many hydraulic fluids are almost colorless, making it difficult to spot leaks. A red dye additive for the hydraulic system oil is available in 20 ml (0.67 oz) bottles. One bottle is sufficient for 15 to 22 L (4 to 6 US gallons) of hydraulic fluid. Order Part No. 44-2500 from your authorized Toro distributor. Do not use this red dye with biodegradable fluids. Use food coloring.
Checking the Hydraulic-Fluid Level
-
Position the machine on a level surface.
Note: Ensure that the machine has cooled down so the fluid is cold.
-
Check the fluid level according to the tank on your machine:
-
If the auxiliary hydraulic tank has a sight window, check the oil level there (Figure 54), and proceed to step 5.
Note: If the fluid level is between the 2 marks on the sight window, the fluid level is sufficient.
-
If the auxiliary hydraulic tank does not have a sight window, locate the dipstick on the top of the machine (Figure 54) and proceed to step 3.
-
-
Remove the dipstick and wipe it with a clean rag, then screw the dipstick back into the tank.
-
Remove the dipstick and check the fluid level. If it is between the marks on the dipstick, the level is sufficient. If the fluid level is not between the marks, adjust the fluid level accordingly (Figure 55).
-
Remove the cap from the hydraulic fluid tank and slowly fill the tank with the appropriate high quality hydraulic fluid until the level is between the 2 marks on the sight window or dipstick.
Important: To prevent system contamination, clean the top of the hydraulic-fluid containers before puncturing them. Ensure that the pour spout and funnel are clean.
Note: Do not mix hydraulic fluids.
-
Install the cap.
Note: Make a close visual inspection of the hydraulic components. Inspect them for leaks, loose fasteners, missing parts, or improperly routed lines. Make any necessary corrections.
Changing the Hydraulic Fluid and Filter
Hydraulic Fluid Capacity: 25.7 L (6.8 US gallons)
If the fluid becomes contaminated, have your authorized Toro distributor flush the system. Contaminated fluid looks milky or black when compared to clean fluid.
-
Clean the area around the filter mounting area (Figure 56). Place a drain pan under the filter and remove the filter.
Note: If you will not be draining the fluid, disconnect and plug the hydraulic line going to the filter.
-
Fill the replacement filter with the appropriate hydraulic fluid, lubricate the sealing gasket, and hand turn it until the gasket contacts the filter head. Then tighten it 3/4 turn further.
-
Fill the hydraulic reservoir with hydraulic fluid; refer to Hydraulic Fluid Specifications and Checking the Hydraulic-Fluid Level.
-
Start the machine and run it at idle for 3 to 5 minutes to circulate the fluid and remove any air trapped in the system. Shut off the engine and check the fluid level.
-
Dispose of the fluid and filter properly.
Checking the Hydraulic Lines and Hoses
Check the hydraulic lines and hoses daily for leaks, kinked lines, loose mounting supports, wear, loose fittings, weather deterioration, and chemical deterioration. Make all necessary repairs before operating.
Checking the Leak Detector
The leak detector system is designed to assist in early detection of hydraulic-fluid-system leaks. If the fluid level in the main hydraulic reservoir is lowered by 118 to 177 ml (4 to 6 oz), the float switch in the tank will close. After a 1 second delay, the alarm sounds, alerting the operator (Figure 59). Expansion of fluid, due to normal heating during machine operation, causes the fluid to transfer into the auxiliary fluid reservoir. The fluid returns to the main tank when you turn off the ignition switch.
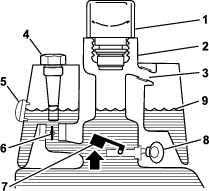
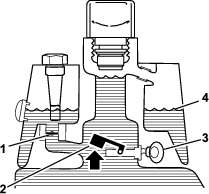
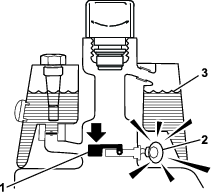
Checking the System Operation
-
With ignition switch in the ON position, move the leak detector switch rearward and hold. After the 1-second delay elapses, the alarm should sound.
-
Release the leak-detector switch.
Checking the Leak-Detector-System Operation
-
Move the ignition switch to the ON position. Do not start the engine.
-
Remove the hydraulic-tank breather from the neck of the tank.
-
Insert a clean rod or screwdriver into the tank neck and gently push down on the switch float (Figure 60); the alarm should sound after the 1-second delay.
