Maintenance
Determine the left and right sides of the machine from the normal operating position.
Recommended Maintenance Schedule(s)
Maintenance Service Interval | Maintenance Procedure |
---|---|
After the first 8 operating hours |
|
After the first 100 operating hours |
|
After the first 250 operating hours |
|
Before each use or daily |
|
Every 50 hours |
|
Every 100 hours |
|
Every 200 hours |
|
Every 250 hours |
|
Every 500 hours |
|
Monthly |
|
Yearly |
|
Yearly or before storage |
|
Important: Refer to your engine operator's manual for additional maintenance procedures.
Caution
If you leave the key in the ignition switch, someone could accidently start the engine and seriously injure you or other bystanders.
Remove the key from the ignition before you perform any maintenance.
Pre-Maintenance Procedures
Maintenance and Storage Safety
-
Before repairing the machine do the following:
-
Disengage the drives.
-
Engage the parking brake.
-
Shut off the engine and remove the key.
-
Disconnect the spark-plug wire.
-
-
Park the machine on a level surface.
-
Clean grass and debris from the cutting unit, drives, mufflers, and engine to help prevent fires.
-
Clean up oil or fuel spills.
-
Let the engine cool before storing the machine.
-
Do not store the machine or fuel near flames or drain the fuel indoors.
-
Do not allow untrained personnel to service the machine.
-
Use jack stands to support the machine and/or components when required.
-
Carefully release pressure from components with stored energy.
-
Disconnect the battery or remove the spark-plug wire before making any repairs. Disconnect the negative terminal first and the positive terminal last. Connect the positive terminal first and negative last.
-
Use care when checking the blades. Wrap the blade(s) or wear thickly padded gloves, and use caution when servicing them. Only replace blades; do not straighten or weld them.
-
Keep your hands and feet away from moving parts. If possible, do not make adjustments with the engine running.
-
Keep all parts in good working condition and all hardware tightened, especially the blade-attachment bolts. Replace all worn or damaged decals.
-
Never interfere with the intended function of a safety device or reduce the protection provided by a safety device. Check their proper operation regularly.
-
To ensure optimum performance and continued safety certification of the machine, use only genuine Toro replacement parts and accessories. Replacement parts and accessories made by other manufacturers could be dangerous, and such use could void the product warranty.
-
Check the parking brake operation frequently. Adjust and service as required.
Releasing the Mower-Deck Curtain
Loosen the bottom bolt of the curtain to release the mower-deck curtain and get access to the top of the mower deck (Figure 45). After performing maintenance, install the curtain and tighten the bolt.
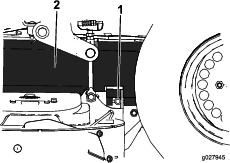
Removing the Sheet-Metal Guard
Loosen the 2 front bolts and remove the sheet-metal guard to access the mower belts and spindles (Figure 46). After performing maintenance, install the sheet-metal guard and tighten the bolts.
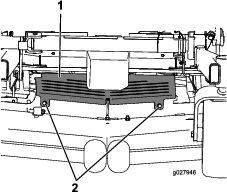
Lubrication
Grease more frequently when operating conditions are extremely dusty or sandy.
Grease Type: No. 2 general-purpose lithium-based or molybdenum-based grease
-
Disengage the blade-control switch (PTO), move the motion-control levers to the NEUTRAL-LOCK position, and engage the parking brake.
-
Shut off the engine, remove the key, and wait for all moving parts to stop before leaving the operating position.
-
Clean the grease fittings with a rag.
Note: Make sure that you scrape any paint off the front of the fitting(s).
-
Connect a grease gun to the fitting.
-
Pump grease into the fittings until grease begins to ooze out of the bearings.
-
Wipe up any excess grease.
Adding Light Oil or Spray Lubrication
Lubricate the deck-lift pivots.
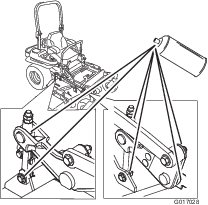
Greasing the Mower
-
Disengage the blade-control switch (PTO), move the motion-control levers to the NEUTRAL-LOCK position, and engage the parking brake.
-
Shut off the engine, remove the key, and wait for all moving parts to stop before leaving the operating position.
-
Loosen the bottom bolt holding the mower-deck curtain to the mower deck. Refer to Releasing the Mower-Deck Curtain.
-
Remove the sheet-metal guard. Refer to Removing the Sheet-Metal Guard.
-
Grease the mower deck idler-pulley pivot until grease comes out the bottom (Figure 48).
-
Grease the drive-belt idler arm (Figure 48).
-
Remove the dust cap and adjust the caster pivots.
Note: Keep the dust cap off until greasing is done.
-
Remove the hex plug.
-
Thread a grease fitting into the hole.
-
Pump grease into the fitting until it oozes out around the top bearing.
-
Remove the grease fitting in the hole.
-
Install the hex plug and dust cap (Figure 50).
-
Grease the caster-wheel bearings (Figure 50).
-
Install the sheet-metal guard. Refer to Removing the Sheet-Metal Guard.
-
Tighten the bolt for the mower-deck curtain. Refer to Releasing the Mower-Deck Curtain.
Lubricating the Caster-Wheel Hubs
-
Shut off the engine, wait for all moving parts to stop, remove the key, and engage the parking brake.
-
Raise the mower for access.
-
Remove the caster wheel from the caster forks.
-
Remove the seal guards from the wheel hub.
-
Remove a spacer nut from the axle assembly in the caster wheel.
Note: Thread-locking adhesive has been applied to lock the spacer nuts to the axle.
-
Remove the axle (with the other spacer nut still assembled to it) from the wheel assembly.
-
Pry out seals and inspect bearings for wear or damage and replace if necessary.
