Maintenance
Using the Kickstand When Tipping the Cutting Unit
Whenever the cutting unit has to be tipped to expose the bedknife/reel, prop up the rear of the cutting unit with the kickstand (supplied with the traction unit) to make sure that the nuts on the back end of the bedbar adjusting screws are not resting on the work surface (Figure 23).
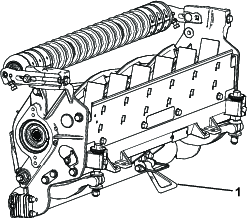
Lubricating the Cutting Unit
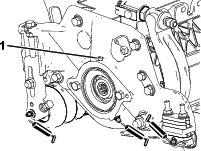
Each cutting unit has 5 grease fittings (Figure 24) that must be lubricated regularly with No. 2 lithium grease.
The lubrication points are the front roller (2), the rear roller (2), and the motor spline (1).
Note: Lubricating the cutting units immediately after washing helps purge water out of the bearings and increases bearing life.
-
Wipe each grease fitting with a clean rag.
-
Apply grease until clean grease comes out of the roller seals and the bearing relief valve.
-
Wipe excess grease away.
Relief-Grinding the Reel
The new reel has a land width of 1.3 to 1.5 mm (0.050 to 0.060 inch) and a 30 degree relief grind.
When the land width gets larger than 3 mm (0.120 inch) wide, do the following:
-
Apply a 30 degree relief grind on all reel blades until the land width is 1.3 mm (0.050 inch) wide (Figure 25).
-
Spin grind the reel to achieve <0.025 mm (0.001 inch) reel run-out.
Note: This causes the land width to grow slightly.
Note: To extend the longevity of the sharpness of the edge of the reel and the bedknife—after grinding the reel and/or the bedknife—check the reel to bedknife contact again after cutting 2 fairways, as any burrs will be removed, which may create improper reel to bedknife clearance and thus accelerate wear.
Servicing the Bedknife
The bedknife service limits are listed in the following chart.
Important: Operating the cutting unit with the bedknife below the service limit may result in poor after-cut appearance and reduce the structural integrity of the bedknife for impacts.
Bedknife Service Limit Chart | ||||
Bedknife | Part No. | Bedknife Lip Height* | Service Limit* | Grind AnglesTop/Front Angles |
Low HOC (Optional) | 120-1641 (27 inch)120-1642 (32 inch) | 5.6 mm (0.220 inch) | 4.8 mm (0.190 inch) | 10/5 degrees |
EdgeMax® (Optional) | 112-8910 (27 inch)112-8956 (32 inch) | 6.9 mm (0.270 inch) | 4.8 mm (0.190 inch) | 10/5 degrees |
Standard (Production) | 114-9388 (27 inch)114-9389 (32 inch) | 6.9 mm (0.270 inch) | 4.8 mm (0.190 inch) | 10/5 degrees |
Heavy Duty (Optional) | 114-9390 (27 inch)114-9391 (32 inch) | 9.3 mm (0.370 inch) | 4.8 mm (0.190 inch) | 10/5 degrees |
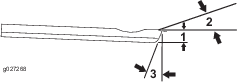
Note: All bedknife service limit measurements relate to the bottom of the bedknife (Figure 27).
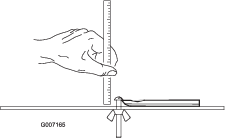
Checking the Top Grind Angle
The angle that you use to grind your bedknives is very important.
Use the angle indicator (Toro Part No. 131-6828) and the angle-indicator mount (Toro Part No. 131-6829) to check the angle that your grinder produces and then correct for any grinder inaccuracy.
-
Place the angle indicator on the bottom side of the bedknife as shown in Figure 28.
-
Press the Alt Zero button on the angle indicator.
-
Place the angle-indicator mount on the edge of the bedknife so that the edge of the magnet is mated with the edge of the bedknife (Figure 29).
Note: The digital display should be visible from the same side during this step as it was in step 1.
-
Place the angle indicator on the mount as shown in Figure 29.
Note: This is the angle that your grinder produces; it should be within 2 degrees of the recommended top grind angle.
Servicing the Bedbar
Removing the Bedbar
-
Turn the bedbar-adjuster screws counterclockwise to back the bedknife away from the reel (Figure 30).
