Maintenance
Note: Determine the left and right sides of the machine from the normal operating position.
Caution
If you leave the key in the switch, someone could accidently start the engine and seriously injure you or other bystanders.
Remove the key from the switch before you perform any maintenance.
Maintenance Safety
-
Park the machine on a level surface, disengage the auxiliary hydraulics, lower the attachment, engage the parking brake (if equipped), shut off the engine, and remove the key. Wait for all movement to stop and allow the machine to cool before adjusting, cleaning, storing, or repairing it.
-
Clean up oil or fuel spills.
-
Do not allow untrained personnel to service the machine.
-
Use jack stands to support the components when required.
-
Carefully release pressure from components with stored energy; refer to Relieving Hydraulic Pressure.
-
Disconnect the battery before making any repairs; refer to Using the Battery-Disconnect Switch.
-
Keep your hands and feet away from the moving parts. If possible, do not make adjustments with the engine running.
-
Keep all parts in good working condition and all hardware tightened. Replace all worn or damaged decals.
-
Do not tamper with the safety devices.
-
Attachments can change the stability and the operating characteristics of the machine.
-
Use only genuine Toro replacement parts.
-
If any maintenance or repair requires the loader arms to be in the raised position, secure the arms in the raised position with the hydraulic-cylinder lock(s).
Recommended Maintenance Schedule(s)
Maintenance Service Interval | Maintenance Procedure |
---|---|
After the first 8 hours |
|
After the first 50 hours |
|
Before each use or daily |
|
Every 25 hours |
|
Every 50 hours |
|
Every 100 hours |
|
Every 400 hours |
|
Every 500 hours |
|
Every 800 hours |
|
Every 1,000 hours |
|
Every 1,500 hours |
|
Yearly |
|
Yearly or before storage |
|
Every 2 years |
|
Important: Refer to your engine owner’s manual for additional maintenance procedures.
Pre-Maintenance Procedures
Using the Cylinder Locks
Warning
The loader arms may lower when in the raised position, crushing anyone under them.
Install the cylinder lock(s) before performing maintenance that requires raised loader arms.
Installing the Cylinder Locks
-
Remove the attachment.
-
Raise the loader arms to the fully raised position.
-
Shut off the engine and remove the key.
-
Remove the 2 pins securing the cylinder lock to the posts on the side of the machine.
-
Slide the cylinder lock over the lift-cylinder rod (Figure 37).
-
Repeat step 4 and 5 for the other side of the machine.
-
Slowly lower the loader arms until the cylinder locks contact the cylinder bodies and rod ends.
Removing and Storing the Cylinder Locks
Important: Remove the cylinder locks from the rods and fully secure them in the storage position before operating the machine.
-
Start the engine.
-
Raise the loader arms to the fully raised position.
-
Shut off the engine and remove the key.
-
Remove the pins securing the cylinder locks.
-
Place the cylinder locks on the posts on the sides of the machine and secure with the pins.
-
Lower the loader arms.
Accessing Internal Components
Warning
Opening or removing covers, hoods, and screens while the engine is running could allow you to contact moving parts, seriously injuring you.
Before opening any of the covers, hoods, and screens, shut off the engine, remove the key from the key switch, and allow the engine to cool.
Opening the Hood
Closing the Hood
-
Lower the hood, and hold it down while you secure the latches..
-
Tighten the hood-locking screw (Figure 38).
-
Remove the cylinder locks and lower the loader arms.
Opening the Rear-Access Cover
Removing the Rear Screen
-
Open the rear-access cover; refer to Opening the Rear-Access Cover.
-
Loosen the 2 bolts securing the bottom of the screen (Figure 41).
-
Loosen the 2 knobs on the screen (Figure 41).
-
Lift the screen and remove it (Figure 41).
Removing the Bottom Plate
-
Remove the 2 bolts securing the bottom plate (Figure 42).
-
Remove the bottom plate.
Removing the Front Cover
-
Raise the loader arms and secure them with the cylinder locks.
-
Loosen the 2 bolts securing the front cover to the machine (Figure 43).
-
Slide the cover off the machine.
-
When installing the cover, torque the bolts to 41 N∙m (30 ft-lb).
Lubrication
Lubricating the Machine
Maintenance Service Interval | Maintenance Procedure |
---|---|
Before each use or daily |
|
Every 100 hours |
|
Grease Type: General-purpose grease.
-
Park the machine on a level surface, engage the parking brake, and lower the loader arms.
-
Shut off the engine and remove the key.
-
Clean the grease fittings with a rag.
-
Connect a grease gun to each fitting (Figure 45, Figure 46, and Figure 47).
