Maintenance
Note: Determine the left and right sides of the machine from the normal operating position.
Maintenance Safety
Caution
If you leave the key in the switch, someone could accidently start the engine and seriously injure you or other bystanders.
Remove the key from the switch before you perform any maintenance.
-
Park the machine on a level surface, disengage the auxiliary hydraulics, lower the attachment, engage the parking brake (if equipped), shut off the engine, and remove the key. Wait for all movement to stop and allow the machine to cool before adjusting, cleaning, storing, or repairing it.
-
Clean up oil or fuel spills.
-
Do not allow untrained personnel to service the machine.
-
Use jack stands to support the components when required.
-
Carefully release pressure from components with stored energy; refer to Relieving Hydraulic Pressure.
-
Disconnect the battery before making any repairs; refer to Using the Battery-Disconnect Switch.
-
Keep your hands and feet away from the moving parts. If possible, do not make adjustments with the engine running.
-
Keep all parts in good working condition and all hardware tightened. Replace all worn or damaged decals.
-
Do not tamper with the safety devices.
-
Use only Toro-approved attachments. Attachments can change the stability and the operating characteristics of the machine. You may void the warranty if you use the machine with unapproved attachments.
-
Use only genuine Toro replacement parts.
-
If any maintenance or repair requires the loader arms to be in the raised position, secure the arms in the raised position with the hydraulic-cylinder lock(s).
Recommended Maintenance Schedule(s)
Maintenance Service Interval | Maintenance Procedure |
---|---|
After the first 8 hours |
|
After the first 50 hours |
|
Before each use or daily |
|
Every 25 hours |
|
Every 50 hours |
|
Every 100 hours |
|
Every 250 hours |
|
Every 400 hours |
|
Every 500 hours |
|
Every 600 hours |
|
Yearly or before storage |
|
Every 2 years |
|
Important: Refer to your engine owner’s manual for additional maintenance procedures.
Pre-Maintenance Procedures
Using the Cylinder Locks
Warning
The loader arms may lower when in the raised position, crushing anyone under them.
Install the cylinder lock(s) before performing maintenance that requires raised loader arms.
Installing the Cylinder Locks
-
Remove the attachment.
-
If needed, open the hood and secure the prop rod.
Note: You cannot open the hood after raising the loader arms.
-
Raise the loader arms to the fully raised position.
-
Shut off the engine and remove the key.
-
Remove the 2 pins securing the cylinder lock to the posts on the side of the machine.
-
Slide the cylinder lock over the lift-cylinder rod.
-
Repeat step 5 and 6 for the other side of the machine.
-
Slowly lower the loader arms until the cylinder locks contact the cylinder bodies and rod ends.
Removing and Storing the Cylinder Locks
Important: Remove the cylinder locks from the rods and fully secure them in the storage position before operating the machine.
-
Start the engine.
-
Raise the loader arms to the fully raised position.
-
Shut off the engine and remove the key.
-
Remove the pins securing the cylinder locks.
-
Place the cylinder locks on the posts on the sides of the machine and secure with the pins.
-
Lower the loader arms.
-
If the hood is open, close it.
Accessing Internal Components
Warning
Opening or removing covers, hoods, and screens while the engine is running could allow you to contact moving parts, seriously injuring you.
Before opening any of the covers, hoods, and screens, shut off the engine, remove the key from the key switch, and allow the engine to cool.
Opening the Hood
-
Use the latch key to unlock the lever.
-
Use the lever to lift open the hood
-
Secure the prop rod.
Closing the Hood
-
Lift up on the tab securing the prop rod.
-
Lower the hood and secure it by pushing down on the front of the hood until it locks in place.
-
Use the latch key to secure the latch.
Removing the Console Plate
-
Remove the 2 side cushions.
-
Remove the console plate.
-
Loosen the hose clamp on the hose and disconnect the hose from the air box.
Removing the Front Cover
-
Raise the loader arms and secure with the cylinder locks.