-
Pack the bearings with a general-purpose grease.
-
Insert 1 bearing and 1 new seal into the wheel.
Note: Replace the seals.
-
If the axle assembly is missing both spacer nuts, apply a thread-locking adhesive to 1 spacer nut and thread it onto the axle with the wrench flats facing outward.
Note: Do not thread the spacer nut all of the way onto the end of the axle. Leave approximately 3 mm (1/8 inch) from the outer surface of the spacer nut to the end of the axle inside the nut.
-
Insert the assembled nut and axle into the wheel on the side of the wheel with the new seal and bearing.
-
With the open end of the wheel facing up, fill the area inside the wheel around the axle full of general-purpose grease.
-
Insert the second bearing and new seal into the wheel.
-
Apply a thread-locking adhesive to the second spacer nut, and thread it onto the axle with the wrench flats facing outward.
-
Torque the nut to 8 to 9 N∙m (75 to 80 in-lb), loosen, then torque to 2 to 3 N∙m (20 to 25 in-lb).
Note: Make sure that the axle does not extend beyond either nut.
-
Install the seal guards over the wheel hub, and insert the wheel into the caster fork.
-
Install the caster bolt and tighten the nut fully.
Important: To prevent seal and bearing damage, check the bearing adjustment often. Spin the caster tire. The tire should not spin freely (more than 1 or 2 revolutions) or have any side play. If the wheel spins freely, adjust the torque on the spacer nut until there is a slight amount of drag. Apply another layer of thread-locking adhesive.
Engine Maintenance
Warning
Contact with hot surfaces may cause personal injury.
Keep your hands, feet, face, clothing, and other body parts away the muffler and other hot surfaces.
Engine Safety
Shut off the engine before checking the oil or adding oil to the crankcase.
Servicing the Air Cleaner
Note: Service the air cleaner more frequently if operating conditions are extremely dusty or sandy.
Removing the Filters
-
Disengage the blade-control switch (PTO), move the motion-control levers to the NEUTRAL-LOCK position, and engage the parking brake.
-
Shut off the engine, remove the key, and wait for all moving parts to stop before leaving the operating position.
-
Push down to release the retaining clamps on the air cleaner, and pull the air-cleaner cover off the air-cleaner body (Figure 52).
-
Clean the inside of the air-cleaner cover with compressed air.
-
Gently slide the primary filter out of the air-cleaner body (Figure 52). Avoid knocking the filter into the side of the body.
-
Remove the secondary filter only if you intend to replace it.
Important: Never attempt to clean the secondary filter. If the secondary filter is dirty, then the primary filter is damaged and you should replace both filters.
-
Inspect the primary filter for damage by looking into the filter while shining a bright light on the outside of the filter.
Note: Holes in the filter appear as bright spots.
Note: If the filter is damaged discard it.
Servicing the Primary Filter
-
Do not clean the paper filter, replace it (Figure 52).
-
Inspect the element for tears, an oily film, or damage to the rubber seal.
-
Replace the paper element if it is damaged.
Servicing the Secondary Filter
Do not clean the secondary filter, replace it.
Important: Do not attempt to clean the secondary filter. If the secondary filter is dirty, then the primary filter is damaged and you should replace both filters.
Installing the Filters
Important: To prevent engine damage, always operate the engine with both air filters and the cover installed.
-
If installing new filters, check each filter for shipping damage.
Note: Do not use a damaged filter.
-
If the secondary filter is being replaced, carefully slide it into the filter body (Figure 52).
-
Carefully slide the primary filter over the secondary filter (Figure 52).
-
Ensure that it is fully seated by pushing on the outer rim of the filter while installing it.
Important: Do not press on the soft inside area of the filter.
-
Install the air-cleaner cover with the breather cap down, and rotate so that the retaining clamps lock the cover in place (Figure 52).
Servicing the Engine Oil
Oil Type: Detergent oil (API service SG, SH, SJ, or higher)
Oil Capacity:
-
Model 74919TE: with a filter change, 2.1L (71 oz); with no filter change, 1.8L (61 oz)
-
Model 74925TE: with a filter change, 2.3 L (77 oz); with no filter change, 2.1L (70 oz)
Viscosity: See the table below.
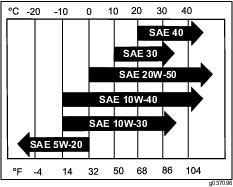
Note: Use of multi-grade oils (5W-20, 10W-30, or 10W-40) increase oil consumption. Check the oil level more frequently when using them.
Checking the Engine-Oil Level
Note: Check the oil when the engine is cold.
Warning
Contact with hot surfaces may cause personal injury.
Keep your hands, feet, face, clothing, and other body parts away from the muffler and other hot surfaces.
Important: Do not overfill the crankcase with oil because damage to the engine may result. Do not run engine with oil below the Low mark because the engine may be damaged.
-
Disengage the blade-control switch (PTO), move the motion-control levers to the NEUTRAL-LOCK position, and engage the parking brake.
-
Shut off the engine, remove the key, and wait for all moving parts to stop before leaving the operating position (Figure 54).
Changing the Engine Oil
Note: Dispose of the used oil at a recycling center.
-
Start the engine and let it run for 5 minutes.
Note: This warms the oil so it drains better.
-
Park the machine so that the rear is slightly lower than the front to ensure that the oil drains completely.
-
Disengage the blade-control switch (PTO), move the motion-control levers to the NEUTRAL-LOCK position, and engage the parking brake.
-
Shut off the engine, remove the key, and wait for all moving parts to stop before leaving the operating position (Figure 55).
-
Slowly pour approximately 80% of the specified oil into the filler tube and slowly add the additional oil to bring it to the Full mark (Figure 56).
