Maintenance
Note: Determine the left and right sides of the machine from the normal operating position.
Maintenance Safety
Caution
If you leave the key in the switch, someone could accidently start the machine and seriously injure you or other bystanders.
Remove the key from the switch before you perform any maintenance.
-
Park the machine on a level surface, disengage the auxiliary hydraulics, lower the attachment, ensure that the parking brake is engaged, shut off the machine, and remove the key. Wait for all movement to stop and allow the machine to cool before adjusting, cleaning, storing, or repairing it.
-
Do not allow untrained personnel to service the machine.
-
Use jack stands to support the components when required.
-
Carefully release pressure from components with stored energy; refer to Relieving Hydraulic Pressure.
-
Disconnect the battery before making any repairs; refer to Using the Battery-Disconnect Switch.
-
Keep your hands and feet away from the moving parts. If possible, do not make adjustments with the machine running.
-
Keep all parts in good working condition and all hardware tightened. Replace all worn or damaged decals.
-
Do not tamper with the safety devices.
-
Use only Toro-approved attachments. Attachments can change the stability and the operating characteristics of the machine. You may void the warranty if you use the machine with unapproved attachments.
-
Use only genuine Toro replacement parts.
-
If any maintenance or repair requires the loader arms to be in the raised position, secure the arms in the raised position with the hydraulic-cylinder lock(s).
Recommended Maintenance Schedule(s)
Maintenance Service Interval | Maintenance Procedure |
---|---|
After the first 8 hours |
|
After the first 50 hours |
|
Before each use or daily |
|
Every 25 hours |
|
Every 100 hours |
|
Every 400 hours |
|
Every 500 hours |
|
Yearly |
|
Yearly or before storage |
|
Pre-Maintenance Procedures
Using the Cylinder Locks
Warning
The loader arms may lower when in the raised position, crushing anyone under them.
Install the cylinder lock(s) before performing maintenance that requires raised loader arms.
Installing the Cylinder Locks
-
Remove the attachment.
-
Raise the loader arms to the fully raised position.
-
Shut off the machine and remove the key.
-
Position a cylinder lock over each lift-cylinder rod.
-
Secure each cylinder lock with 2 pins.
-
Slowly lower the loader arms until the cylinder locks contact the cylinder bodies and rod ends.
Removing and Storing the Cylinder Locks
Important: Remove the cylinder locks from the rods and fully secure them in the storage position before operating the machine.
-
Start the machine.
-
Raise the loader arms to the fully raised position.
-
Shut off the machine and remove the key.
-
Remove the pins securing each cylinder lock.
-
Remove the cylinder locks.
-
Place the cylinder locks on the posts on the sides of the machine and secure with the pins.
-
Lower the loader arms.
Accessing Internal Components
Warning
Opening or removing covers, hoods, and screens while the machine is running could allow you to contact moving parts, seriously injuring you.
Before opening any of the covers, hoods, and screens, shut off the machine, remove the key from the key switch, and allow the machine to cool.
Warning
The rotating fan can cause personal injury.
-
Do not operate the machine without guards in place.
-
Keep your fingers, hands, and clothing clear of the rotating fan.
-
Shut off the machine and remove the key before performing maintenance.
Removing the Hood
-
Park the machine on a level surface.
-
Shut off the machine, remove the key, and wait for moving parts to stop.
-
Remove the 4 bolts (3/8 x 1-1/2 inches) securing the hood.
-
Pull the hood off the machine.
Reverse the procedure to install the hood.
Removing the Lower Front Cover
-
Park the machine on a level surface.
-
Raise the loader arms and install the cylinder locks.
Note: If you cannot raise the loader arms using the machine power, pull the loader-arm lever rearward and use a hoist to lift the loader arms at their lift points.
-
Shut off the machine, remove the key, and wait for moving parts to stop.
-
Remove the hood.
-
Remove the 2 bolts (3/8 x 1 inch) securing the cover.
-
Remove the cover.
Reverse the procedure to install the cover.
Lubrication
Greasing the Machine
Maintenance Service Interval | Maintenance Procedure |
---|---|
Before each use or daily |
|
Grease Type: General-purpose grease
-
Park the machine on a level surface and lower the loader arms.
-
Shut off the machine and remove the key.
-
Clean the grease fittings with a rag.
-
Connect a grease gun to each fitting.
-
Pump grease into the fittings until grease begins to ooze out of the bearings (approximately 3 pumps).
-
Wipe up any excess grease.
