Maintenance
Recommended Maintenance Schedule(s)
Maintenance Service Interval | Maintenance Procedure |
---|---|
After the first 8 hours |
|
Before each use or daily |
|
Every 50 hours |
|
Every 100 hours |
|
Every 250 hours |
|
Every 500 hours |
|
Before storage |
|
Yearly |
|
Maintenance Safety
-
Before adjusting, cleaning, servicing, or leaving the machine, do the following:
-
Position the machine on a level surface.
-
Move the throttle switch to the low-idle position.
-
Disengage the PTO.
-
Ensure that the traction is in neutral.
-
Engage the parking brake.
-
Shut off the engine of the tractor and remove the key.
-
Wait for all moving parts to stop.
-
Allow machine components to cool before performing maintenance.
-
-
Perform only those maintenance instructions described in this manual. If major repairs are ever needed or assistance is desired, contact an authorized Toro distributor.
-
Ensure that the machine is in safe operating condition by keeping nuts, bolts, and screws tight.
-
If possible, do not perform maintenance while the engine is running. Keep away from moving parts.
-
Do not check or adjust the chain tension when the tractor engine is running.
-
Carefully release pressure from components with stored energy.
-
Support the machine with blocks or storage stands when working beneath it. Never rely on the hydraulic system to support the machine.
-
Check the tine mounting bolts daily to be sure that they are tightened to specification.
-
Ensure that all guards are installed and the hood is secured shut after maintaining or adjusting the machine.
-
To ensure safe, optimal performance of the machine, use only genuine Toro replacement parts. Replacement parts made by other manufacturers could be dangerous, and such use could void the product warranty.
Jacking the Machine
Caution
If the machine is not properly supported by blocks or jack stands, the machine may move or fall, which may result in personal injury.
When changing attachments or performing other service, use correct blocks, hoists or jacks. Ensure that the machine is parked on a solid, level surface such as a concrete floor. Prior to raising the machine, remove any attachments that may interfere with the safe and proper raising of the machine. Always chock or block the tow vehicle wheels. Use jack stands or solid wood blocks to support the raised machine.
Note: If available, a hoist can be used to lift the rear of the ProCore Aerator. Use the eyelets in the coring head bearing housings as hoist attachment points (Figure 27)
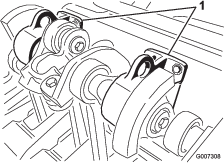
Greasing the Bearings and Bushings
Maintenance Service Interval | Maintenance Procedure |
---|---|
Every 50 hours |
|
The main working bearings of the aerator are sealed for life and require no maintenance or lubrication. This drastically reduces the maintenance required and eliminates the risk of grease or oil being dropped onto the turf.
There are grease fittings that must be lubricated with an SAE multi-purpose, high-temperature grease with high-pressure (EP) performance or SAE multi-purpose lithium-based grease.
The lubrication points are:
PTO shaft (3) (Figure 28)
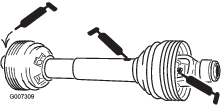
Roller bearings (ProCore 864: 2; ProCore 1298: 4) (Figure 29)
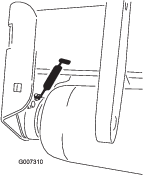
Drive shaft bearings (ProCore 864:1; ProCore 1298: 2) (Figure 30)
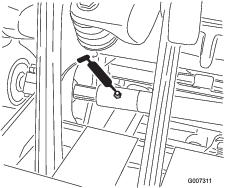
Important: Bearings rarely fail from defects in materials or workmanship. The most common reason for failure is moisture and contamination working its way past the protective seals. Bearings that are greased will rely upon regular maintenance to purge harmful debris from the bearing area. Sealed bearings rely on an initial fill of special grease and a robust integral seal to keep contaminants and moisture out of the rolling elements.
The sealed bearings require no lubrication or short term maintenance. This minimizes routine service required and reduces the potential of turf damage due to grease contamination. These sealed bearing packages will provide good performance and life under normal use, but periodic inspections of bearing condition and seal integrity should be conducted to avoid downtime. These bearings should be inspected seasonally and replaced if damaged or worn. Bearings should operate smoothly with no detrimental characteristics such as high heat, noise, looseness, or rust weeping.