-
Remove the front cover.
Lubrication
Greasing the Machine
Maintenance Service Interval | Maintenance Procedure |
---|---|
Before each use or daily |
|
Grease Type: General-purpose grease.
-
Park the machine on a level surface, engage the parking brake, and lower the loader arms.
-
Shut off the engine and remove the key.
-
Clean the grease fittings with a rag.
-
Connect a grease gun to each fitting.
-
Pump grease into the fittings until grease begins to ooze out of the bearings (approximately 3 pumps).
-
Wipe up any excess grease.
Engine Maintenance
Engine Safety
-
Shut off the engine before checking the oil or adding oil to the crankcase.
-
Do not change the engine governor setting or overspeed the engine.
-
Keep your hands, feet, face, other body parts, and clothing away from the muffler and other hot surfaces.
Servicing the Air-Cleaner
Maintenance Service Interval | Maintenance Procedure |
---|---|
Before each use or daily |
|
Every 25 hours |
|
Every 600 hours |
|
Important: To prevent engine damage, always operate the engine with the air filter and cover installed.
Important: Replace the primary air-cleaner filter only when the service indicator shows red. Changing the air filter before it is necessary only increases the chance of dirt entering the engine when you remove the filter.
Servicing the Air-Cleaner Cover and Body
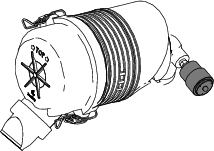
-
Park the machine on a level surface, engage the parking brake, and lower the loader arms.
-
Open the hood and secure the prop rod.
Note: You cannot open the hood after raising the loader arms.
-
Raise the loader arms enough to access the air cleaner cover and filters.
-
Shut off the engine and remove the key.
-
Check the air-cleaner body for damage that could cause an air leak. Check the whole intake system for leaks, damage, or loose hose clamps. Replace or repair any damaged components.
-
Release the latches on the air cleaner cover and pull the cover off.
Important: Do not remove the air filter.
-
Squeeze the dust cap sides to open it and knock the dust out.
-
Clean the inside of the cover with compressed air that is under 205 kPa (30 psi).
Important: Do not use compressed air on the air-cleaner body.
-
Check the service indicator.
-
If the service indicator is clear, install the cover with the dust cap oriented downward and secure the latches.
-
If the service indicator is red, replace the air filter.
-
Replacing the Filter(s)
-
Gently slide the primary filter out of the air-cleaner body.
Note: Avoid knocking the filter into the side of the body.
Important: Do not attempt to clean the filter.
-
If replacing the safety filter, gently slide the primary filter out of the air-cleaner body.
-
Inspect the new filter(s) for tears, an oily film, or damage to the rubber seal. Look into the filter while shining a bright light on the outside of the filter; holes in the filter appear as bright spots.
If the filter is damaged, do not use it.
-
Carefully install the filter(s).
Note: Ensure that each filter is fully seated by pushing on the outer rim of the filter while installing it.
Important: Do not press on the soft inside area of the filter.
-
Install the air-cleaner cover with the dust cap oriented downward as shown in Figure 41 and secure the latches.
-
Close the hood.
-
Lower the loader arms.
Servicing the Engine Oil
Maintenance Service Interval | Maintenance Procedure |
---|---|
Before each use or daily |
|
Every 250 hours |
|
Engine-Oil Specifications
The engine ships with oil in the crankcase; however, check the oil level before and after you first start the engine. Check the oil level before operating the machine each day or each time you use the machine.
Crankcase capacity: 3.4 L (3.6 qt) with the filter
Preferred engine oil: Toro Premium Engine Oil
If using an alternate oil, use high-quality, low-ash engine oil that meets or exceeds the following specifications:
-
API service category CJ-4 or higher
-
ACEA service category E6
-
JASO service category DH-2
Important: Using engine oil other than API classification CJ-4 or higher, ACEA E6, or JASO DH-2 may cause the diesel particulate filter to plug or cause engine damage.