Electrical System Maintenance
Electrical System Safety
-
Disconnect the battery before making any repairs; refer to Using the Battery-Disconnect Switch.
-
Charge the battery in an open, well-ventilated area, away from sparks and flames. Unplug the charger before connecting or disconnecting the battery. Wear protective clothing and use insulated tools.
Using the Battery-Disconnect Switch
-
Park the machine on a level surface and lower the loader arms.
-
Shut off the machine and remove the key.
-
Push the button on the latch and open the hood cover.
-
Turn the battery-disconnect switch to the ON or OFF position to perform the following:
-
To energize the machine electrically, rotate the battery-disconnect switch clockwise to the ON position.
-
To de-energize the machine electrically, rotate the battery-disconnect switch counterclockwise to the OFF position.
-
-
Close the cover and push the latch down.
Replacing the Static Strap
Maintenance Service Interval | Maintenance Procedure |
---|---|
Before each use or daily |
|
-
Park the machine on a level surface and lower the loader arms.
-
Shut off the machine and remove the key.
-
Under the platform, replace the static strap as shown.
Servicing the Batteries
Note: The machine is equipped with 6 lithium-ion batteries.
A lithium-ion battery must be disposed of or recycled in accordance with local and federal regulations. If a battery requires service, contact your Authorized Service Dealer for assistance.
Do not open the battery. If you are having problems with a battery, contact your Authorized Service Dealer for assistance.
Maintaining the Lithium-Ion Batteries
Warning
The batteries contain high voltage, which could burn or shock you.
-
Do not attempt to open the batteries.
-
Use extreme care when handling a battery with a cracked case.
-
Use only the charger designed for the batteries.
The lithium-ion batteries hold a sufficient charge to perform intended work during its life span.
To achieve maximum life and use from your batteries, follow these guidelines:
-
Do not open the battery.
-
Store/park the machine in a clean, dry garage or storage area, away from direct sunlight, heat sources, rain, and wet conditions. Do not store it in a location where the temperature exceeds the range specified in Battery Storage Requirements.
Important: Temperatures outside of this range will damage your batteries. High temperatures during storage, especially at a high state of charge, reduces the life of the batteries.
-
When storing the machine for more than 10 days, ensure that the machine is in a cool and dry location, out of sunlight, rain, and wet conditions.
-
If you are using the machine hot conditions or in strong, direct sunlight, the battery may overheat. If this happens, a high-temperature alert appears on the InfoCenter and machine functionality may be reduced.
Immediately drive the machine to a cool location out of the sun, turn off the machine, and allow the batteries to cool fully before resuming operation. If the batteries continue to overheat, another alert appears on the InfoCenter and the machine will shut off.
-
Use lights only when it is necessary.
Maintaining the Battery Charger
Important: All electrical repairs should be performed by an Authorized Service Dealer only.
The operator can perform very little maintenance other than protecting the charger from damage and weather.
-
Clean the charger cord with a slightly damp cloth after each use.
-
Coil the cord and place it into the storage compartment when not in use.
-
Periodically examine the cord for damage, and replace them when necessary with Toro-approved parts.
Servicing the Fuses
-
Park the machine on a level surface.
-
Shut off the machine and remove the key.
-
Remove the hood; refer to Removing the Hood.
-
Turn the battery-disconnect switch to the OFF position.
-
Test or replace the fuses as described in the Service Manual for the machine.
-
Turn the battery-disconnect switch to the ON position.
-
Install the hood.
Drive System Maintenance
Checking the Tire Treads
Maintenance Service Interval | Maintenance Procedure |
---|---|
Before each use or daily |
|
Check the tire treads for wear. Replace the tires when the treads are worn and shallow.
Checking the Wheel-Lug Nuts
Maintenance Service Interval | Maintenance Procedure |
---|---|
After the first 8 hours |
|
Every 100 hours |
|
Check and torque the wheel lug nuts 61 to 75 N∙m (45 to 55 ft-lb).
Drive-Motor Gear Oil Specifications
Oil type: Mobil 626 SHC
Capacity: 0.31 L (10.5 fl oz) per gearbox
Changing the Drive-Motor Gear Oil
Maintenance Service Interval | Maintenance Procedure |
---|---|
After the first 50 hours |
|
Every 500 hours |
|
-
Start the machine and drive it for 5 minutes.
Note: This warms the gear oil so that it drains better.
-
Park the machine on a level surface so that a drain plug on the motor is in the 6 o’clock position.
-
Shut off the machine and remove the key.
-
Raise the machine off the ground so that the wheels are off the ground. Support the machine using jack stands.