Due to the operating conditions these bearing/seal packages are subject to (i.e. sand, turf chemicals, water, impacts, etc.) they are considered normal wear items. Bearings that fail due to other than defects in materials or workmanship are typically not covered under warranty.
Note: Bearing life can be negatively affected by improper washing procedures. Do not wash the unit when it is still hot and avoid directing high-pressure or high-volume spray at the bearings.It is common for new bearings to purge some grease out of the seals on a new machine. This purged grease will turn black in color due to collection of debris and not due to excessive heat. It is good practice to wipe this excess grease from the seals after the initial 8 hours. There may always appear to be a wet area around the seal lip. This is generally not detrimental to bearing life, but keeps the seal lip lubricated.Coring head bearing replacement is suggested at intervals of 500 hours. A bearing service kit which covers the complete coring head is available from your distributor.
Checking the Gearbox Lubrication
Maintenance Service Interval | Maintenance Procedure |
---|---|
Every 100 hours |
|
The gearbox is filled with 80W-90 gear oil or equivalent. Allow the gearbox to cool before checking the lubrication.
-
Clean debris from the fill plug and check the plug to avoid contamination.
-
Remove the check plug from the gearbox (Figure 31).
-
Make sure that the oil level is up to the bottom of the check plug hole in gearbox (Figure 31).
-
If the oil level is low, remove the fill plug from the gearbox and add oil as required.
-
Install the plugs.
Changing the Gearbox Lubrication
Maintenance Service Interval | Maintenance Procedure |
---|---|
After the first 8 hours |
|
Every 250 hours |
|
The gearbox is filled with 80W-90 gear oil or equivalent.
-
Clean debris from the fill plug and the drain cap to avoid contamination (Figure 31).
-
Remove the fill plug to relieve air draw.
-
Position a drain pan under the drain tube and remove the drain cap.
Note: The high viscosity of cool oil extends the drain time (approximately 30 minutes).
-
After oil is completely drained, install the drain cap.
-
Fill the gearbox with 1650 ml (56 fl oz) of high quality 80W-90 gear lube.
-
Install the fill plug.
-
Check the oil level.
Checking the Coring Head Fastener Torque
Maintenance Service Interval | Maintenance Procedure |
---|---|
After the first 8 hours |
|
Every 250 hours |
|
After the initial 8 hours of use, check the coring head fasteners to ensure that proper torque is maintained. Fastener torque requirements are listed on the reference service decal below and located on the coring head.
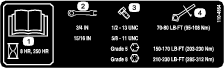
Inspecting the Belts
Maintenance Service Interval | Maintenance Procedure |
---|---|
Yearly |
|
The drive belt(s) on the ProCore Aerators have been designed to be very durable. However, the normal exposure to UV radiation, ozone or incidental exposure to chemicals can deteriorate the rubber compounding over time and lead to premature wear or material loss (i.e. chunking).
Annual belt inspection is highly recommended for signs of wear, excessive cushion cracks, or large embedded debris with replacement when needed.
Adjusting the Belt Tension
Maintenance Service Interval | Maintenance Procedure |
---|---|
Before each use or daily |
|
Make sure that the belt is properly tensioned to ensure correct operation of the machine and to prevent unnecessary wear.
-
Check for proper belt tension by compressing idler spring to a length of 146 mm (5-3/4 inches); refer to Figure 33.
-
Adjust the belt tension as follows:
-
Remove the rear coring head cover (Figure 34).
-
Remove the pulley shield mounting bolts and remove the shield (Figure 34).
-
Loosen the locknut securing the spring retainer (Figure 35).
-
Adjust the spring retainer to attain required compressed spring length (Figure 35).
-
Tighten the locknut against the spring retainer to lock the adjustment.
-
Install the pulley shield and the coring head cover.
-
Replacing the Drive Belt
Note: You do not need to remove the outside stomper arm to replace the drive belt.
Removing the Belt
-
Remove the rear coring head cover (Figure 36).
-
Remove the pulley shield mounting bolts and remove the shield (Figure 36).
-
Remove the fasteners securing the dirt shield and the lower belt shield (Figure 37). Remove the dirt shield and the lower belt shield.