-
Release the float; the alarm should stop sounding.
-
Install the hydraulic-tank cap.
-
Move the ignition switch to the OFF position.
Operating the Leak Detector
The leak detector alarm may sound for 1 of the following reasons:
-
A leak of 118 to 177 ml (4 to 6 oz) has occurred.
-
The fluid level in the main reservoir is reduced by 118 to 177 ml (4 to 6 oz) due to contraction of the fluid by cooling.
If the alarm sounds, turn off the machine as quickly as possible and inspect it for leaks. If the alarm sounds while operating on a green, drive off the green first. Determine the source of the leak and repair it before continuing operation.
If you do not find a leak and suspect a false alarm, move the ignition switch to the OFF position and allow the machine to stand for 1 to 2 minutes to allow the fluid levels to stabilize. Then start the machine and operate it in a non-sensitive area to confirm that no leak exists.
False alarms, due to fluid contraction, may be caused by extended idling of the machine after normal operation. A false alarm may also occur if you work the machine at a reduced workload after an extended period of a heavier workload. To avoid false alarms, turn the machine off rather than idling for extended periods.
Blade Safety
Refer to and complete the procedure in Maintenance Safety.
A worn or damaged blade or bedknife can break, and a piece could be thrown toward you or bystanders, resulting in serious personal injury or death.
-
Inspect the blades and bedknives periodically for excessive wear or damage.
-
Use care when checking the blades. Wear gloves and use caution when servicing them. Only replace or backlap the blades and bedknives; never straighten or weld them.
-
On machines with multiple cutting units, take care when rotating a reel; it can cause the reels in the other cutting units to rotate.
Checking the Reel-to-Bedknife Contact
Each day before operating the machine, check the reel-to-bedknife contact, regardless if the quality of cut had previously been acceptable. There must be light contact across the full length of the reel and bedknife; refer to the Cutting Unit Operator’s Manual.
Setting the Reel Speed
To achieve a consistent, high-quality cut and a uniform after-cut appearance, you must correctly set the reel speed control (located on the manifold block under the cover to the left of the seat). Adjust the reel speed control as follows:
-
Decide the height of cut at which the cutting units are set.
-
Decide the desired ground speed best suited for conditions.
-
Use table that follows to determine the reel-speed setting for your 5-, 8-, 11-, or 14-blade cutting units (Figure 61).
-
Tilt the operator’s seat forward and support it with the prop rod (Figure 62).
-
To adjust the reel speed by rotating the knob of the reel-speed control (Figure 63) until the indicator arrow are in line with the number that you determined in step 3.
Note: You can increase or decrease the reel speed to compensate for turf conditions.
Backlapping the Reels
Warning
Contact with the reels or other moving parts can result in personal injury.
-
Keep your hands and clothing away from the reels or other moving parts.
-
Never attempt to turn the reels by hand or foot while the engine is running.
-
Position the machine on a level surface, lower the cutting units, shut off the engine, remove the key, and set the parking brake.
-
Tilt the operator’s seat forward and support it with the prop rod (Figure 64).
-
Make initial reel to bedknife adjustments appropriate for honing all the cutting units that you are backlapping; refer to the Cutting Unit Operator's Manual.
-
Rotate the backlap lever to the R position (Figure 65).
-
Rotate the reel-speed knob to setting 1 (Figure 65).
-
Start the engine and run at low idle speed.
Important: Do not change the engine speed while backlapping or the reels may stall. Only backlap at idle engine speed.
-
With the mow/transport lever in the NEUTRAL position, move the raise/lower mow control forward to start the backlapping operation on the reel.
-
Apply lapping compound with a long handle brush. Never use a short-handled brush.
-
If the reels stall or become erratic while backlapping, select a higher reel speed setting until the speed stabilizes, then return the reel speed to setting 1 or to your desired speed.
-
To make an adjustment to the cutting units while backlapping, turn the reels off by moving the raise/lower mow control rearward and shut off the engine. After completing adjustments, repeat steps 4 through 8.
-
-
Repeat the steps 4 through 8 for all cutting units that you want to backlap.
-
When finished, return the backlap lever to the F position, move the reel speed knob to the desired reel-speed setting, lower the seat, and wash all lapping compound off of the cutting units. Adjust cutting unit reel to bedknife as needed.
Important: If you do not return the backlap lever to the F position after backlapping, the cutting units will not raise or function properly.