Maintenance
Note: Determine the left and right sides of the machine from the normal operating position.
Maintenance Safety
-
Before you leave the operator’s position, do the following:
-
Park the machine on a level surface.
-
Shut off the machine.
-
Engage the parking brake.
-
Shut off the engine and remove the key (if equipped).
-
Wait for all movement to stop.
-
-
Allow machine components to cool before performing maintenance.
-
Perform only those maintenance instructions described in this manual. If major repairs are ever needed or assistance is desired, contact an authorized Toro distributor.
-
If possible, do not perform maintenance while the engine is running. Keep away from moving parts.
-
Do not check or adjust the chain tension when the vehicle engine is running.
-
Carefully release pressure from components with stored energy.
-
Support the machine with jack stands whenever you work under the machine.
-
After maintaining or adjusting the machine, ensure that all guards are installed.
-
Keep all parts of the machine in good working condition and all hardware tightened.
-
Replace all worn or damaged decals.
-
To ensure safe, optimal performance of the machine, use only genuine Toro replacement parts. Replacement parts made by other manufacturers could be dangerous, and such use could void the product warranty.
Recommended Maintenance Schedule(s)
Maintenance Service Interval | Maintenance Procedure |
---|---|
After the first hour |
|
After the first 10 hours |
|
Before each use or daily |
|
Every 40 hours |
|
Every 200 hours |
|
Every 800 hours |
|
Every 1,000 hours |
|
Every 2,000 hours |
|
Pre-Maintenance Procedures
Preparing for Maintenance
-
Shut off the hand-control switch for the topdresser.
-
Move the machine to a level surface.
-
Set the parking brake of the traction unit, shut off the engine, remove the key, and wait for all moving parts to stop before leaving the operator’s seat.
Raising the Machine
-
Empty the hopper.
-
Perform the steps in Preparing for Maintenance.
-
Use the skids as the jacking points.
-
Support the machine with jack stands.
-
When working on the wheels, pivot them up or down to expose wheel bolts.
Important: If you remove the wheels and installed them, torque wheel bolts as specified in Torquing the Wheel Bolts. Incorrect bolt torque could result in failure or loss of the wheel.
Lubrication
Grease Specification
No. 2 lithium grease
Greasing the Bearings and Bushings
Maintenance Service Interval | Maintenance Procedure |
---|---|
Every 200 hours |
|
-
Perform the steps in Preparing for Maintenance.
-
Lubricant each of the grease fitting described in the grease-fitting table with the specified grease.
Location | Quantity |
---|---|
Roller shaft bearing (Figure 15) | 4 |
Brush shaft bearing (Figure 15) | 1 |
Pivot bearing (Figure 16 | 4 |
Wheel bearing (Figure 16) | 4 |
Important: Lubricate the bearings to maintain a slight leakage between bearings and housings. Too much grease can cause overheating or damage to seals.
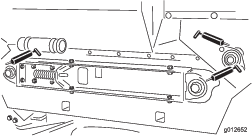
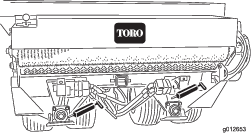
Note: Do not lubricate the drive chains unless they become stiff from rust. If the chain rusts, lightly lubricate it with a dry-type lubricant. This reduces the likelihood of sand build-up or other top-dressing material adhering to the chain.
Drive System Maintenance
Checking the Tire Air Pressure
Maintenance Service Interval | Maintenance Procedure |
---|---|
Before each use or daily |
|
-
Perform the steps in Preparing for Maintenance.
-
Check the tire air pressure.
You should measure 138 to 207 kPa (20 to 30 psi) air pressure.
-
If the tire air pressure is too low or too high, add air to or remove air from the tires until you measure 138 to 207 kPa (20 to 30 psi).
Torquing the Wheel Bolts
Maintenance Service Interval | Maintenance Procedure |
---|---|
After the first hour |
|
After the first 10 hours |
|
Every 200 hours |
|
Important: Failure to maintain proper torque could result in failure or loss of wheel.
-
Perform the steps in Preparing for Maintenance.
-
Torque 20 wheel bolts to 109 to 122 N∙m(80-90 ft-lb).