Note: Raise the loader arms before greasing the fittings in Figure 47.
-
Pump grease into the fittings until grease begins to ooze out of the bearings (approximately 3 pumps).
-
Wipe up any excess grease.
-
Lubricate the quick-attach linkages using spray lubricant (Figure 48).
Engine Maintenance
Engine Safety
-
Shut off the engine and remove the key before checking the oil or adding oil to the crankcase.
-
Keep your hands, feet, face, clothing, and other body parts away from the muffler and other hot surfaces.
Servicing the Air Cleaner
Maintenance Service Interval | Maintenance Procedure |
---|---|
Before each use or daily |
|
Every 100 hours |
|
Yearly |
|
Check the air-cleaner body for damage, which could cause an air leak. Replace the body if it is damaged. Check the intake system for leaks, damage, or loose hose clamps.
Service the air-cleaner filter only when the service indicator (Figure 49) requires it. Changing the air filter before it is necessary increases the chance of dirt entering the engine when you remove the filter.
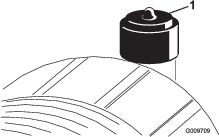
Important: Ensure that the cover is seated correctly and seals with the air-cleaner body.
Servicing the Engine Oil
Maintenance Service Interval | Maintenance Procedure |
---|---|
After the first 50 hours |
|
Before each use or daily |
|
Every 400 hours |
|
Engine-Oil Specifications
Oil Type: Detergent diesel engine oil (API service CH-4 or higher)
Crankcase Capacity: with filter 7.0 L (1.85 US gallons)
Viscosity: See the table below.
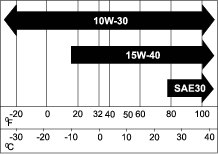
Checking the Engine-Oil Level
-
Park the machine on a level surface, engage the parking brake, and lower the loader arms.
-
Shut off the engine, remove the key, and allow the engine to cool.
-
Open the hood.
-
Clean the area around the oil dipstick and oil-fill cap (Figure 53).
-
Check the oil and add additional oil as needed (Figure 54).
Important: Do not overfill the crankcase with oil; if the oil in the crankcase is too high and you run the engine, you may damage the engine.
-
Close the hood.
Changing the Engine Oil and Filter
-
Start the engine and let it run for 5 minutes.
Note: This warms the oil so that it drains better.
-
Park the machine on a level surface.
-
Raise the loader arms and secure with the cylinder locks; refer to Installing the Cylinder Locks.
-
Engage the parking brake, shut off the engine, and remove the key.
-
Drain the oil beneath the platform (Figure 55).
Caution
Components will be hot if the machine has been running. If you touch hot components, you may be burned.
Use care to avoid touching hot components while changing the oil and/or filter.
-
Torque the drain plug to 46 to 56 N∙m (34 to 42 ft-lb).
-
Open the hood and secure the prop rod (if applicable).
-
Remove the front cover assembly; refer to Removing the Front Cover Assembly.
-
Place a shallow pan or rag under the filter to catch oil.
-
Change the oil filter (Figure 56).
-
Remove the oil-fill cap and slowly pour approximately 80% of the specified amount of oil in through the valve cover.
-
Check the oil level.
-
Slowly add additional oil to bring the level to the upper hole on the dipstick.
-
Replace the fill cap.
-
Install the front cover assembly.
-
Close the hood.
Fuel System Maintenance
Danger
In certain conditions, fuel is extremely flammable and highly explosive. A fire or explosion from fuel can burn you and others and can damage property.
Refer to Fuel Safety for a complete list of fuel related precautions.
Draining the Water Separator
Maintenance Service Interval | Maintenance Procedure |
---|---|
Every 50 hours |
|
-
Park the machine on a level surface, engage the parking brake, and lower the loader arms.
-
Shut off the engine and remove the key.
-
Open the rear access cover; refer to Opening the Rear-Access Cover
-
Remove the rear screen; refer to Removing the Rear Screen
-
Place a container under the water separator.
-
Disconnect the wire harness from the water separator (Figure 57).
-
Unscrew the switch from bottom of the filter canister and allow the water to drain (Figure 57).
-
Install the switch (Figure 57).
-
Connect the wire harness to the switch (Figure 57).
-
Install the rear screen and tighten the knobs and bolts to secure it.
-
Close the rear-access cover and install the fastener to secure it.
-
Bleed the fuel system; refer to Bleeding the Fuel System.
Replacing the Water Separator Filter
Maintenance Service Interval | Maintenance Procedure |
---|---|
Every 500 hours |
|
-
Park the machine on a level surface, engage the parking brake, and lower the loader arms.