-
Start the engine and drive to a flat area.
-
Check the oil level again.
Changing the Engine-Oil Filter
Note: Change the engine-oil filter more frequently when operating conditions are extremely dusty or sandy.
-
Drain the oil from the engine; refer to Changing the Engine Oil.
-
Change the engine-oil filter (Figure 57).
Note: Ensure that the oil-filter gasket touches the engine, and then an extra 3/4 turn is completed.
-
Fill the crankcase with the proper type of new oil; refer to Changing the Engine Oil.
Servicing the Spark Plug
Make sure that the air gap between the center and side electrodes is correct before installing the spark plug. Use a spark plug wrench for removing and installing the spark plug(s) and a gapping tool/feeler gauge to check and adjust the air gap. Install a new spark plug(s) if necessary.
Type : NGK® BPR4ES or equivalent
Air Gap: 0.76 mm (0.03 inch)
Removing the Spark Plug
-
Shut off the engine, remove the key, and wait for all moving parts to stop before leaving the operating position.
-
Disengage the blade-control switch (PTO), move the motion-control levers to the NEUTRAL-LOCK position, and engage the parking brake.
-
Remove the hydraulic-unit shroud and the 2 bolts attached to it (Figure 58).
Note: This gives you access to the front spark plug.
-
Remove the spark plug.
-
Install the hydraulic-unit shroud (Figure 58).
Checking the Spark Plug
Important: Do not clean the spark plug(s). Always replace the spark plug(s) when it has: a black coating, worn electrodes, an oily film, or cracks.
If you see light brown or gray on the insulator, the engine is operating properly. A black coating on the insulator usually means the air cleaner is dirty.
Set the gap to 0.76 mm (0.03 inch).
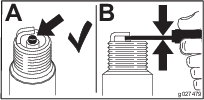
Installing the Spark Plug
Tighten the spark plug(s) to 24.4 to 29.8 N∙m (18 to 22 ft-lb).
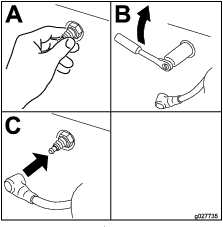
Checking the Spark Arrester
Warning
Hot exhaust system components may ignite fuel vapors even after you shut off the engine. Hot particles exhausted during engine operation may ignite flammable materials. Fire may result in personal injury or property damage.
Do not fuel or run the engine unless a spark arrester is installed.
-
Shut off the engine, wait for all moving parts to stop, remove the key, and engage the parking brake.
-
Wait for the muffler to cool.
-
If there are any breaks in the screen or welds are observed, replace the arrester.
-
If the screen is plugged, remove the arrester and shake loose particles out of the arrester, and clean the screen with a wire brush (soak in solvent if necessary).
-
Install the arrester on the exhaust outlet.
Fuel System Maintenance
Replacing the Fuel Filter
The fuel filter is located near the engine on the front or rear side of the engine.
-
Disengage the blade-control switch (PTO), move the motion-control levers to the NEUTRAL-LOCK position, and engage the parking brake.
-
Shut off the engine, remove the key, and wait for all moving parts to stop before leaving the operating position.
-
Allow the machine to cool down.
-
Close the fuel-shutoff valve under the seat (Figure 62).
-
Squeeze the ends of the hose clamps together and slide them away from the filter (Figure 62).
-
Remove the filter from the fuel lines.
-
Install a new filter and move the hose clamps close to the filter (Figure 62).
-
Open the fuel-shutoff valve.
Important: Install the fuel line hoses and secure with plastic ties the same as they were originally installed at the factory to keep the fuel line away from components that can cause fuel line damage.
Servicing the Fuel Tank
Do not attempt to drain the fuel tank. Ensure that an Authorized Service Dealer drains the fuel tank and services any components of the fuel system.
Electrical System Maintenance
Electrical System Safety
-
Disconnect the battery before repairing the machine. Disconnect the negative terminal first and the positive last. Connect the positive terminal first and the negative last.
-
Charge the battery in an open, well-ventilated area, away from sparks and flames. Unplug the charger before connecting or disconnecting the battery. Wear protective clothing and use insulated tools.
Warning
Battery posts, terminals, and related accessories contain lead and lead compounds, chemicals known to the State of California to cause cancer and reproductive harm. Wash hands after handling.
Servicing the Battery
Danger
Battery electrolyte contains sulfuric acid which is fatal if consumed and causes severe burns.
Do not drink electrolyte and avoid contact with skin, eyes or clothing. Wear safety glasses to shield your eyes and rubber gloves to protect your hands.
Removing the Battery
Warning
Battery terminals or metal tools could short against metal machine components causing sparks. Sparks can cause the battery gasses to explode, resulting in personal injury.
-
When removing or installing the battery, do not allow the battery terminals to touch any metal parts of the machine.
-
Do not allow metal tools to short between the battery terminals and metal parts of the machine.
Warning
Incorrect battery cable routing could damage the machine and cables causing sparks. Sparks can cause the battery gasses to explode, resulting in personal injury.
-
Always disconnect the negative (black) battery cable before disconnecting the positive (red) cable.
-
Always connect the positive (red) battery cable before connecting the negative (black) cable.
-
Disengage the blade-control switch (PTO), move the motion-control levers to the NEUTRAL-LOCK position, and engage the parking brake.
-
Shut off the engine, remove the key, and wait for all moving parts to stop before leaving the operating position.
-
Remove the battery as shown in Figure 63.
Installing the Battery
Note: Position the battery in the tray with the terminal posts opposite from the hydraulic tank (Figure 63).
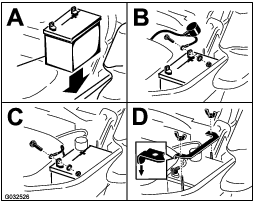
Charging the Battery
Warning
Charging the battery produces gasses that can explode.