-
To release the idler spring tension, loosen the locknut securing the spring retainer (Figure 38) and rotate the spring retainer.
Caution
Springs are under tension, use caution when adjusting or removing.
-
Loosen and remove the 2 locknuts and washers securing the rotalink damper for the #1 stomper arm (Figure 39).
-
Lower the rotalink damper from the coring head frame.
-
Route the drive belt down through the coring head frame and around the lower end of the #1 stomper arm (Figure 39).
Installing the Belt
-
Route the new drive belt around the lower end of the #1 stomper arm and up through the coring head frame.
-
Position the drive belt onto the crank pulley, under the idler assembly and over the drive pulley.
-
Raise the rotalink damper for the #1 stomper arm to coring head frame. Ensure that the damper spacers are installed in the same position as in removal.
-
Secure the rotalink damper to the coring head with the 2 washers and locknuts previously removed.
-
Install and adjust the belt idler pulley and adjust it to the appropriate tension.
-
Install the dirt shield and the lower belt shield. Adjust the lower shield to ensure clearance with the belt.
-
Install the pulley and the coring head covers.
Adjusting the Side Shield
The coring head side shields should be adjusted so that the bottom rides between 25 to 38 mm (1 to 1-1/2 inches) from the turf while aerating.
-
Loosen the bolts and nuts securing the side shield to frame (Figure 40).
-
Adjust the shield up or down and tighten the nuts.
Replacing the Turf Guards
All turf guards (Figure 41) should be replaced if broken or worn to less than 1/4 inch thickness. Broken turf guards can catch and tear turf, creating undesirable damage.
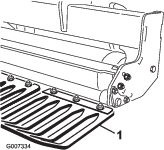
Coring Head Timing
The unitized coring head design of the ProCore aerators provides industry-leading smooth operation while taking out the guesswork of timing.
ProCore 864 (Figure 42)
Each pair of crank arms joined through a bearing housing are timed 180 degrees apart (i.e. arm positions 1-2, 3-4, 5-6, 7-8). The adjacent pairs are all set with the same timing whereas the later pair lags by 120 degrees. The same pair of coupling castings are used between all adjacent pairs (i.e. coupling positions 2-3, 4-5, 6-7). To further reduce operating vibration, 2 counter weights are added at the #1 position on the pulley and the #8 position.
Note: The numbers cast into the crank arms will not align with the raised indicator mark on the bearing housings for the ProCore 864.
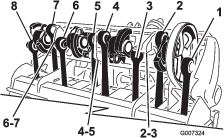
ProCore 1298 (Figure 43)
This unit is comprised of 2 independent coring heads with 6 arms each. The timing of either coring head is not dependent on the adjacent coring head. The timing marks are easily identified by the numbers cast into the crank arm castings and the raised locator on the bearing housings. The #1 arm always starts with the drive pulley.
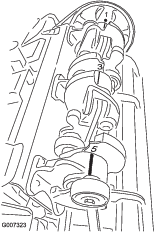
Removing the Aerator from the Tractor
Important: Refer to the PTO shaft owner’s manual for additional operating and safety information.
-
Park the vehicle on a level surface, not on a slope.
-
Disengage the PTO and engage the parking brake.
-
Shut off the engine and remove the key from the ignition switch.
-
Before leaving the operator's seat, wait for the engine and all moving parts to stop.
-
Install the storage stands and secure them to the aerator with the lynch pins (Figure 44).
Note: The aerator can be stored on the original shipping pallet.
-
Slowly lower the aerator until the storage stands contact the ground.
-
Loosen the locking nut and rotate the upper adjusting link to release the tension between the aerator and the tractor.
-
Remove the lynch pin and the top link pin securing the center link to the bracket. Retain the lynch pin and the top link pin with the aerator.
-
Disconnect the safety shield chains from the tractor PTO (CE only).
-
Pull back on the lock collar to disconnect the power shaft from the tractor PTO shaft.
-
Slide the PTO shaft back and remove it from the tractor.
-
Connect the PTO tether to the PTO shield to prevent the PTO shaft from contacting the ground (Figure 45).
-
Remove the lynch pins and slide the lower link arms off the hitch pins. Retain the lynch pins with the aerator.