-
Shut off the engine and remove the key.
-
Open the rear access cover; refer to Opening the Rear-Access Cover.
-
Remove the rear screen; refer to Removing the Rear Screen.
-
Disconnect the wire harness from the water separator.
-
Unscrew the switch and drain the water separator (Figure 57).
-
Clean the area where the filter mounts.
-
Remove the filter and clean the mounting surface.
-
Lubricate the gasket on the filter with clean oil.
-
Install the filter by hand until the gasket contacts the mounting surface; then rotate an additional 1/2 turn.
-
Install the switch to the filter.
-
Connect the wire harness to the switch.
-
Install the rear screen and tighten the knobs and bolts.
-
Close the rear-access cover and install the fastener.
Replacing the Fuel Filter Canister
Maintenance Service Interval | Maintenance Procedure |
---|---|
Every 400 hours |
|
-
Park the machine on a level surface, engage the parking brake, and lower the loader arms.
-
Shut off the engine and remove the key.
-
Open the rear access cover; refer to Opening the Rear-Access Cover
-
Remove the rear screen; refer to Removing the Rear Screen
-
Place a clean container under the fuel filter canister (Figure 58).
-
Remove the filter canister and clean the mounting surface.
-
Lubricate the gasket on the new filter canister with clean oil.
-
Fill the canister with fuel.
-
Install the filter canister by hand until the gasket contacts the mounting surface, then rotate it an additional 1/2 turn.
-
Install the rear screen and tighten the knobs and bolts to secure it.
-
Close the rear-access cover and install the fastener to secure it.
Checking the Fuel Lines and Connections
Maintenance Service Interval | Maintenance Procedure |
---|---|
Every 400 hours |
|
Inspect the fuel lines and connections for deterioration, damage, or loose connections. Tighten any loose connections and contact your Authorized Service Dealer for assistance in fixing damaged fuel lines.
Bleeding the Fuel System
You must bleed the fuel system before starting the engine if any of the following situations have occurred:
-
Initial startup of a new machine
-
The engine has ceased running due to a lack of fuel.
-
Maintenance has been performed upon fuel-system components (e.g., filter replaced).
Use the manual pump on the water separator to bleed air out of the fuel system.
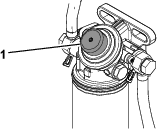
Draining the Fuel Tank(s)
Maintenance Service Interval | Maintenance Procedure |
---|---|
Every 500 hours |
|
Have an Authorized Service Dealer drain and clean the fuel tank(s).
Electrical System Maintenance
Electrical System Safety
-
Disconnect the battery before repairing the machine. Disconnect the negative terminal first and the positive last. Connect the positive terminal first and the negative last.
-
Charge the battery in an open, well-ventilated area, away from sparks and flames. Unplug the charger before connecting or disconnecting the battery. Wear protective clothing and use insulated tools.
-
Battery acid is poisonous and can cause burns. Avoid contact with skin, eyes, and clothing. Protect your face, eyes, and clothing when working with a battery.
-
Battery gases can explode. Keep cigarettes, sparks, and flames away from the battery.
Servicing the Battery
Maintenance Service Interval | Maintenance Procedure |
---|---|
Every 50 hours |
|
Using the Battery-Disconnect Switch
-
Park the machine on a level surface, engage the parking brake, and lower the loader arms.
-
Shut off the engine and remove the key.
-
Open the rear-access cover.
-
Turn the battery-disconnect switch to the ON or OFF position to perform the following:
-
To energize the machine electrically, rotate the battery-disconnect switch clockwise to the ON position (Figure 60).
-
To de-energize the machine electrically, rotate the battery-disconnect switch counterclockwise to the OFF position (Figure 60).
-
Removing the Battery
-
Park the machine on a level surface, engage the parking brake, and lower the loader arms.
-
Shut off the engine and remove the key.
-
Remove the rear screen; refer to Removing the Rear Screen.
-
Disconnect the negative (black) ground cable from the battery post (Figure 61). Retain the fasteners.
-
Slide the rubber cover off the positive (red) cable.
-
Disconnect the positive (red) cable from the battery post (Figure 61). Retain the fasteners.
-
Loosen the 3 bolts securing the battery tray and remove the tray with the battery (Figure 61).
-
Remove the wing nut and rod.
-
Remove the battery.
Charging the Battery
Warning
Charging the battery produces gasses that can explode.
Never smoke near the battery and keep sparks and flames away from battery.
Important: Always keep the battery fully charged (1.265 specific gravity). This is especially important to prevent battery damage when the temperature is below 0°C (32°F).