Never smoke near the battery and keep sparks and flames away from battery.
Important: Always keep the battery fully charged (1.265 specific gravity). This is especially important to prevent battery damage when the temperature is below 0°C (32°F).
-
Charge battery for 10 to 15 minutes at 25 to 30 A or 30 minutes at 10 A.
-
When the battery is fully charged, unplug the charger from the electrical outlet, then disconnect the charger leads from the battery posts (Figure 65).
-
Install the battery in the machine and connect the battery cables; refer to Installing the Battery.
Note: Do not run the machine with the battery disconnected, electrical damage may occur.
Servicing the Fuses
The electrical system is protected by fuses. It requires no maintenance, however, if a fuse blows check the component/circuit for a malfunction or short.
Drive System Maintenance
Checking the Seat Belt
Visually inspect seat belt for wear, cuts, and proper operation of retractor and buckle. Replace before operating if damaged.
Checking the Rollover Protection System (ROPS) Knobs
Warning
To avoid injury or death from rollover: keep the roll bar in the fully raised locked position and use the seat belt.
Ensure that the seat is secured to the machine.
Check that both the mounting hardware and the knobs are in good working condition. Make sure that the knobs are fully engaged with the roll bar in the raised position. The upper hoop of the roll bar may need to be pushed forward or pulled rearward to get both knobs fully engaged (Figure 67).
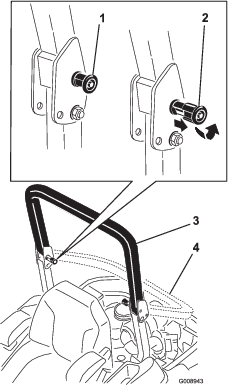
Adjusting the Tracking
-
Disengage the blade-control switch (PTO).
-
Drive to an open, flat area, and move the motion-control levers to the NEUTRAL-LOCK position.
-
Move the throttle midway between FAST and SLOW.
-
Move both motion-control levers forward until they both hit the stops in the T-slot.
-
Check which way the machine tracks.
-
If it tracks to the right, loosen the bolts and adjust the left stop plate rearward on the left T-slot until the machine tracks straight (Figure 68).
-
If it tracks to the left, loosen the bolts and adjust the right stop plate rearward on the right T-slot until the machine tracks straight (Figure 68).
-
Tighten the stop plate (Figure 68).
Checking the Tire Pressure
Maintain the air pressure in the rear tires at 90 kPa (13 psi). Uneven tire pressure can cause uneven cut. Check the tires when they are cold to get the most accurate pressure reading.
Note: The front tires are semi-pneumatic tires and do not require air pressure maintenance.
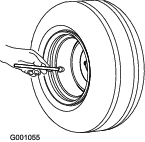
Checking the Wheel-Lug Nuts
Check and torque the wheel lug nuts to 122 to 129 N∙m (90 to 95 ft-lb).
Checking the Wheel-Hub Slotted Nut
Check and ensure that the torque of the slotted nut is 286 to 352 N∙m (211 to 260 ft-lb).
Note: Do not use anti-seize compound on wheel hub.
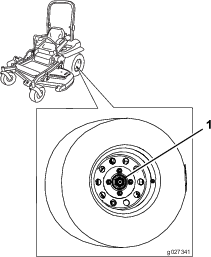
Adjusting the Caster-Pivot Bearing
-
Disengage the blade-control switch (PTO), move the motion-control levers to the NEUTRAL-LOCK position, and engage the parking brake.
-
Shut off the engine, remove the key, and wait for all moving parts to stop before leaving the operating position.
-
Remove the dust cap from caster and tighten the locknut (Figure 71).
-
Tighten the locknut until the spring washers are flat, and then back off a 1/4turn to properly set the preload on the bearings (Figure 71).
Important: Make sure that the spring washers are installed correctly as shown in Figure 71.
-
Install the dust cap (Figure 71).
Using the Clutch Shim
Some later model year units have been built with clutches that contain a brake shim. When the clutch brake has worn to the point where the clutch no longer engages consistently, the shim can be removed to extend the clutch life.
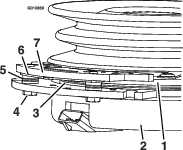
Removing the Clutch Shim
-
Shut off the engine, wait for all moving parts to stop, remove the key, engage the parking brake, and allow the machine to cool completely before starting these instructions.
-
Using an air compressor, blow out any debris from under the brake pole and around the brake spacers (Figure 73).
-
Check the condition of the wire-harness leads, connectors, and terminals.
Note: Clean or repair as necessary.
-
Verify that 12V is present at the clutch connector when the blade-control switch (PTO) switch is engaged.
-
Measure the gap between the rotor and armature. If the gap is greater than 1 mm (0.04 inch), proceed with the following steps:
-
Loosen both brake-mounting bolts 1/2 to 1 full turn as shown in Figure 74.
Note: Do not remove the brake pole from the field shell/armature. The brake pole has worn to match the armature and needs to continue to match after the shim is removed to ensure proper brake torque.
-
Using needle-nose pliers, or by hand, hold the tab and remove the shim (Figure 75).
Note: Do not discard the shim until proper clutch function has been confirmed.
-
Using a pneumatic line, blow out any debris from under the brake pole and around the brake spacers.
-
Torque each bolt (M6 x 1) to 13 N∙m (10 ft-lb) +/-0.7 N∙m (0.5 ft-lb).
-
Using a 0.25 mm (0.01 inch) thick feeler gauge, verify that a gap is present between the rotor and the armature face on both sides of the brake pole as shown in Figure 76 and Figure 77.