Tensioning the Wheel-Drive Chain
-
Perform the steps in Preparing for Maintenance.
-
Loosen carriage bolts and nuts that secure the hydraulic motor/pump to axle cradle (Figure 17).
-
Rotate motor sprocket assembly (Figure 17) until the wheel-drive chain deflects 3.2 mm (1/8 inch).
Note: Access to chain is through cutout in lower side of axle cradle.
Important: Do not overtension the chain or it will wear prematurely. Do not under-tension the chain or it will cause sprocket wear.
-
Tighten mounting bolts.
Tensioning the Conveyor-Belt Chain
-
Perform the steps in Preparing for Maintenance.
-
Remove the chain cover (Figure 18).
-
Loosen bolts and nuts that secure the motor and sprocket assembly to the main frame (Figure 19).
-
Rotate motor and sprocket assembly (Figure 19) in mounting slots until the conveyer-belt chain deflects 3.2 mm (1/8 inch).
Important: Do not overtension the chain or it will wear prematurely. Do not under-tension the chain or it will cause sprocket wear.
-
Tighten mounting bolts (Figure 19).
-
Install chain cover (Figure 18).
Belt Maintenance
Tensioning the Conveyor Belt
When conveyor belt is adjusted properly, the compressed length of each compression spring should be 112 mm (4-7/16 inches). Adjust conveyor belt as follows:
-
Empty the hopper.
-
Perform the steps in Preparing for Maintenance.
-
Loosen rear jam nut (Figure 20).
-
Adjust forward jam nut to compression spring to 112 mm (4-7/16 inches).
-
Tighten jam rear nut.
-
Repeat steps 3 through 5 at the other side of the machine.
-
Measure the distance between center points of the belt-roller shafts at each side of machine to ensure that the measurements are equal (Figure 21).
Equal distance measures approximately 895 mm (35-1/4 inches).
Replacing the Conveyor Belt
Preparing to Machine
-
Empty the hopper.
-
Perform the steps in Preparing for Maintenance.
-
Inspect hopper seals and gate edge for wear or torn edges (Figure 22).
Replace worn or damaged components to ensure proper operation of new conveyor belt.
Removing the Conveyer Chain
Disassembling the Slider Bed
-
Loosen forward and rear jam nuts on tension rod to release spring tension (Figure 25).
-
At each side of machine, remove 2 capscrews, 2 washers, and 2 locknuts that secure the hopper to slider-frame rails (Figure 26).
-
Pivot hopper rearward and lean it against wall, post, ladder, etc. (Figure 27).
Important: Do not allow hopper to rest against the rear of machine to avoid damaging the brush or the hydraulic couplers.Make sure that the hopper is pivoted beyond center and/or secured to wall or post to prevent it from accidentally falling on work area (Figure 27).
-
At the right side of machine, loosen 2 capscrews that secure slider-frame rail to the right fender (Figure 28). Ensure that the capscrews are loose enough to allow slider bed tip.
-
At the left side of machine, remove 2 capscrews and 2 washers that secure slider-frame rail to the left fender (Figure 29).
Removing the Belt
Cut belt and remove it from rollers.
Installing the Belt
-
Insert a lift bar though the hole at the left slider-frame rail, and raise the lift bar to tip frame rail slightly; refer to Figure 29 in Disassembling the Slider Bed.
-
Assemble the belt over the lift bar and rollers as far as possible.
-
Insert a plastic belt tool between each roller and the belt.
Rotate rollers until each tool is positioned to the outside of each roller. Insert the tool past rib in the center of belt.
-
Slide belt and belt tools further onto rollers until belt is centered on rollers.
-
Remove belt tools.
-
Align belt so that the belt rib fits into alignment grooves in each roller.
Assembling the Slider Bed
-
At the left side of machine, assemble the slider-frame rail to the left fender (Figure 30) with the 2 capscrews and 2 washers that you removed in Disassembling the Slider Bed, and tighten the capscrews.
-
At the right side of machine, tighten 2 capscrews that secure slider-frame rail to the right fender (Figure 31).