-
Back out the spring-tension nut until the washer is no longer tensioned against the bedbar (Figure 30).
-
On each side of the machine, loosen the locknut securing the bedbar bolt (Figure 31).
-
Remove each bedbar bolt, allowing the bedbar to be pulled downward and removed from machine bolt (Figure 31). Account for 2 nylon washers and 1 stamped steel washer on each end of the bedbar (Figure 32).
Assembling the Bedbar
-
Install the bedbar, positioning the mounting ears between the washer and the bedbar adjuster.
-
Secure the bedbar to each side plate with the bedbar bolts (nuts on bolts) and 6 washers.
-
Position a nylon washer on each side of the side-plate boss.
-
Place a steel washer outside each of the nylon washers (Figure 32).
Note: Torque the bedbar bolts to 37 to 45 N∙m (27 to 33 ft-lb). Tighten the locknuts until the outside steel washer stops rotating and end play is removed, but do not overtighten or deflect the side plates. The washers on the inside may have a gap.
-
Tighten the spring-tension nut until the spring is collapsed, then back off 1/2 turn (Figure 33).
Installing the Bedknife
-
Remove the rust, scale, and corrosion from the bedbar surface and apply a thin layer of oil to the bedbar surface.
-
Clean the screw threads.
-
Apply anti-seize compound to the screws and install the bedknife to the bedbar as follows (Figure 34):
-
Grind the bedknife.
Servicing the HD Dual Point Adjusters (DPA)
-
Remove all parts (refer to the Installation Instructions for the HD DPA Kit (Model No. 120-7230) and to Figure 36).
-
Apply anti-seize compound to the inside of the bushing area on the carrier frame of the cutting unit (Figure 36).
-
Align the keys on flange bushings to the slots in the frame and install the bushings (Figure 36).
-
Install a wave washer onto the adjuster shaft and slide the adjuster shaft into the flange bushings in the cutting unit frame (Figure 36).
-
Secure the adjuster shaft with a flat washer and lock nut (Figure 36). Torque the lock nut to 20 to 27 N-m (15 to 20 ft-lb).
Note: The bedbar adjuster shaft has left-hand threads.
-
Apply anti-seize compound to the threads of the bedbar-adjuster screw that fit into the adjuster shaft.
-
Thread the bedbar-adjuster screw into the adjuster shaft.
-
Loosely install the hardened washer, spring, and spring-tension nut onto the adjuster screw.
-
Install the bedbar, positioning the mounting ears between the washer and the bedbar adjuster.
-
Secure the bedbar to each side plate with the bedbar bolts (nuts on bolts) and 6 washers.
Note: Position a nylon washer on each side of the side plate boss. Place a steel washer outside each of the nylon washers (Figure 36). Torque the bedbar bolts to 27 to 36 N∙m (240 to 320 in-lb). Tighten the locknuts until the outside steel washer stops rotating and end play is removed, but do not overtighten or deflect the side plates. The washers on the inside may have a gap (Figure 32).
-
Tighten the nut on each bedbar-adjuster assembly until the compression spring is fully compressed, then loosen the nut 1/2 turn (Figure 33).
-
Repeat the procedure on the other end of the cutting unit.
-
Adjust the bedknife to the reel.
Servicing the Roller
The Roller Rebuild Kit (Part No. 114-5430) and the Roller Rebuild Tool Kit (Part No. 115-0803) (Figure 37) are available for servicing the roller. The Roller Rebuild Kit includes all the bearings, bearing nuts, inner seals, and outer seals to rebuild a roller. The Roller Rebuild Tool Kit includes all the tools and the installation instructions required to rebuild a roller with the roller rebuild kit. Refer to your parts catalog or contact your authorized Toro distributor for assistance.
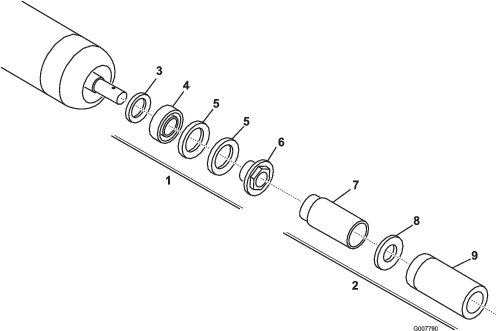