Note: Due to the way the rotor and the armature faces wear (peaks and valleys) it is sometimes difficult to measure the gap accurately.
-
If the gap is less than 0.25 mm (0.01 inch), then install the shim; refer to .
-
If the gap is sufficient, proceed to the safety check in step 6.
-
-
Perform the following safety check:
-
Sit on the seat and start the engine.
-
Make sure that the blades do not engage with the blade-control switch (PTO) in the OFF position, and that the clutch is disengaged.
If the clutch does not disengage, install the shim again; refer to .
-
Engage and disengage the blade-control switch (PTO) 10 consecutive times to ensure that the clutch is functioning properly.
-
-
Cooling System Maintenance
Cleaning the Engine Screen and Engine-Oil Cooler
Remove any buildup of grass, dirt, or other debris from the oil cooler (Figure 78).
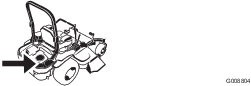
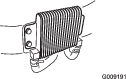
Before each use, remove any buildup of grass, dirt, or other debris from the engine screen. This helps ensure adequate cooling, correct the engine speed, and reduces the possibility of overheating and mechanical damage to the engine (Figure 79).
Cleaning the Engine-Cooling Fins and Shrouds
-
Disengage the blade-control switch (PTO) and engage the parking brake.
-
Shut off the engine, remove the key, and wait for all moving parts to stop before leaving the operating position.
-
Remove the air-intake screen, the recoil starter, and the fan housing (Figure 79).
-
Clean the debris and grass from the engine parts.
-
Install the air-intake screen, the recoil starter, and the fan housing (Figure 79).
Checking and Cleaning the Hydraulic Unit Shrouds
Important: The fasteners on the covers of this machine are designed to remain on the cover after removal. Loosen all of the fasteners on each cover a few turns so that the cover is loose but still attached, then go back and loosen them until the cover comes free. This prevents you from accidentally stripping the bolts free of the retainers.
-
Disengage the blade-control switch (PTO) and engage the parking brake.
-
Shut off the engine, remove the key, and wait for all moving parts to stop before leaving the operating position.
-
Move the seat forward.
-
Wait for the engine and hydraulic system to cool.
-
Clean the debris and grass from the hydraulic unit shrouds (Figure 80).
-
Over each dipstick, remove the cover and the bolt attached to the cover . Clean around each dipstick and hydraulic unit (Figure 81).
-
Position the seat.
Brake Maintenance
Adjusting the Parking Brake
Note: This procedure must be followed after the first 100 hours or when a brake component has been removed or replaced.
-
Drive the machine onto a level surface.
-
Disengage the blade-control switch (PTO), move the motion control levers to the NEUTRAL-LOCK position, and engage the parking brake.
-
Shut off the engine, wait for all moving parts to stop, and remove the key.
-
Raise the back of the machine and support the machine with jack stands.
Danger
Mechanical or hydraulic jacks may fail to support machine and cause a serious injury.
-
Use jack stands when supporting machine.
-
Do not use hydraulic jacks.
-
-
Remove the rear tires from the machine.
-
Remove any debris from the brake area.
-
Rotate the drive-wheel release handle to the released position; refer to Using the Drive-Wheel-Release Valves.
-
Check to see if there is a visible gap between the L-bracket and the linkage stop (Figure 82).
-
Disengage the parking brake, the lever should be in the down position.
-
Turn the wheel hub by hand in both directions relative to the caliper; the wheel hub should move freely between the caliper.
-
If a gap is needed or the wheel hub does not move freely:
-
Disengage the parking brake.
-
Disconnect and fine-tune the rear linkage assembly:
-
Shorten the link to create a gap.
-
Lengthen the link to allow wheel hub movement.
-
-
Connect the rear linkage assembly.
-
-
Engage the parking brake and check the gap.
-
Repeat steps 9 through 13 until a visible gap is achieved and the wheel hub rotates freely.
-
Repeat this procedure for the brake on the opposite side.
-
Rotate the drive-wheel release handle to the operating position; refer to Using the Drive-Wheel-Release Valves.
-
Install the rear tires and torque the lug nuts; refer to Checking the Wheel-Lug Nuts.
-
Remove the jack stands.
Belt Maintenance
Inspecting the Belts
Replace the belt if it is worn. The signs of a worn belt include squealing while the belt is rotating; the blades slipping while cutting grass; and frayed edges, burn marks, and cracks on the belt.
Replacing the Mower Belt
-
Disengage the blade-control switch (PTO), move the motion-control levers to the NEUTRAL-LOCK position, and engage the parking brake.
-
Shut off the engine, remove the key, and wait for all moving parts to stop before leaving the operating position.
-
Lower the mower to the 76 mm (3 inch) height-of-cut.
-
Loosen the bottom bolt holding the mower-deck curtain to the mower deck. Refer to Releasing the Mower-Deck Curtain.
-
Remove the sheet-metal guard. Refer to Removing the Sheet-Metal Guard
-
Remove the belt covers (Figure 83).
-
Use a ratchet in the square hole in the idler arm to remove tension on the idler spring (Figure 84).
-
Remove the belt from the mower-deck pulleys.
-
Remove the belt guide on the spring-loaded idler arm (Figure 84).
-
Remove the existing belt.
-
Install the new belt around the mower pulleys and the clutch pulley under the engine (Figure 84).
-
Install the belt guide on the idler arm (Figure 84).
-
Using the ratchet in the square hole, install the idler spring (Figure 84).
Note: Make sure that the spring ends are seated in the anchor grooves.
-
Install the belt covers (Figure 85).
-
Install the sheet-metal guard. Refer to Removing the Sheet-Metal Guard.
-
Tighten the bolt for the mower-deck curtain. Refer to Releasing the Mower-Deck Curtain.