-
Carefully rotate the hopper down onto the slider-frame rails; refer to Figure 27 of Disassembling the Slider Bed.
-
At each side of machine, secure the hopper to slider-frame rails (Figure 32) with the 2 capscrews, 2 washers, and 2 locknuts that you removed in Disassembling the Slider Bed.
-
Tension the conveyer belt; refer to Tensioning the Conveyor Belt.
Installing the Conveyer Chain
-
Assemble the chain onto the small sprocket and secure the chain with the master link (Figure 33).
-
If you loosen the motor-mount bolts, tension the conveyer-belt chain, refer to Tensioning the Conveyor-Belt Chain.
-
Install the chain cover (Figure 34).
Hydraulic System Maintenance
Hydraulic System Safety
-
Seek immediate medical attention if fluid is injected into skin. Injected fluid must be surgically removed within a few hours by a doctor.
-
Ensure that all hydraulic-fluid hoses and lines are in good condition and all hydraulic connections and fittings are tight before applying pressure to the hydraulic system.
-
Keep your body and hands away from pinhole leaks or nozzles that eject high-pressure hydraulic fluid.
-
Use cardboard or paper to find hydraulic leaks.
-
Safely relieve all pressure in the hydraulic system before performing any work on the hydraulic system.
Checking the Hydraulic Lines and Hoses
Maintenance Service Interval | Maintenance Procedure |
---|---|
Before each use or daily |
|
Inspect hydraulic lines and hoses daily for leaks, kinked lines, loose mounting supports, wear, loose fittings, weather deterioration and chemical deterioration. Make all necessary repairs before operating the machine.
Hydraulic Fluid Specifications
The reservoir is filled at the factory with high-quality hydraulic fluid. Check the level of the hydraulic fluid before you first start the engine and daily thereafter; refer to Checking the Hydraulic Fluid Level.
Recommended hydraulic fluid: Toro PX Extended Life Hydraulic Fluid; available in 19 L (5 US gallon) pails or 208 L (55 US gallon) drums.
Note: A machine using the recommended replacement fluid requires less frequent fluid and filter changes.
Alternative hydraulic fluids: If Toro PX Extended Life Hydraulic Fluid is not available, you may use another conventional, petroleum-based hydraulic fluid having specifications that fall within the listed range for all the following material properties and that it meets industry standards. Do not use synthetic fluid. Consult with your lubricant distributor to identify a satisfactory product.
Note: Toro does not assume responsibility for damage caused by improper substitutions, so use products only from reputable manufacturers who will stand behind their recommendation.
Material Properties: | ||
Viscosity, ASTM D445 | cSt @ 40°C (104°F) 44 to 48 | |
Viscosity Index ASTM D2270 | 140 or higher | |
Pour Point, ASTM D97 | -37°C to -45°C (-34°F to -49°F) | |
Industry Specifications: | Eaton Vickers 694 (I-286-S, M-2950-S/35VQ25 or M-2952-S) |
Note: Many hydraulic fluids are almost colorless, making it difficult to spot leaks. A red dye additive for the hydraulic fluid is available in 20 ml (0.67 fl oz) bottles. A bottle is sufficient for 15 to 22 L (4 to 6 US gallons) of hydraulic fluid. Order Part No. 44-2500 from your authorized Toro distributor.
Important: Toro Premium Synthetic Biodegradable Hydraulic Fluid is the only synthetic biodegradable fluid approved by Toro. This fluid is compatible with the elastomers used in Toro hydraulic systems and is suitable for a wide-range of temperature conditions. This fluid is compatible with conventional mineral oils, but for maximum biodegradability and performance, the hydraulic system should be thoroughly flushed of conventional fluid. The oil is available in 19 L (5 US gallon) pails or 208 L (55 US gallon) drums from your authorized Toro distributor.
Checking the Hydraulic Fluid Level
Maintenance Service Interval | Maintenance Procedure |
---|---|
Before each use or daily |
|
-
Perform the steps in Preparing for Maintenance.
-
Clean area around filler neck and cap of hydraulic reservoir, and remove the cap (Figure 35).
-
Check the hydraulic-fluid level.
The fluid level should be 1/2 way up the screen in filler neck (Figure 35).