Use the following engine oil viscosity grade:
-
SAE 10W-30 (all temperatures)
-
SAE 15W-40 (above 0° F)
Note: Toro Premium Engine oil is available from your Authorized Service Dealer.
Checking the Engine-Oil Level
-
Park the machine on a level surface, engage the parking brake, and lower the loader arms.
-
Open the hood and secure the prop rod.
Note: You cannot open the hood after raising the loader arms.
-
Raise the loader arms and secure them with the cylinder locks.
-
Shut off the engine, remove the key, and allow the engine to cool.
-
Check the oil and add additional oil as needed.
Important: Do not overfill the crankcase with oil; if the oil in the crankcase is too high and you run the engine, you may damage the engine.
-
Remove the cylinder locks and lower the loader arms.
-
Close the hood.
Changing the Engine Oil and Filter
-
Start the engine and let it run for 5 minutes.
Note: This warms the oil so that it drains better.
-
Park the machine on a level surface, engage the parking brake, and lower the loader arms.
-
Open the hood and secure the prop rod.
Note: You cannot open the hood after raising the loader arms.
-
Raise the loader arms and secure them with the cylinder locks.
-
Shut off the engine and remove the key.
-
Drain the oil beneath the platform.
Caution
Components will be hot if the machine has been running. If you touch hot components, you may be burned.
Use care to avoid touching hot components while changing the oil and/or filter.
-
Torque the drain plug to 46 to 56 N∙m (34 to 42 ft-lb).
-
Place a shallow pan or rag under the filter to catch oil.
-
Change the oil filter as shown.
-
Remove the oil-fill cap and slowly pour approximately 80% of the specified amount of oil in through the valve cover.
-
Check the oil level.
-
Slowly add additional oil to bring the level to the upper hole on the dipstick.
-
Replace the fill cap.
-
Remove the cylinder locks and lower the loader arms.
-
Close the hood.
Fuel System Maintenance
Danger
In certain conditions, fuel is extremely flammable and highly explosive. A fire or explosion from fuel can burn you and others and can damage property.
Refer to Fuel Safety for a complete list of fuel related precautions.
Draining the Water Separator
Maintenance Service Interval | Maintenance Procedure |
---|---|
Before each use or daily |
|
-
Park the machine on a level surface, engage the parking brake, and lower the loader arms.
-
Shut off the engine and remove the key.
-
Open the hood.
-
Place a clean container under the water separator.
-
Loosen the drain valve on the bottom of the filter canister and allow the water to drain.
-
When finished, tighten the drain valve.
-
Close the hood.
Replacing the Water Separator Filter
Maintenance Service Interval | Maintenance Procedure |
---|---|
Every 500 hours |
|
-
Park the machine on a level surface, engage the parking brake, and lower the loader arms.
-
Shut off the engine and remove the key.
-
Open the hood.
-
Clean the area where the filter canister mounts.
-
Remove the filter canister and clean the mounting surface.
-
Lubricate the gasket on the new filter canister with clean oil.
-
Fill the canister with fuel.
-
Install the filter canister by hand until the gasket contacts the mounting surface, then rotate it an additional 1/2 turn .
-
Close the hood.
Replacing the In-Line Fuel Filter
Maintenance Service Interval | Maintenance Procedure |
---|---|
Every 500 hours |
|
-
Park the machine on a level surface, engage the parking brake, and lower the loader arms.
-
Shut off the engine and remove the key.
-
Remove the console plate; refer to Removing the Console Plate.
-
Replace the filter as shown.
Note: Ensure that the markings on the filter follow the fuel flow direction.
Checking the Fuel Lines and Connections
Maintenance Service Interval | Maintenance Procedure |
---|---|
Every 400 hours |
|
Inspect the fuel lines and connections for deterioration, damage, or loose connections. Tighten any loose connections and contact your Authorized Service Dealer for assistance in fixing damaged fuel lines.