Replacing the Hydraulic Pump-Drive Belt
-
Disengage the blade-control switch (PTO) and engage the parking brake.
-
Shut off the engine, remove the key, and wait for all moving parts to stop before leaving the operating position.
-
Remove the mower belt; refer to Replacing the Mower Belt.
-
Raise the machine and support it with jack stands (Figure 86).
-
Use a ratchet in the square hole in the idler arm to remove the idler spring (Figure 86).
-
Unhook the idler spring from the frame (Figure 86).
-
Remove the belt from the hydraulic-unit-drive pulleys and the engine pulley.
-
Install the new belt around engine pulley and the 2 drive pulleys.
-
Using a ratchet in the square hole in the idler arm, install the idler spring to the frame (Figure 86).
-
Install the mower belt; refer to Replacing the Mower Belt.
Controls System Maintenance
Adjusting the Control-Handle Position
There are 2 height positions for the control levers—high and low. Remove the bolts to adjust the height for the operator.
-
Disengage the blade-control switch (PTO), move the motion-control levers to the NEUTRAL-LOCK position, and engage the parking brake.
-
Shut off the engine, remove the key, and wait for all moving parts to stop before leaving the operating position.
-
Loosen the bolts and flange nuts installed in the levers (Figure 87).
-
Align the levers in the front-to-rear position by bringing the levers together to the NEUTRAL position, and slide them until they are aligned, then tighten the bolts (Figure 88).
-
If the ends of the levers hit against each other, refer to Adjusting the Control-Handle Position.
-
Repeat to adjust the control levers.
Adjusting the Motion-Control Linkage
Located on either side of the fuel tank, below the seat are the pump-control linkages. Rotating the pump linkage with a wrench (1/2 inch) allows fine tuning adjustments so that the machine does not move in neutral. Any adjustments should be made for neutral positioning only.
Warning
Engine must be running and drive wheels must be turning so motion control adjustment can be performed. Contact with moving parts or hot surfaces may cause personal injury.
Keep fingers, hands, and clothing clear of rotating components and hot surfaces.
-
Prior to starting the engine, push the deck-lift pedal, and remove the height-of-cut pin.
-
Lower deck to the ground.
-
Raise the rear of machine up and support it with jack stands (or equivalent support).
Note: Raise the machine just high enough to allow the drive wheels to turn freely.
-
Remove the electrical connection from the seat safety switch, located under the bottom cushion of the seat.
Note: The switch is a part of the seat assembly.
-
Temporarily install a jumper wire across the terminals in the connector of the main wire harness.
-
Start the engine and run it at full throttle and disengage the brake.
Note: The brake must be engaged and the motion-control levers must be out to start the engine. The operator does not have to be in the seat, because of the jumper wire being used.
-
Run the unit for at least 5 minutes with the drive levers at full forward speed to bring the hydraulic fluid up to the operating temperature.
Note: The motion-control levers needs to be in neutral while making any necessary adjustments.
-
Bring the motion-control levers into the NEUTRAL position.
-
Adjust the pump control rod lengths by rotating the double nuts on the rod in the appropriate direction until the wheels slightly creep in reverse (Figure 89).
-
Move the motion-control levers to the reverse position and while applying slight pressure to the lever, allow the reverse-indicator springs to bring the levers back to neutral.
Note: The wheels must stop turning or slightly creep in reverse.
-
Shut off the unit, remove the jumper wire from the wire harness, and plug the connector into the seat switch.
-
Remove the jack stands.
-
Raise the deck and install the height-of-cut pin.
-
Check that the machine does not creep in neutral with the park brakes disengaged.
Adjusting the Motion-Control Damper
The top damper mounting bolt can be adjusted to obtain a more desired motion-control lever resistance. See Figure 90 for mounting options.
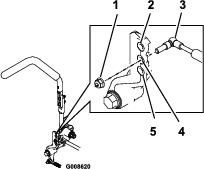
Adjusting the Motion Control Neutral-Lock Pivot
The flanged nut can be adjusted to obtain a more desired motion-control lever resistance when moving it to the NEUTRAL-LOCK position. See Figure 91 for adjustment options.
-
Loosen the jam nut.
-
Tighten or loosen the flanged nut to the desired feel.
Note: For more resistance, tighten the flanged nut.
Note: For less resistance, loosen the flanged nut
-
Tighten the jam nut.
Hydraulic System Maintenance
Hydraulic System Safety
-
Ensure that all hydraulic-fluid hoses and lines are in good condition and all hydraulic connections and fittings are tight before applying pressure to the hydraulic system.
-
Keep your body and hands away from pinhole leaks or nozzles that eject high-pressure hydraulic fluid.
-
Use cardboard or paper to find hydraulic leaks.
-
Safely relieve all pressure in the hydraulic system before performing any work on the hydraulic system.
-
Seek immediate medical attention if fluid is injected into skin. Injected fluid must be surgically removed within a few hours by a doctor.
Servicing the Hydraulic System
Hydraulic-Fluid Type: Toro® HYPR-OIL ™ 500 hydraulic fluid or Mobil® 1 15W-50.
Important: Use the specified fluid. Other fluids could damage the hydraulic system.
Each Hydraulic System Fluid Capacity: 1.5 L (52 oz) per side with filter change
Checking the Hydraulic Fluid
-
Position the machine on a level surface.
-
Disengage the blade-control switch (PTO), move the motion-control levers to the NEUTRAL-LOCK position, and engage the parking brake.
-
Shut off the engine, remove the key, and wait for all moving parts to stop before leaving the operating position.
-
Allow the engine and the hydraulic system to cool for 10 minutes.
Note: The oil level on the dipstick is incorrect when the oil is checked and the unit is hot.
-
Move the seat forward.
