Maintenance
Recommended Maintenance Schedule(s)
Maintenance Service Interval | Maintenance Procedure |
---|---|
After the first 2 hours |
|
After the first 5 hours |
|
Before each use or daily |
|
Every 100 hours |
|
Yearly |
|
Yearly or before storage |
|
Maintenance Safety
Read the following safety precautions before performing any maintenance on the machine:
-
Shut off the engine, remove the key, and wait for all movement to stop before you leave the operator’s position. Allow the machine to cool before adjusting, servicing, cleaning, or storing it.
-
Always wear eye protection while performing an adjustment or repair to protect your eyes from foreign objects that the machine may throw.
-
Check all fasteners at frequent intervals for proper tightness to ensure that the machine is in safe working condition.
-
Do not change the governor settings on the engine.
Purchase only genuine Toro replacement parts and accessories.
Preparing for Maintenance
-
Move the machine to a level surface.
-
Shut off the engine and wait for all moving parts to stop.
-
Disconnect the spark-plug wire. Refer to Replacing the Spark Plug.
Checking the Engine-Oil Level
Maintenance Service Interval | Maintenance Procedure |
---|---|
Before each use or daily |
|

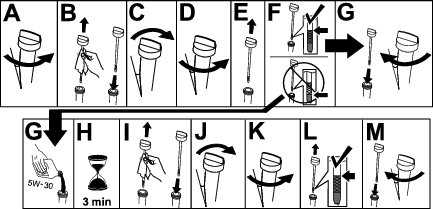
Checking and Adjusting the Skids and Scraper
Maintenance Service Interval | Maintenance Procedure |
---|---|
Yearly |
|
Check the skids and the scraper to ensure that the auger does not contact the paved or gravel surface. Adjust the skids and the scraper as needed to compensate for wear.
-
Check the tire pressure; refer to Checking the Tire Pressure.
-
Loosen the nuts that secure both skids to the auger sides until the skids slide up and down easily.
Important: The auger blades must be supported above the ground by the skids.
-
Ensure that the scraper is 3 mm (1/8 inch) above and parallel to a level surface.
Note: If the pavement is cracked, rough, or uneven, adjust the skids to raise the scraper. For gravel surfaces, adjust the skids further down to prevent the machine from picking up rocks.
-
Move the skids down until they are even with the ground.
-
Firmly tighten the nuts that secure both skids to the auger sides.
Note: To quickly adjust the skids if they loosen, support the scraper 3 mm (1/8 inch) off the pavement, then adjust the skids down to the pavement.
Note: If the skids become excessively worn, you can turn them over and set the unused side toward the pavement.
Checking and Adjusting the Traction Cable
Maintenance Service Interval | Maintenance Procedure |
---|---|
After the first 2 hours |
|
Yearly |
|
If the machine does not drive in the forward or reverse speeds or it drives when you release the traction lever, adjust the traction cable.
If the left (traction) cable is not properly adjusted, do the following steps:
-
Loosen the jam nut.
-
Engage the traction lever and hold it in place (Figure 26).
-
Loosen or tighten the turnbuckle to adjust the spring length to 5.5 cm (2–3/16 inches) as shown in Figure 27.
-
Tighten the jam nut (Figure 27), ensuring that there is slight tension on the cable.
-
If the traction cable is properly adjusted but a problem remains, contact an Authorized Service Dealer.
Checking and Adjusting the Auger/Impeller Cable
Maintenance Service Interval | Maintenance Procedure |
---|---|
After the first 2 hours |
|
Yearly |
|
-
Loosen the jam nut.
-
Engage the auger/impeller lever and hold it in place (Figure 28).
-
Loosen or tighten the turnbuckle to adjust the spring length to 7 cm (2-3/4 inches) as shown in Figure 29.
-
Tighten the jam nut (Figure 29), ensuring that there is slight tension on the cable.
-
If the auger/impeller cable is properly adjusted but a problem remains, contact an Authorized Service Dealer.
Checking the Auger-Gearbox-Oil Level
Maintenance Service Interval | Maintenance Procedure |
---|---|
Yearly |
|
-
Move the machine to a level surface.
-
Clean the area around the pipe plug (Figure 30).
-
Remove the pipe plug from the gearbox.
-
Check the oil level in the gearbox. The oil should be 9.5 mm (3/8 inch) below the filler opening.
-
If the oil level is low, add GL-5 or GL-6, SAE 80-90 EP gear oil lubricant to the gearbox until the oil level is 9.5 mm (3/8 inch) below the filler opening.
Note: Do not use synthetic oil.
-
Install the pipe plug in the gearbox.