-
Remove the battery from the machine; refer to Removing the Battery.
-
Charge the battery for 4 to 8 hours at a rate of 3 to 4 A (Figure 62). Do not overcharge the battery.
-
When the battery is fully charged, unplug the charger from the electrical outlet, then disconnect the charger leads from the battery posts (Figure 62).
Cleaning the Battery
Note: Keep the terminals and the entire battery case clean, because a dirty battery discharges slowly.
-
Park the machine on a level surface, engage the parking brake (if equipped), and lower the loader arms.
-
Shut off the engine and remove the key.
-
Remove the battery from the machine; Removing the Battery.
-
Wash the entire case with a solution of baking soda and water.
-
Rinse the battery with clear water.
-
Coat the battery posts and cable connectors with Grafo 112X (skin-over) grease (Toro Part No. 505-47) or petroleum jelly to prevent corrosion.
-
Install the battery; refer to Installing the Battery.
Installing the Battery
-
Place the battery on the battery tray and secure it with the wing nut and rod (Figure 61).
-
Install the battery tray to the machine and secure with the 3 bolts (Figure 61). Torque the bolts to 41 N∙m (30 ft-lb).
-
Using the fasteners previously removed, install the positive (red) battery cable to the positive (+) battery terminal (Figure 61).
-
Slide the red terminal boot onto the positive battery post.
-
Using the fasteners previously removed, install the negative (black) battery cable to the negative (-) battery terminal (Figure 61).
-
Install the rear screen.
Servicing a Replacement Battery
The original battery is maintenance-free and does not require service. For servicing a replacement battery, refer to the battery manufacturer’s instructions.
Jump-Starting the Machine
Warning
Jump-starting the battery can produce gasses that can explode.
Do not smoke near the battery, and keep sparks and flames away from battery.
-
Open the rear-access cover; refer to Opening the Rear-Access Cover.
-
Remove the rear screen; refer to Removing the Rear Screen.
-
Check and clean corrosion from the battery terminals before jump-starting. Ensure that the connections are tight.
Caution
Corrosion or loose connections can cause unwanted electrical voltage spikes at any time during the jump-starting procedure.
Do not attempt to jump-start the machine with loose or corroded battery terminals, or damage to the engine may occur.
Danger
Jump-starting a weak battery that is cracked or frozen or has a low electrolyte level or an open/shorted battery cell can cause an explosion, resulting in serious personal injury.
Do not jump-start a weak battery if these conditions exist.
-
Make sure that the booster battery is a good and fully charged lead-acid battery at 12.6 V or greater.
Note: Use properly sized jumper cables with short lengths to reduce voltage drop between systems. Make sure that the cables are color coded or labeled for the correct polarity.
Warning
Batteries contain acid and produce explosive gases.
-
Shield your eyes and face from the batteries at all times.
-
Do not lean over the batteries.
Note: Ensure that the vent caps are tight and level. Place a damp cloth, if available, over any vent caps on both batteries. Also ensure that the machines do not touch and that both electrical systems are off and at the same rated system voltage. These instructions are for negative ground systems only.
-
-
Connect the positive (+) cable to the positive (+) terminal of the discharged battery that is wired to the starter or solenoid as shown in Figure 63.
-
Connect the other end of the positive (+) jumper cable to the positive terminal of the battery in the other machine.
-
Connect an end of the negative (-) jumper cable to the negative post of the battery in the other machine.
-
Connect the other end of the negative (-) jumper cable to a ground point, such as an unpainted bolt or chassis member.
-
Start the engine in the other machine. Let it run a few minutes, then start your engine.
-
Remove the cables in the reverse order of connection.
-
Install the cover to the jump post.
Servicing the Fuses
The electrical system is protected by fuses. It requires no maintenance; however, if a fuse blows, check the component/circuit for a malfunction or a short. Figure 64 illustrates the fuse block location.
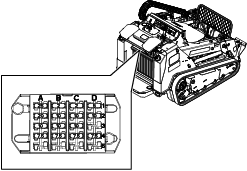
A | B | C | D |
Engine | Logic-Tec | Telematics | System |
(25 A) | (2 A) | (2 A) | (5 A) |
Starter solenoid | Power point | Display | Horn |
(20 A) | (10 A) | (10 A) | (10 A) |
Accessory connection | Accessory connection | Accessory connection | - |
(10 A) | (10 A) | (10 A) | |
Tec power | Tec power | Tec power | Tec power |
(7.5 A) | (7.5 A) | (7.5 A) | (7.5 A) |
- | - | - | - |
Note: If the machine does not start, either the main circuit or the control panel/relay fuse could be blown.