Bleeding the Fuel System
You must bleed the fuel system before starting the engine if any of the following situations have occurred:
-
Initial startup of a new machine
-
The engine has ceased running due to a lack of fuel.
-
Maintenance has been performed upon fuel-system components (e.g., filter replaced).
-
Turn the key to the RUN position.
-
Let the fuel pump run for 2 minutes prior to starting the machine.
Draining the Fuel Tank(s)
Maintenance Service Interval | Maintenance Procedure |
---|---|
Every 2 years |
|
Have an Authorized Service Dealer drain and clean the fuel tank(s).
Electrical System Maintenance
Electrical System Safety
-
Disconnect the battery before making any repairs; refer to Using the Battery-Disconnect Switch.
-
Charge the battery in an open, well-ventilated area, away from sparks and flames. Unplug the charger before connecting or disconnecting the battery. Wear protective clothing and use insulated tools.
-
Battery acid is poisonous and can cause burns. Avoid contact with skin, eyes, and clothing. Protect your face, eyes, and clothing when working with a battery.
-
Battery gases can explode. Keep cigarettes, sparks, and flames away from the battery.
Using the Battery-Disconnect Switch
-
Park the machine on a level surface, engage the parking brake, and lower the loader arms.
-
Shut off the engine and remove the key.
-
Open the hood.
-
Turn the battery-disconnect switch to the ON or OFF position.
Servicing the Battery
Maintenance Service Interval | Maintenance Procedure |
---|---|
Every 50 hours |
|
Removing the Battery
Warning
Incorrect battery cable routing could damage the machine and cables, causing sparks. Sparks can cause the battery gasses to explode, resulting in personal injury.
Always disconnect the negative (black) battery cable before disconnecting the positive (red) cable.
-
Park the machine on a level surface and engage the parking brake.
-
Raise the loader arms and secure them with the cylinder locks.
-
Shut off the engine and remove the key.
-
Disconnect the negative (black) ground cable from the battery post. Retain the fasteners.
-
Slide the rubber cover off the positive (red) cable.
-
Disconnect the positive (red) cable from the battery post. Retain the fasteners.
-
Remove the wing nuts, rods, and strap.
-
Remove the battery.
Charging the Battery
Warning
Charging the battery produces gasses that can explode.
Never smoke near the battery and keep sparks and flames away from battery.
Important: Always keep the battery fully charged (1.265 specific gravity). This is especially important to prevent battery damage when the temperature is below 0°C (32°F).
-
Remove the battery from the machine; refer to Removing the Battery.
-
Charge the battery for 4 to 8 hours at a rate of 3 to 4 A. Do not overcharge the battery.
-
When the battery is fully charged, unplug the charger from the electrical outlet, then disconnect the charger leads from the battery posts.
Cleaning the Battery
Note: Keep the terminals and the entire battery case clean, to help extend battery life.
-
Park the machine on a level surface, engage the parking brake (if equipped), and lower the loader arms.
-
Shut off the engine and remove the key.
-
Remove the battery from the machine; Removing the Battery.
-
Wash the entire case with a solution of baking soda and water.
-
Rinse the battery with clear water.
-
Coat the battery posts and cable connectors with Grafo 112X (skin-over) grease (Toro Part No. 505-47) or petroleum jelly to prevent corrosion.
-
Install the battery; refer to Installing the Battery.
Installing the Battery
Warning
Incorrect battery cable routing could damage the machine and cables, causing sparks. Sparks can cause the battery gasses to explode, resulting in personal injury.
Always connect the positive (red) battery cable before connecting the negative (black) cable.
-
Place the battery on the battery tray and secure it with the strap, wing nuts, and rods.
-
Using the fasteners previously removed, install the positive (red) battery cable to the positive (+) battery terminal.
-
Slide the red terminal boot onto the positive battery post.
-
Using the fasteners previously removed, install the negative (black) battery cable to the negative (-) battery terminal.