Changing the Engine Oil
Maintenance Service Interval | Maintenance Procedure |
---|---|
After the first 5 hours |
|
Yearly |
|

If possible, run the engine for a few minutes before changing the oil because warm oil flows better and carries more contaminants.
Engine oil capacity | Model 38814: 0.6 L (20 fl oz)*, Model 38819: 0.7 L (24 fl oz)* |
Oil viscosity | Refer to Figure 32. |
API service classification | SJ or higher |
*There is residual oil in the crankcase after you drain the oil. Do not pour the entire capacity of oil into the crankcase. Fill the crankcase with oil as directed in the following steps.
Use Figure 32 below to select the best oil viscosity for the outdoor temperature range expected:
-
Move the machine to a level surface.
-
Clean the area around the oil-drain cap (Figure 31).
-
Slide an oil-drain pan under the drain extension and remove the oil-drain cap.
-
Drain the oil.
Note: Dispose of the used oil properly at a local recycling center.
-
Install the oil-drain cap and tighten it securely.
-
Clean around the oil fill/dipstick.
-
Unscrew the dipstick and remove it.
-
Carefully pour about 3/4 of the engine capacity of oil into the oil-fill tube.
Use Figure 32 to select the best oil viscosity for the outdoor temperature range expected:
-
Wait 3 minutes for the oil to settle in the engine.
-
Wipe the dipstick clean with a clean cloth.
-
Insert the dipstick into the oil-fill tube, screw it in, then remove the dipstick.
-
Read the oil level on the dipstick.
-
If the oil level on the dipstick is too low, carefully pour a small amount of oil into the oil-fill tube, wait 3 minutes, and repeat steps 10 through 12 until the oil level on the dipstick is correct.
-
If the oil level on the dipstick is too high, drain the excess oil until the oil level on the dipstick is correct.
Important: If the oil level in the engine is too low or too high and you run the engine, you may damage the engine.
-
-
Install the dipstick into the oil-fill tube securely.
Lubricating the Hex Shaft
Maintenance Service Interval | Maintenance Procedure |
---|---|
Yearly |
|
Lightly lubricate the hex shaft yearly with automotive engine oil (Figure 33).
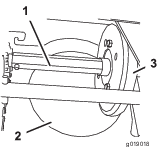
Important: Do not get oil on the rubber wheel or the steel friction pulley because the traction drive will slip (Figure 33).
-
Drain the fuel from the fuel tank.
-
Tip the machine forward onto its auger housing and block it so that it cannot fall.
-
Remove the back cover (Figure 34).
-
Move the speed-selector lever to Position R2.
-
Dip your finger in automotive engine oil and lightly lubricate the hex shaft.
-
Move the speed-selector lever to Position 6.
-
Lubricate the other end of the hex shaft.
-
Move the speed-selector lever forward and rearward a few times.
-
Install the back cover and return the machine to the operating position.
Replacing the Spark Plug
Maintenance Service Interval | Maintenance Procedure |
---|---|
Every 100 hours |
|
Warning
Replacing the spark plug while the engine is hot can result in burns.
Wait until the engine is cool to replace the spark plug.
Use a Toro spark plug or equivalent (Champion® RN9YC or NGK BPR6ES).
-
Remove the boot (Figure 35).
-
Clean around the base of the spark plug.
-
Remove and discard the old spark plug.
Note: You will need a ratchet wrench extension to remove the spark plug.
-
Set the gap between the electrodes on a new spark plug at 0.76 mm (0.030 inch) as shown in Figure 37.
-
Install the new spark plug, tighten it firmly, and attach the ignition wire to the spark plug.
Note: Ensure that the ignition wire snaps completely into place on the spark plug.
Adjusting the Discharge-Chute Latch
If the discharge chute does not lock into the desired position or does not unlock so that you can move it to another position, adjust the discharge-chute latch.
-
Loosen the clamp fastener on the chute-support plate until the cable is free.
-
Remove any slack in the cable by pulling the cable conduit rearward.
-
Tighten the clamp fastener while holding the cable in place.
Replacing the Drive Belts
If the auger/impeller drive belt or the traction-drive belt becomes worn, oil-soaked, or otherwise damaged, have an Authorized Service Dealer replace the belt.
Replacing the Headlight
Replace the headlight assembly (Toro part number 138-0670) when needed.
-
Remove the headlight wire from the back of the headlight (A of Figure 39).
-
Remove the bolt and nut holding the headlight assembly onto the headlight bracket and then remove the old headlight assembly (B of Figure 39).
-
Secure the new headlight assembly onto the headlight bracket with the previously removed nut and bolt (C of Figure 39).
-
Insert the headlight wire straight into the back of the headlight until it is securely in place (D of Figure 39).