Drive System Maintenance
Replacing the Drive-Motor Planetary Gear Oil
Maintenance Service Interval | Maintenance Procedure |
---|---|
Every 1,000 hours |
|
Oil Type: SAE 85W-140 gear oil
Capacity: 0.9 L (30 fl oz)
-
Start the engine and drive the machine for 5 minutes.
Note: This warms the gear oil so that it drains better.
-
Park the machine on a level surface so that the drain plug is in the 6 o’clock position (Figure 65), engage the parking brake, and lower the loader arms.
-
Shut off the engine and remove the key.
-
Place a drain pan under the drive motor.
-
Remove the check plug and the drain plug and allow the gear lubricant to drain (Figure 65).
-
Install the drain plug (Figure 65).
-
Fill the drive motor with gear oil through the check hole until the oil is up to the bottom of the hole.
-
Install the check plug.
-
Repeat for the other drive motor.
-
Start the engine and drive the machine a few minutes.
-
Park the machine on a level surface, engage the parking brake, shut off the engine and remove the key.
-
Remove the check plugs and verify that the oil level is at the bottom of the oil-level check hole. Add oil as needed.
-
Install the check plugs. Torque the check and drain plugs to 30 to 40 N∙m (22 to 30 ft-lb).
Servicing the Tracks
Maintenance Service Interval | Maintenance Procedure |
---|---|
After the first 8 hours |
|
After the first 50 hours |
|
Before each use or daily |
|
Every 50 hours |
|
Cleaning the Tracks
-
Park the machine on a level surface and engage the parking brake.
-
With the bucket installed and angled downward, lower it into the ground so that the front of the traction unit lifts off the ground a few centimeters (inches).
-
Shut off the engine and remove the key.
-
Using a water hose or pressure washer, remove dirt from each track system.
Important: Ensure that you use high-pressure water to wash only the track area. Do not use a high-pressure washer to clean the rest of the traction unit. Do not use high pressure water between the drive sprocket and the traction unit or you may damage the motor seals. High-pressure washing can damage the electrical system and hydraulic valves or deplete grease.
Important: Ensure that you fully clean the road wheels, the front wheel, and the drive sprocket (Figure 67). The road wheels should rotate freely when clean.
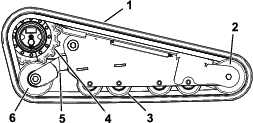
Checking the Track Tension
-
Park the machine on a level surface and engage the parking brake.
-
With the bucket installed and angled downward, lower it into the ground so that the front of the traction unit lifts off the ground a few centimeters (inches).
Note: If you do not have a bucket, raise the machine and support it using jackstands rated for the weight of the machine; refer to Specifications.
-
Shut off the engine and remove the key.
-
Verify that the gap between the 2nd road wheel from the rear and the track is 20 mm (0.8 inch) as shown in Figure 68. If adjustment is needed, proceed to Adjusting the Track Tension
Adjusting the Track Tension
-
Park the machine on a level surface and engage the parking brake.
-
Place a 15 x 15 cm (6 x 6 inch) block under the rear frame of the machine, directly behind the track being tensioned.
-
With the bucket installed and angled downward, lower it into the ground so that the front of the traction unit lifts off the ground a few centimeters (inches) and the machine tips back onto the block until the track is completely off the ground.
Note: If you do not have a bucket, raise the machine and support it using jackstands rated for the weight of the machine; refer to Specifications.
-
Shut off the engine and remove the key.
-
Loosen the 2 bolts and rotate the access cover open (Figure 69).
-
Remove the locking bolt, spacer, and nut (Figure 70).
-
Using a 1/2 inch drive ratchet, turn the tensioning screw until the gap between the road wheel and track is 20 mm (0.79 inch) as shown in Figure 68.
Note: Turning the screw counter-clockwise tightens the track; turning the screw clockwise loosens the track.
-
Align the notch in the tension screw to the nearest locking-bolt hole and secure the screw with the locking bolt, spacer, and nut (Figure 70.
-
Repeat the procedure for the other track if needed.
Replacing the Tracks
Removing the Tracks
-
Remove any attachments.
-
Park the machine on a level surface, ensuring that 1 segment of the sprocket is not engaged with the track.
-
Lower the loader arms.
-
Shut off the engine and remove the key.
-
Raise the machine off the ground so that the bottom of the track is at least 10.2 cm (4 inches) off the ground. Support the machine using jack stands.
Note: Use jack stands rated for your machine.