Note: Use jack stands rated for your machine. Refer to the Specifications for the weight.
Warning
Mechanical or hydraulic jacks may fail to support the machine and cause serious injury.
Use jack stands when supporting the machine.
-
Remove the rear wheels.
-
Place a drain pan under the drive motor.
-
Remove both plugs and allow the gear oil to drain.
-
Install the lower plug.
-
Fill the drive motor with gear oil through the open hole until the oil is up to the bottom of the hole.
Note: You may not need the full capacity amount due to residual oil in the motor.
-
Install the plug.
-
Repeat the procedure for the other drive motors.
-
Start the machine and engage the traction control it for a few minutes.
-
Stop the machine so that a drain plug on each motor is in the 3 o’clock position, shut off the machine, and remove the key.
-
Remove the plug in the 3 o’clock position, and verify that the oil level is at the bottom of the hole. Add oil as needed.
-
Install the plug and torque all plugs to 5 to 6 N∙m (50 to 60 in-lb).
-
Install the tires and torque the lug nuts 61 to 75 N∙m (45 to 55 ft-lb).
-
Lower the machine to the ground.
Controls System Maintenance
Adjusting the Controls
The factory adjusts the controls before shipping the machine. However, after many hours of use, you may need to adjust the traction control alignment, the NEUTRAL position of the traction control, and the tracking of the traction control in the full forward position.
Contact your Authorized Service Dealer to adjust the controls of your machine.
Hydraulic System Maintenance
Hydraulic System Safety
-
Seek immediate medical attention if fluid is injected into skin. Injected fluid must be surgically removed within a few hours by a doctor.
-
Ensure that all hydraulic-fluid hoses and lines are in good condition and all hydraulic connections and fittings are tight before applying pressure to the hydraulic system.
-
Keep your body and hands away from pinhole leaks or nozzles that eject high-pressure hydraulic fluid.
-
Use cardboard or paper to find hydraulic leaks.
-
Safely relieve all pressure in the hydraulic system before performing any work on the hydraulic system.
Relieving Hydraulic Pressure
To relieve hydraulic pressure while the machine is on, disengage the auxiliary hydraulics and fully lower the loader arms. Turn the key switch to the AUXILIARY HYDRAULIC RELIEF position and press the auxiliary-hydraulic switch back and forth.
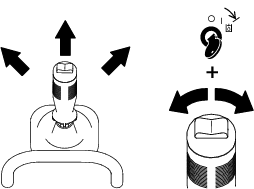
To relieve the pressure on the loader arms and attachment plate while the machine is off, cycle the joystick between the forward positions to lower the loader arms.
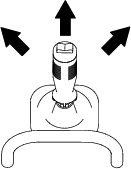
Hydraulic Fluid Specifications
Maintenance Service Interval | Maintenance Procedure |
---|---|
Every 25 hours |
|
Hydraulic Tank Capacity: 22.7 L (6 US gallons)
Recommended hydraulic fluid: Toro PX Extended Life Hydraulic Fluid
Note: A machine using the recommended replacement fluid requires less frequent fluid and filter changes.
Alternative hydraulic fluids: If Toro PX Extended Life Hydraulic Fluid is not available, you may use another conventional, petroleum-based hydraulic fluid having specifications that fall within the listed range for all the following material properties and that it meets industry standards. Do not use synthetic fluid. Consult with your lubricant distributor to identify a satisfactory product.
Note: Toro does not assume responsibility for damage caused by improper substitutions, so use products only from reputable manufacturers who will stand behind their recommendation.
Material Properties: | ||
Viscosity, ASTM D445 | cSt @ 40°C (104°F) 44 to 48 | |
Viscosity Index ASTM D2270 | 140 or higher | |
Pour Point, ASTM D97 | -37°C to -45°C (-34°F to -49°F) | |
Industry Specifications: | Eaton Vickers 694 (I-286-S, M-2950-S/35VQ25 or M-2952-S) |
Note: Many hydraulic fluids are almost colorless, making it difficult to spot leaks. A red dye additive for the hydraulic fluid is available in 20 ml (0.67 fl oz) bottles. A bottle is sufficient for 15 to 22 L (4 to 6 US gallons) of hydraulic fluid. Order Part No. 44-2500 from your Authorized Service Dealer.
Checking the Hydraulic-Fluid Level
Maintenance Service Interval | Maintenance Procedure |
---|---|
Every 25 hours |
|
Check the hydraulic-fluid level before the machine is first started and after every 25 operating hours.
Refer to Hydraulic Fluid Specifications.