-
Clean the area around the dipsticks of hydraulic-system reservoirs (Figure 92).
-
Remove 1 dipstick from the hydraulic reservoir (Figure 92).
-
Wipe the dipstick off and thread the dipstick into the reservoir.
-
Remove the dipstick and look at the end (Figure 92).
Important: Do not overfill the hydraulic units with oil as damage may occur. Do not run the machine with the oil below the add mark.
-
If the oil level is at the add mark , slowly pour only enough oil into the hydraulic reservoir to raise the level to the full or H line.
-
Install the dipstick.
-
Repeat the procedure for the opposite dipstick.
Warning
Hydraulic fluid escaping under pressure can penetrate skin and cause injury.
-
If hydraulic fluid is injected into the skin it must be surgically removed within a few hours by a doctor familiar with this type of injury. Gangrene may result if this is not done.
-
Keep your body and hands away from pinhole leaks or nozzles that eject high-pressure hydraulic fluid.
-
Use cardboard or paper to find hydraulic leaks.
-
Safely relieve all pressure in the hydraulic system before performing any work on the hydraulic system.
-
Make sure that all hydraulic-oil hoses and lines are in good condition, and all hydraulic connections and fittings are tight before applying pressure to the hydraulic system.
-
Replacing the Hydraulic Fluid and Filters
To replace the hydraulic fluid, the filters need to be removed. Replace both at the same time; refer to Servicing the Hydraulic System for the oil specifications.
-
Disengage the blade-control switch (PTO), move the motion-control levers to the NEUTRAL-LOCK position, and engage the parking brake.
-
Shut off the engine, remove the key, and wait for all moving parts to stop before leaving the operating position.
-
Raise the machine and support it with jack stands (Figure 93).
-
Remove both the mower belt and the pump-drive belt; refer to Replacing the Mower Belt and Replacing the Hydraulic Pump-Drive Belt.
Note: This prevents oil from getting on the belts.
-
Place a drain pan under the filter, remove the old filter, and wipe the surface clean (Figure 94).
-
Apply a thin coat of hydraulic fluid to the rubber gasket on the replacement filter (Figure 94).
-
Install the replacement hydraulic filter.
-
Install the pump-drive belt and the mower belt.
-
Remove the jack stands and lower the machine (Figure 93).
-
Add oil to the hydraulic reservoir and check for any leaks.
-
Clean up any spilled oil.
-
Start the engine and let it run for about 2 minutes to purge air from the system.
-
Shut off the engine and check for leaks.
-
Check the oil level while the oil is cold.
-
If required, add oil to the hydraulic reservoir.
Note: Do not overfill.
Leveling the Mower Deck
Setting up the Machine
Note: Ensure that the mower deck is level before matching the height of cut (HOC).
-
Position the mower on a flat surface.
-
Disengage the blade-control switch (PTO), move the motion-control levers to the NEUTRAL-LOCK position, and engage the parking brake.
-
Shut off the engine, remove the key, and wait for all moving parts to stop before leaving the operating position.
-
Check tire pressure of the drive tires.
-
If needed, adjust to 90 kPa (13 psi).
-
Position the mower to the 76 mm (3 inches) height-of-cut position.
Leveling the Deck
-
Position the mower on a flat surface.
-
Stop engine, wait for all moving parts to stop, remove the key, and engage the parking brake.
-
Check the tire pressure in the drive tires.
Note: Proper inflation pressure for the tires is 90 kPa (13 psi).
-
Position the transport lock in the latching position.
-
Push the deck-lift pedal all the way forward and the deck latches at the 14 cm (5-1/2 inches) transport position (Figure 95).
-
Insert the height-adjustment pin into the 7.6 cm (3 inches) cutting-height location.
-
Release the transport lock and allow the deck to lower to the cutting height.
-
Raise the discharge chute.
-
On both sides of the deck, measure from the level surface to the front tip of the blade (Postion A) as shown in Figure 96.
Note: The measurement should read 7.6 mm (3 inches)
-
Fine-tune the adjustment nut on the front deck lift assembly by turning it (Figure 97).
Note: To increase the height, turn the adjustment nut clockwise; to decrease, turn counterclockwise.
Note: If the front deck links do not have enough adjustment to achieve accurate cut height, the single-point adjustment can be utilized to gain more adjustment.
-
To adjust the single-point system, loosen the 2 bolts at the bottom of the height-of-cut plate (Figure 98).
-
If the deck is too low, tighten the single-point-adjustment bolt by rotating it clockwise. If the deck is too high, loosen the single-point-adjustment bolt by rotating it counterclockwise (Figure 99).
Note: Loosen or tighten the single-point adjustment bolt enough to move the height-of-cut plate mounting bolts at least 1/3 the length of the available travel in their slots. This regains some up and down adjustment on each of the 4 deck links.
-
Tighten the 2 bolts at the bottom of the height-of-cut plate (Figure 98).
Note: In most conditions, the back blade tip should be adjusted 6.4 mm (1/4 inch) higher than the front.
-
Torque the 2 bolts to 37 to 45 N∙m (27 to 33 ft-lb).
-
On both sides of the deck, measure from the level surface to the back tip of the blade (postion B) as shown in Figure 96.
Note: The measurement should read 8.3 cm (3-1/4 inches)
-
Fine tune the screw adjuster by turning it to get 8.3 mm (3-1/4 inches) height (Figure 97).
To increase the height, turn the adjustment nut clockwise; to decrease, turn counterclockwise.
-
Measure until all 4 sides are the correct height.
-
Tighten all of the nuts on the deck-lift-arm assemblies.
-
Lower the discharge chute.
Servicing the Cutting Blades
To ensure a superior quality of cut, keep the blades sharp. For convenient sharpening and replacement, you may want to keep extra blades on hand.