Warning
Mechanical or hydraulic jacks may fail to support the machine and cause serious injury.
Use jack stands when supporting the machine.
-
Remove the locking bolt, spacer, and nut (Figure 70).
-
Using a 1/2-inch drive ratchet, release the drive tension by turning the tensioning screw clockwise (Figure 70 and Figure 72).
-
Remove the segment of the drive sprocket not engaged with the track.
Important: If you do not remove the sprocket segment, it may be difficult to install a new track without damaging it.
-
Start the machine and disengage the parking brake.
-
Move the traction control forward until a second segment of the sprocket is not engaged with the track.
-
Shut off the engine and remove the key.
-
Remove the sprocket segment (Figure 73).
-
Start the machine and disengage the parking brake.
-
Move the traction control forward until the last segment of the sprocket is not engaged with the track.
Note: You do not need to remove this segment.
-
Remove the track from the track frame.
Installing the Tracks
-
Wrap the new track around the front wheel (Figure 72).
-
Push the track under and between the road wheels and wrap it around the rear tension wheel (Figure 72).
-
Pry the track cleats onto the planetary housing.
-
Start the engine and disengage the parking brake.
-
Move the traction control forward until the drive sprocket segment engages with the track (Figure 74).
-
Shut off the engine and remove the key.
-
Apply thread-locking compound to the bolts of 1 drive sprocket segment that you removed and install the sprocket segment (Figure 73). Torque the bolts to 247 to 301 N∙m (182 to 222 ft-lb).
-
Start the engine and disengage the parking brake.
-
Move the traction control forward until both drive sprocket segments engage the track.
-
Apply thread-locking compound to the bolts of the other drive sprocket segment that you removed and install the sprocket segment (Figure 74). Torque the bolts to 247 to 301 N∙m (182 to 222 ft-lb).
Note: Install the sprocket so that the casting numbers in the sprocket face outward.
-
Using a 1/2 inch drive ratchet, turn the tensioning screw counterclockwise until the gap between the road wheel and track is 20 mm (0.79 inch) as shown in Figure 68.
-
Align the notch in the tension screw to the nearest locking-bolt hole and secure the screw with the locking bolt, spacer, and nut. Torque the locking bolt to 1,130 N∙cm (100 in-lb).
-
Lower the machine to the ground.
-
Repeat the procedure to replace the other track.
-
Close the access cover and tighten the bolts (Figure 69). Torque the bolts to 41 N∙m (30 ft-lb).
Cooling System Maintenance
Cooling System Safety
-
Swallowing engine coolant can cause poisoning; keep out of reach from children and pets.
-
Discharge of hot, pressurized coolant or touching a hot radiator and surrounding parts can cause severe burns.
-
Always allow the engine to cool at least 15 minutes before removing the radiator cap.
-
Use a rag when opening the radiator cap, and open the cap slowly to allow steam to escape.
-
Servicing the Cooling System
Maintenance Service Interval | Maintenance Procedure |
---|---|
Before each use or daily |
|
Every 100 hours |
|
Cleaning the Radiator Screen
Maintenance Service Interval | Maintenance Procedure |
---|---|
Before each use or daily |
|
Remove any buildup of grass, dirt or other debris from the radiator screen with compressed air.
Checking the Engine-Coolant Level
The cooling system is filled with a 50/50 solution of water and permanent ethylene-glycol antifreeze.
-
Park the machine on a level surface, lower the loader arms, engage the parking brake, and shut off the engine.
-
Remove the key from the key switch and allow the engine to cool.
-
Open the hood.
-
Check the coolant level in the expansion tank (Figure 75).
Note: The coolant level should be at or above the mark on the side of the tank.
-
If the coolant level is low, remove the expansion tank cap and add a 50/50 mixture of water and permanent ethylene-glycol antifreeze.
Important: Do not overfill the expansion tank.
-
Install the expansion-tank cap.
Changing the Engine Coolant
Maintenance Service Interval | Maintenance Procedure |
---|---|
Every 800 hours |
|
Have an Authorized Service Dealer change the engine coolant yearly.
If you need to add engine coolant, refer to Checking the Engine-Coolant Level.
Belt Maintenance
Checking and Adjusting the Alternator Belt Tension
Maintenance Service Interval | Maintenance Procedure |
---|---|
Before each use or daily |
|
Every 100 hours |
|
Every 500 hours |
|
-
Park the machine on a level surface, engage the parking brake, and lower the loader arms.
-
Shut off the engine and remove the key.
-
Open the hood.
-
Apply 30 N (22 in-lb) of force to the alternator belt, midway between the pulleys (Figure 76).
