Maintenance
Recommended Maintenance Schedule(s)
Maintenance Service Interval | Maintenance Procedure |
---|---|
After the first 2 hours |
|
After the first 10 hours |
|
After the first 20 hours |
|
Before each use or daily |
|
Every 100 hours |
|
Every 200 hours |
|
Every 800 hours |
|
Every 1,000 hours |
|
Every 2,000 hours |
|
Monthly |
|
Maintenance Safety
-
Before adjusting, cleaning, servicing, or leaving the machine, do the following:
-
Position the machine on a level surface.
-
Disengage the PTO.
-
Ensure that the traction unit is in neutral.
-
Engage the traction unit parking brake.
-
Shut off the engine of the traction unit and remove the key.
-
Wait for all moving parts to stop.
-
Allow machine components to cool before performing maintenance.
-
-
Perform only those maintenance instructions described in this manual. If major repairs are ever needed or assistance is desired, contact an authorized Toro distributor.
-
Ensure that the machine is in safe operating condition by keeping hardware tightened.
-
If possible, do not perform maintenance while the traction unit engine is running. Keep away from moving parts.
-
Do not check or adjust the belt tension when the traction unit engine is running.
-
Carefully release pressure from components with stored energy.
-
Support the machine with blocks whenever you raise it. Do not rely on a hydraulic system to support the machine.
-
Ensure that all guards are installed after maintaining or adjusting the machine.
Lubricating the Machine
Greasing the Fan Shaft Bearings
Greasing the Drive Shaft
Maintenance Service Interval | Maintenance Procedure |
---|---|
Every 100 hours |
|
Grease the 2 drive shaft fittings as illustrated in Figure 10 with No. 2 lithium grease.
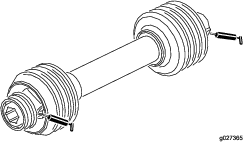
Checking the Tire Air Pressure
Maintenance Service Interval | Maintenance Procedure |
---|---|
Before each use or daily |
|
Important: Maintain the same air pressure in both tires to ensure proper machine performance. Do not under inflate the tires.
-
Check the air pressure in the tires.
You should measure 124 kPa (18 psi).
-
If the air pressure is too high or too low, adjust the air pressure until you measure 124 kPa (18 psi).
Checking the Torque of the Wheel Nuts
Maintenance Service Interval | Maintenance Procedure |
---|---|
After the first 2 hours |
|
After the first 10 hours |
|
Every 200 hours |
|
Warning
Failure to maintain the proper torque of the wheel nuts could result in failure or loss of the wheel and may result in personal injury.
Ensure that the wheel nuts are properly tightened before operating the machine.
Torque the wheel nuts to 115 to 136 N⋅m (85 to 100 ft-lb) in a crossing pattern (Figure 11).
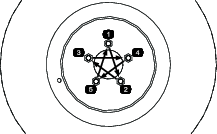
Hydraulic System Safety
-
Seek immediate medical attention if fluid is injected into skin. Injected fluid must be surgically removed within a few hours by a doctor.
-
Ensure that all hydraulic-fluid hoses and lines are in good condition and all hydraulic connections and fittings are tight before applying pressure to the hydraulic system.
-
Keep your body and hands away from pinhole leaks or nozzles that eject high-pressure hydraulic fluid.
-
Use cardboard or paper to find hydraulic leaks.
-
Before disconnecting or performing any work on the hydraulic system, lower the implement to the ground and shut off the engine to relieve all pressure in the system.
-
To ensure safe, optimal performance of the machine, use only genuine Toro replacement parts. Replacement parts made by other manufacturers could be dangerous, and such use could void the product warranty.
Checking the Hydraulic Lines and Hoses
Maintenance Service Interval | Maintenance Procedure |
---|---|
Before each use or daily |
|
Check the hydraulic lines and hoses for leaks, kinked lines, loose mounting supports, wear, loose fittings, weather, deterioration, and chemical deterioration. Make all necessary repairs before operating the machine.
Warning
Hydraulic fluid escaping under pressure can penetrate skin and cause injury.
-
Ensure that all hydraulic fluid hoses and lines are in good condition and all hydraulic connections and fittings are tight before applying pressure to the hydraulic system.
-
Keep body and hands away from pin-hole leaks or nozzles that eject high pressure hydraulic fluid.
-
Use cardboard or paper to find hydraulic leaks.
-
Safely relieve all pressure in the hydraulic system before performing any work on the hydraulic system.
-
Seek immediate medical attention if fluid is injected into skin.
Servicing the Hydraulic System
Hydraulic Fluid Specifications
The reservoir is filled at the factory with high-quality hydraulic fluid. Check the level of the hydraulic fluid before you first start the engine and daily thereafter; refer to Checking the Hydraulic Fluid Level.
Recommended replacement fluid: the manufacturer PX Extended Life Hydraulic Fluid; available in 19 L (5 US gallon) pails or 208 L (55 US gallon) drums.
Note: A machine using the recommended replacement fluid requires less frequent fluid and filter changes.
Alternative fluids: If the manufacturer PX Extended Life Hydraulic Fluid is not available, you may use another conventional, petroleum-based hydraulic fluid having specifications that fall within the listed range for all the following material properties and that it meets industry standards. Do not use synthetic fluid. Consult with your lubricant distributor to identify a satisfactory product.