Blade Safety
A worn or damaged blade can break, and a piece of the blade could be thrown toward you or bystanders, resulting in serious personal injury or death. Trying to repair a damaged blade may result in discontinued safety certification of the product.
-
Inspect the blades periodically for wear or damage.
-
Use care when checking the blades. Wrap the blades or wear gloves, and use caution when servicing the blades. Only replace or sharpen the blades; never straighten or weld them.
-
On multi-bladed machines, take care as rotating 1 blade can cause other blades to rotate.
Before Inspecting or Servicing the Blades
-
Park the machine on a level surface, disengage the blade-control switch (PTO), and engage the parking brake.
-
Shut off the engine, remove the key, and disconnect the spark-plug wires from the spark plugs.
Inspecting the Blades
-
Inspect the cutting edges (Figure 100).
-
If the edges are not sharp or have nicks, remove and sharpen the blade; refer to Sharpening the Blades.
-
Inspect the blades, especially in the curved area.
-
If you notice any cracks, wear, or a slot forming in this area, immediately install a new blade (Figure 100).
Checking for Bent Blades
-
Disengage the blade-control switch (PTO), move the motion-control levers to the NEUTRAL-LOCK position, and engage the parking brake.
-
Shut off the engine, remove the key, and wait for all moving parts to stop before leaving the operating position.
-
Rotate the blades until the ends face forward and backward.
-
Measure from a level surface to the cutting edge, position A, of the blades (Figure 101).
-
Rotate the opposite ends of the blades forward.
-
Measure from a level surface to the cutting edge of the blades at the same position as in step4 above.
Note: The difference between the dimensions obtained in steps 4 and 6 must not exceed 3 mm (1/8 inch).
Note: If this dimension exceeds 3 mm (1/8 inch), the blade is bent and must be replaced.
Warning
A blade that is bent or damaged could break apart and could seriously injure or kill you or bystanders.
-
Always replace a bent or damaged blade with a new blade.
-
Do not file or create sharp notches in the edges or surfaces of the blade.
-
Removing the Blades
Blades must be replaced if a solid object is hit, if the blade is out of balance, or if the blade is bent. To ensure optimum performance and continued safety conformance of the machine, use genuine Toro replacement blades. Replacement blades made by other manufacturers may result in nonconformance with safety standards.
-
Hold the blade end using a rag or a thickly-padded glove.
-
Remove the blade bolt, the curved washer, and the blade from the spindle shaft (Figure 102).
Sharpening the Blades
-
Use a file to sharpen the cutting edge at both ends of the blade (Figure 103).
Note: Maintain the original angle.
Note: The blade retains its balance if the same amount of material is removed from both cutting edges.
-
Check the balance of the blade by putting it on a blade balancer (Figure 104).
Note: If the blade stays in a horizontal position, the blade is balanced and can be used.
Note: If the blade is not balanced, file some metal off the end of the sail area only (Figure 103).
-
Repeat this procedure until the blade is balanced.
Installing the Blades
-
Install the blade onto the spindle shaft (Figure 105).
Important: The curved part of the blade must be pointing upward toward the inside of the mower to ensure proper cutting.
-
Install the spring disk and blade bolt (Figure 105).
Note: The spring-disk cone must be installed toward the bolt head (Figure 105).
-
Torque the blade bolt to 115 to 150 N∙m (85 to 110 ft-lb).
Removing the Mower Deck
Before servicing or removing the mower deck, lock out the spring-loaded deck arms.
Warning
Deck-lift-arm assemblies have stored energy. Removing the deck without releasing the stored energy can cause serious injury or death.
Do not attempt to disassemble the deck from the front frame without locking out the stored energy.
-
Shut off the engine, wait for all moving parts to stop, remove the key, and engage the parking brake.
-
Remove the height-adjustment pin and lower the deck to the ground.
-
Place the height-adjustment pin in the 7.6 cm (3 inch) cutting-height location.
Note: This locks the deck-lift arms in the lowest position when the deck is removed and the stored energy in the deck spring is released.
-
Remove the belt covers.
-
Lift up the floor pan and insert a ratchet into the square hole in the deck idler (Figure 106).
-
Rotate the deck idler clockwise and remove the mower belt (Figure 106).
-
Remove and retain the hardware on both sides of the deck (Figure 107).
-
Raise the deck struts and secure them in the up position.
-
Slide the deck out to the right side of the machine.
Replacing the Grass Deflector
Warning
An uncovered discharge opening could allow the lawn mower to throw objects at you or bystanders, resulting in serious injury. Also, contact with the blade could occur.
Do not operate the lawn mower unless you install a cover plate, a mulch plate, grass deflector or bagger.
-
Remove the locknut, the bolt, the spring, and the spacer holding the deflector to the pivot brackets (Figure 108).
-
Remove the damaged or worn grass deflector (Figure 108).
-
Place the spacer and the spring onto grass deflector.
-
Place the J-end of the spring behind the deck edge.
Note: Make sure that the J-end of the spring is installed behind the deck edge before installing the bolt as shown in Figure 108.
-
Install the bolt and the nut.
-
Place the J-hook end of the spring around the grass deflector (Figure 108).
Important: The grass deflector must be able to rotate. Lift the deflector up to the full open position and ensure that it rotates into the full down position.
Cleaning
Cleaning under the Mower
-
Disengage the blade-control switch (PTO), move the motion-control levers to the NEUTRAL-LOCK position, and engage the parking brake.
-
Shut off the engine, remove the key, and wait for all moving parts to stop before leaving the operating position.
-
Raise the mower to the transport position.
Disposing of Waste
Engine oil, batteries, hydraulic fluid, and engine coolant are pollutants to the environment. Dispose of these according to your state and local regulations.