Important: Always use the correct hydraulic fluid. Unspecified fluids will damage the hydraulic system.
-
Park the machine on a level surface, remove any attachment, raise the loader arms, and install the cylinder locks.
-
Shut off the machine, remove the key, and allow the machine to cool.
-
Remove the hood and lower front cover.
-
Remove the fan shroud.
-
Clean the area around the filler neck of the hydraulic tank.
-
Remove the filler-neck cap and check the fluid level on the dipstick.
The fluid level should be between the marks on the dipstick.
-
If the level is low, add enough fluid to raise it to the proper level.
-
Install the filler-neck cap.
-
Install the fan shroud.
-
Install the lower front cover and hood.
-
Remove and store the cylinder locks and lower the loader arms.
Replacing the Hydraulic Filter
Maintenance Service Interval | Maintenance Procedure |
---|---|
After the first 8 hours |
|
Every 400 hours |
|
Important: Do not substitute an automotive oil filter; otherwise, severe hydraulic system damage may result.
-
Park the machine on a level surface and lower the loader arms.
-
Shut off the machine and remove the key.
-
Remove the hood and lower front cover.
-
Place a drain pan under the filter.
-
Remove the old filter (Figure 41) and wipe the surface of the filter adapter clean.
-
Apply a thin coat hydraulic fluid to the rubber gasket on the replacement filter (Figure 41).
-
Install the replacement hydraulic filter onto the filter adapter (Figure 41). Tighten it clockwise until the rubber gasket contacts the filter adapter, then tighten the filter an additional 1/2 turn.
-
Clean up any spilled fluid.
-
Start the machine and let it run for about 2 minutes to purge air from the system.
-
Shut off the machine and check for leaks.
-
Check the fluid level in the hydraulic tank; refer to Checking the Hydraulic-Fluid Level. Add fluid to raise the level to mark on dipstick. Do not overfill the tank.
-
Install the lower front cover and hood.
Changing the Hydraulic Fluid
Maintenance Service Interval | Maintenance Procedure |
---|---|
Yearly |
|
-
Park the machine on a level surface, remove any attachment, raise the loader arms, and install the cylinder locks.
-
Shut off the machine and remove the key.
-
Remove the hood and lower front cover.
-
Remove the fan shroud.
-
Place a large drain pan under the machine that can hold the fluid capacity listed in Hydraulic Fluid Specifications.
-
Remove the drain plug from the bottom of the hydraulic tank and allow the fluid to completely drain (Figure 43).
-
Install the drain plug.
-
Fill the hydraulic tank with hydraulic fluid; refer to Hydraulic Fluid Specifications.
Note: Dispose of used fluid at a certified recycling center.
-
Install the fan shroud.
-
Install the lower front cover and the hood.
-
Remove and store the cylinder locks and lower the loader arms.
Cleaning
Removing Debris
Maintenance Service Interval | Maintenance Procedure |
---|---|
Before each use or daily |
|
Warning
Using compressed air improperly to clean the machine could result in serious injury.
-
Wear appropriate personal protective equipment, such as eye protection, hearing protection, and a dust mask.
-
Do not aim compressed air at any part of your body or at anyone else.
-
Refer to the manufacturer’s instructions for the air compressor for operating and safety information.
-
Park the machine on a level surface, remove any attachment, raise the loader arms, and install the cylinder locks.
-
Shut off the machine and remove the key.
-
Clean any debris from the machine.
Important: Blow the dirt out rather than wash it out. If you use water, keep it away from electrical items and hydraulic valves. Clean electrical connectors using compressed air; do not use contact cleaner.
-
Remove and store the cylinder locks and lower the loader arms.
Washing the Machine
If you must pressure wash the machine, do the following:
Important: Do not clean the machine with water while it is charging. Ensure machine is dry before charging.
-
Wear appropriate personal protective equipment for the pressure washer.
-
Keep all guards in place on the machine.
-
Avoid spraying at electronic components.
-
Avoid spraying at edges of decals.
-
Spray the exterior of the machine only. Do not spray directly into openings in the machine.
-
Spray only the dirty parts of the machine.
-
Use a 40-degree or larger spray nozzle. 40-degree nozzles are usually white.
-
Keep the tip of the pressure washer at least 61 cm (2 ft) away from the surface being washed.
-
Use only pressure washers with pressure below 13790 kpa (2000 psi) and flow below 7.6 L (2 US gallons) per minute.
-
Replace damaged or peeling decals.
-
Grease all grease points after washing; refer to Greasing the Machine.