Note: the manufacturer does not assume responsibility for damage caused by improper substitutions, so use products only from reputable manufacturers who will stand behind their recommendation.
Material Properties: | ||
Viscosity, ASTM D445 | cSt @ 40°C (104°F) 44 to 48 | |
Viscosity Index ASTM D2270 | 140 or higher | |
Pour Point, ASTM D97 | -37°C to -45°C (-34°F to -49°F) | |
Industry Specifications: | Eaton Vickers 694 (I-286-S, M-2950-S/35VQ25 or M-2952-S) |
Note: Many hydraulic fluids are almost colorless, making it difficult to spot leaks. A red dye additive for the hydraulic fluid is available in 20 ml (0.67 fl oz) bottles. A bottle is sufficient for 15 to 22 L (4 to 6 US gallons) of hydraulic fluid. Order Part No. 44-2500 from your authorized the manufacturer distributor.
Checking the Hydraulic Fluid Level
Maintenance Service Interval | Maintenance Procedure |
---|---|
Before each use or daily |
|
-
Operate the machine so that the fluid is warm, park the machine on a level surface, and shut off the engine.
-
Check the level of the fluid by viewing the sight gauge (Figure 12).
You should see the fluid level is in the middle of the sight gauge.
-
If the fluid level is below the middle of the gauge, remove the cap from the hydraulic fluid reservoir and slowly add the specified hydraulic fluid until the level reaches the middle (maximum) of the sight gauge; refer to Hydraulic Fluid Specifications.
Important: Do not over fill the reservoir; if you exceed the max fill line of the sight gauge you must remove the excess fluid; refer to Changing the Hydraulic Fluid.
Important: To prevent hydraulic system contamination, clean the top of the hydraulic-fluid containers opening it. Ensure that the pour spout and the funnel are clean.
-
Install the reservoir cap.
Changing the Hydraulic Fluid
Maintenance Service Interval | Maintenance Procedure |
---|---|
Every 800 hours |
|
Every 2,000 hours |
|
Reservoir capacity: approximately 38 L (10 US gallons)
Important: If the fluid becomes contaminated, contact an authorized the manufacturer distributor. Contaminated fluid looks milky or black when compared to clean fluid.
-
Turn the engine off.
-
Disconnect the small hydraulic hose (case drain) from the bottom of the reservoir and let the hydraulic fluid flow into a drain pan.
Note: Install and tighten the hose when the hydraulic fluid stops draining.
-
Fill the reservoir with approximately 38 L (10 US gallons) of the specified hydraulic fluid; refer to Hydraulic Fluid Specifications.
Important: Use only the hydraulic fluids specified. Other fluids could damage the system. To prevent over filling, do not fill if the fluid is cold. Do not over fill the reservoir with hydraulic fluid.
-
Install the reservoir cap.
-
Start the traction unit engine, use all the hydraulic controls to distribute the hydraulic fluid throughout the system, and check for leaks.
-
Shut off the engine
-
With the fluid warm, look into the sight gauge.
Note: If the hydraulic fluid level is low, add enough fluid to raise the level to the middle (maximum) of the sight gauge.
Replacing the Hydraulic Filter
Maintenance Service Interval | Maintenance Procedure |
---|---|
Every 800 hours |
|
Every 1,000 hours |
|
Use only the the manufacturer replacement filter in the hydraulic system; refer to the Parts Catalog.
Important: Use of any other filter may void the warranty on some components.
-
Turn the traction unit engine off and remove the key from the ignition.
-
Clean the area around the filter mounting area.
-
Place a drain pan under the filter and remove the filter (Figure 13).
-
Lubricate the new filter gasket and fill the filter with hydraulic fluid.
-
Ensure that the filter mounting area is clean.
-
Screw the filter on until the gasket contacts the mounting plate, then tighten the filter one–half turn.
-
Start the traction unit engine and operate the hydraulic controls to purge air from the system.
-
Shut off the engine and check the fluid level and for any leaks.
Adjusting the Impeller Belt
Maintenance Service Interval | Maintenance Procedure |
---|---|
After the first 20 hours |
|
Monthly |
|
Make sure that the belt is properly tensioned to ensure proper operation of the machine and prevent unnecessary wear.
-
Loosen the bolts and nuts securing the drive shield to the impeller housing (Figure 14) and remove the shield.
Note: You do not need to disconnect the drive shaft to adjust the belt tension.
-
On back side of the frame, loosen the bolt securing the belt tensioner to the frame (Figure 14).
-
Remove the bolt and nut securing the tensioner guide to the drive mount to release the belt tension (Figure 15).
-
Using a large wrench, rotate the tensioner clockwise until the decal is aligned with 15° on the tensioner tube.
Important: Align the tensioner as close to 15° as possible without going under.Rotating the tensioner too far over 15° can over-tension the belt, rotating it under 15° will leave the belt too loose; both can damage the machine.
-
Insert the bolt into the aligned guide holes and secure it with the nut.
Important: If the holes are not exactly aligned, rotate the guide to the next higher hole until it is aligned.
-
Tighten the bolt at the back side of the frame to lock the tensioner.
-
Install the drive shield to the impeller housing with the bolts and nuts removed previously.