-
If the belt does not deflect 11 mm (7/16 inch), complete the following procedure to tension the belt:
-
Loosen the bolt securing the alternator to the engine and the bolt securing the brace to the alternator.
-
Insert a pry bar between the alternator and engine, and pry out at the alternator.
-
When you obtain the proper tension, tighten the alternator and brace bolts to secure the adjustment.
-
Controls System Maintenance
Adjusting the Controls
The factory adjusts the controls before shipping the machine. However, after many hours of use, you may need to adjust the traction control alignment, the NEUTRAL position of the traction control, and the tracking of the traction control in the full forward position.
Contact your Authorized Service Dealer to adjust the controls of your machine.
Hydraulic System Maintenance
Hydraulic System Safety
-
Seek immediate medical attention if fluid is injected into skin. Injected fluid must be surgically removed within a few hours by a doctor.
-
Ensure that all hydraulic-fluid hoses and lines are in good condition and all hydraulic connections and fittings are tight before applying pressure to the hydraulic system.
-
Keep your body and hands away from pinhole leaks or nozzles that eject high-pressure hydraulic fluid.
-
Use cardboard or paper to find hydraulic leaks.
-
Safely relieve all pressure in the hydraulic system before performing any work on the hydraulic system.
Relieving Hydraulic Pressure
To relieve hydraulic pressure while the engine is on, disengage the auxiliary hydraulics and fully lower and retract the loader arms.
To relieve the pressure while the engine is off, cycle the joystick between the forward positions to lower the loader arms (Figure 77).
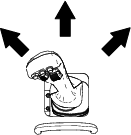
Hydraulic-Fluid Specifications
Maintenance Service Interval | Maintenance Procedure |
---|---|
Every 100 hours |
|
Every 400 hours |
|
Every 1,000 hours |
|
Every 1,500 hours |
|
Every 2 years |
|
Hydraulic-Tank Capacity: 57.7 L (15.25 US gallons)
Use only 1 of the following fluids in the hydraulic system:
-
Toro Premium Transmission/Hydraulic Tractor Fluid (refer to your Authorized Service Dealer for more information)
-
Toro PX Extended Life Hydraulic Fluid (refer to your Authorized Service Dealer for more information)
-
If either of the above Toro fluids are not available, you may use another Universal Tractor Hydraulic Fluid (UTHF), but they must be only conventional, petroleum-based products. The specifications must fall within the listed range for all the following material properties and the fluid should meet the listed industry standards. Check with your hydraulic fluid supplier to determine if the fluid meets these specifications.
Note: Toro will not assume responsibility for damage caused by improper substitutions, so use only products from reputable manufacturers who will stand behind their recommendations.
Material Properties Viscosity, ASTM D445 cSt at 40°C: 55 to 62 cSt at 100°C: 9.1 to 9.8 Viscosity index, ASTM D2270 140 to 152 Pour Point, ASTM D97 -37 to -43°C (-35 to -46°F) Industry Standards API GL-4, AGCO Powerfluid 821 XL, Ford New Holland FNHA-2-C-201.00, Kubota UDT, John Deere J20C, Vickers 35VQ25 and Volvo WB-101/BM Note: Many hydraulic fluids are almost colorless, making it difficult to spot leaks. A red dye additive for the hydraulic system fluid is available in 20 ml (2/3 fl oz) bottles. One bottle is sufficient for 15 to 22 L (4 to 6 US gallons) of hydraulic fluid. Order Part No. 44-2500 from your Authorized Toro Dealer.
Checking the Hydraulic-Fluid Level
Maintenance Service Interval | Maintenance Procedure |
---|---|
Every 25 hours |
|
Important: Always use the correct hydraulic fluid. Unspecified fluids will damage the hydraulic system. Refer to Hydraulic-Fluid Specifications.
-
Remove any attachments.
-
Park the machine on a level surface and engage the parking brake.
-
Raise the loader arms and install the cylinder locks.
-
Shut off the engine and remove the key.
-
Remove the front cover; refer to Removing the Front Cover.
-
Clean the area around the filler neck of the hydraulic tank (Figure 78).
-
Remove the filler-neck cap and check the fluid level on the dipstick (Figure 79).
Note: The fluid level should be between the 2 notches of the dipstick while the arms are lowered or at the lower notch while the arms are raised.
-
If the level is low, add enough fluid to raise it to the proper level.
-
Install the filler-neck cap.
-
Install the front cover.
Replacing the Hydraulic Filters
Important: Do not substitute an automotive oil filter; otherwise, severe hydraulic system damage may occur.