-
If level is low, add the specified hydraulic fluid to raise level.
-
Install the hydraulic-reservoir cap (Figure 35).
Replacing the Hydraulic Filter
Maintenance Service Interval | Maintenance Procedure |
---|---|
Every 800 hours |
|
Every 1,000 hours |
|
-
Perform the steps in Preparing for Maintenance.
-
Clean area around filter and hydraulic manifold, align a drain pan under filter, and remove filter (Figure 36).
-
Lubricate the gasket of the new filter with the specified hydraulic fluid; refer to Hydraulic Fluid Specifications.
-
Clean the filter-mounting area of the hydraulic manifold (Figure 36).
-
Thread the filter onto the filter mount until gasket manifold, then tighten filter one-half turn.
-
Tow machine to power the hydraulic system and check for hydraulic leaks.
Changing the Hydraulic Fluid
Maintenance Service Interval | Maintenance Procedure |
---|---|
Every 800 hours |
|
Every 2,000 hours |
|
Hydraulic reservoir fluid capacity: approximately 9.5 L (2.5 US gallon)
Important: If fluid becomes contaminated, contact your authorized Toro distributor because you must drain the complete hydraulic system. Contaminated fluid looks milky or black when compared to clean oil.
-
Perform the steps in Preparing for Maintenance.
-
Align a drain pan with a 9.5 L (2.5 US gallon) capacity under the hydraulic manifold (Figure 37).
-
Remove the return hose from the fitting in the hydraulic manifold and allow the hydraulic fluid to drain completely (Figure 37).
-
Install and tighten return hose (Figure 37).
-
Clean area around filler neck and cap of hydraulic reservoir, and remove the cap; refer to Figure 35 in Checking the Hydraulic Fluid Level.
-
Add approximately 9.5 L (2.5 US gallon) of the specified hydraulic fluid; refer to Hydraulic Fluid Specifications.
Important: Use only hydraulic fluids specified. Other fluids could cause damage to components of the hydraulic system.
-
Check level of fluid and add enough to the fluid level stated in Checking the Hydraulic Fluid Level.
Important: Do not overfill the reservoir with hydraulic fluid.
-
Install hydraulic-reservoir cap; refer to Figure 35 in Checking the Hydraulic Fluid Level.
Brush Maintenance
Checking the Brush for Position and Wear
Maintenance Service Interval | Maintenance Procedure |
---|---|
Every 40 hours |
|
Brush must make enough contact with conveyor belt to disperse top-dressing material but not restrict the rotation of the brush. A piece of stiff paper can be inserted between the conveyor belt and the brush to check the adjustment.
-
Insert a piece of stiff between the conveyor belt and the brush to check the adjustment.
-
Check that the brush is same height from side to side.
-
Check the condition of the brush bristles.
If the bristles are excessively worn replace the brush. If the bristles are worn uneven either replace the brush or adjust the brush position; refer to Adjusting the Brush Position.
Adjusting the Brush Position
Note: If you are using moist top-dressing material, you may need to adjust the brush position so that the bristles will whisk material from between conveyor belt lugs without excessively contacting smooth portion of belt.
-
Loosen nuts that secure the bearing housing (Figure 38) to right side of machine.
-
Loosen nuts that secure the brush motor (Figure 39) to left side of machine.
-
Slide brush into position at right side, and snug the nuts.
-
Slide brush into position at left side, and snug the nuts.
-
Insert a piece of stiff paper between the brush and the conveyor belt.
The brush must be the same height from side to side.
-
If the brush position is correct, tighten nuts.
If the brush position is not correct, repeat steps 1 through 6.
Cleaning
Washing the Machine
-
Thoroughly clean the machine, especially inside the hopper. Clean the hopper and conveyor belt area free of any sand particles.
-
Wash the machine as needed using water alone or with a mild detergent. You may use a rag when washing the machine.
Important: Do not use brackish or reclaimed water to clean the machine.
Important: Do not use power-washing equipment to wash the machine. Power-washing equipment may damage the electrical system, loosen important decals, or wash away necessary grease at friction points. Avoid excessive use of water at the wiring and hydraulic manifold.