-
Park the machine on a level surface, engage the parking brake, and lower the loader arms.
-
Shut off the engine and remove the key.
-
Raise the loader arms and install the cylinder locks.
-
Remove the front cover; refer to Removing the Front Cover.
-
Place a drain pan under the front filter and replace the filter (Figure 80).
-
Clean up any spilled fluid.
-
Open the rear access cover; refer to Opening the Rear-Access Cover
-
Remove the rear screen; refer to Removing the Rear Screen.
-
Place a drain pan under the rear filter and replace the filter (Figure 81).
-
Clean up any spilled fluid.
-
Start the engine and let it run for about 2 minutes to purge air from the system.
-
Shut off the engine and check for leaks.
-
Check the fluid level in the hydraulic tank; refer toChecking the Hydraulic-Fluid Level and add fluid to raise the level to mark on dipstick.
Important: Do not overfill the tank.
-
Install the front cover.
-
Install the rear screen and tighten the knobs and bolts to secure it.
-
Close the rear-access cover and install the fastener to secure it.
-
Remove and store the cylinder locks and lower the loader arms.
Changing the Hydraulic Fluid
-
Park the machine on a level surface.
-
Raise the loader arms and install the cylinder locks.
-
Shut off the engine, remove the key, and allow the engine to cool.
-
Remove the front cover; refer to Removing the Front Cover.
-
Remove the hydraulic-tank cap and dipstick (Figure 82).
-
Place a large drain pain capable of holding 57 L (15 US gallons) under the drain plug on the front of the machine (Figure 83).
-
Remove the drain plug and allow the oil to drain into the pan (Figure 83).
-
When the oil is finished draining, install and tighten the drain plug.
Note: Dispose of the used oil at a certified recycling center.
-
Fill the hydraulic tank with hydraulic fluid; refer to Hydraulic-Fluid Specifications.
-
Start the engine and let it run for a few minutes.
-
Shut off the engine and remove the key.
-
Check the hydraulic-fluid level and add fluid to fill the tank if necessary; refer to Hydraulic-Fluid Specifications.
-
Install the front cover.
Loader Maintenance
Torquing the Loader Arm Adjustment Screws
Maintenance Service Interval | Maintenance Procedure |
---|---|
Every 25 hours |
|
Check the torque whenever the lower loader arms rattle.
-
Park the machine on a level surface.
-
Shut off the engine, remove the key, and allow the engine to cool.
-
On each loader arm, loosen the setscrew on the 4 adjustment screws (Figure 84).
-
Torque the adjustment screws to 27 N∙m (20 ft-lb).
-
Check that the length of the adjustment screws that is protruding from the arms is equal side to side.
-
Apply medium-strength thread-locking compound to the setscrews and tighten them until they just contact the adjustment screws.
Important: Do not overtighten the setscrews; otherwise you may damage the adjustment screw threads.
Cleaning
Removing Debris
Maintenance Service Interval | Maintenance Procedure |
---|---|
Before each use or daily |
|
Important: Operating the engine with blocked screens and/or cooling shrouds removed will result in engine damage from overheating.
-
Park the machine on a level surface and lower the loader arms.
-
Shut off the engine, remove the key, and allow the engine to cool.
-
Open the hood and secure the prop rod.
-
Clean any debris from the front and side screens.
-
Wipe away debris from the air cleaner.
-
Clean any debris buildup on the engine and in the oil cooler fins with a brush or blower.
Important: Operating the engine with blocked screens and/or cooling shrouds removed will result in engine damage due to overheating.
-
Clean debris from the hood opening, muffler, heat shields, and radiator screen (if applicable).
-
Close the hood.
Cleaning the Chassis
Maintenance Service Interval | Maintenance Procedure |
---|---|
Every 100 hours |
|
Over time, the chassis under the engine collects dirt and debris that must be removed. Using a flashlight, open the hood and inspect the area under the engine regularly. When the debris is 2.5 to 5 cm (1 to 2 inches) deep, clean the chassis.
-
Park the machine on a level surface and lower the loader arms.
-
Raise the front of the machine so that the machine is angled backward.
-
Shut off the engine and remove the key.
-
Remove the bottom plate; refer to Removing the Bottom Plate.
-
Remove the front cover assembly; refer to Removing the Front Cover Assembly.
-
Spray water into the chassis to clean out the dirt and debris.
Note: The water will drain at the back of the machine.
Important: Do not spray water into the engine.
-
Grease the machine; refer to Lubricating the Machine.
-
Install the bottom plate (Figure 42).
-
Install the front cover assembly.
-
Lower the machine.