-
Close the hood.
Servicing a Replacement Battery
The original battery is maintenance-free and does not require service. For servicing a replacement battery, refer to the battery manufacturer’s instructions.
Jump-Starting the Machine
Warning
Jump-starting the battery can produce gasses that can explode.
Do not smoke near the battery, and keep sparks and flames away from battery.
-
Open the hood.
-
Check and clean corrosion from the battery terminals before jump-starting. Ensure that the connections are tight.
Caution
Corrosion or loose connections can cause unwanted electrical voltage spikes at any time during the jump-starting procedure.
Do not attempt to jump-start the machine with loose or corroded battery terminals, or damage to the engine may occur.
Danger
Jump-starting a weak battery that is cracked or frozen or has a low electrolyte level or an open/shorted battery cell can cause an explosion, resulting in serious personal injury.
Do not jump-start a weak battery if these conditions exist.
-
Make sure that the booster battery is a good and fully charged lead-acid battery at 12.6 V or greater.
Note: Use properly sized jumper cables with short lengths to reduce voltage drop between systems. Make sure that the cables are color coded or labeled for the correct polarity.
Warning
Batteries contain acid and produce explosive gases.
-
Shield your eyes and face from the batteries at all times.
-
Do not lean over the batteries.
Note: Ensure that the vent caps are tight and level. Place a damp cloth, if available, over any vent caps on both batteries. Also ensure that the machines do not touch and that both electrical systems are off and at the same rated system voltage. These instructions are for negative ground systems only.
-
-
Connect the positive (+) cable to the positive (+) terminal of the discharged battery that is wired to the starter or solenoid as shown.
-
Connect the other end of the positive (+) jumper cable to the positive terminal of the battery in the other machine.
-
Connect an end of the negative (-) jumper cable to the negative post of the battery in the other machine.
-
Connect the other end of the negative (-) jumper cable to a ground point, such as an unpainted bolt or chassis member.
-
Start the engine in the other machine. Let it run a few minutes, then start your engine.
-
Remove the cables in the reverse order of connection.
-
Close the hood.
Servicing the Fuses
The electrical system is protected by fuses. It requires no maintenance; however, if a fuse blows, check the component/circuit for a malfunction or a short.

1 | 2 | 3 | 4 | 5 | 6 | 7 | 8 | 9 | 10 | 11 | 12 | |
A | (Relay) | (Relay) | (Relay) | (Relay) | ||||||||
B | ||||||||||||
C | Key power | X | (Relay) | (Relay) | (Relay) | |||||||
(20 A) | ||||||||||||
D | Hour meter | X | ||||||||||
(10 A) | ||||||||||||
E | Power point/Light kit | System power | Auxiliary power | Telematics | Accessory power | Start circuit | ||||||
(15 A) | (20 A) | (10 A) | (10 A) | (10 A) | (15 A) |
Note: If the machine does not start, either the main circuit or the control panel/relay fuse could be blown.
Drive System Maintenance
Servicing the Tracks
Maintenance Service Interval | Maintenance Procedure |
---|---|
After the first 8 hours |
|
After the first 50 hours |
|
Before each use or daily |
|
Every 50 hours |
|
Cleaning the Tracks
-
Park the machine on a level surface and engage the parking brake.
-
With the bucket installed and angled downward, lower it into the ground so that the front of the traction unit lifts off the ground a few centimeters (inches).
-
Shut off the engine and remove the key.
-
Using a water hose or pressure washer, remove dirt from each track system.
Important: Ensure that you use high-pressure water to wash only the track area. Do not use a high-pressure washer to clean the rest of the traction unit. Do not use high pressure water between the drive sprocket and the traction unit or you may damage the motor seals. High-pressure washing can damage the electrical system and hydraulic valves or deplete grease.
Important: Ensure that you fully clean the road wheels, front wheel, rear wheel, and drive sprocket. The road wheels should rotate freely when clean.
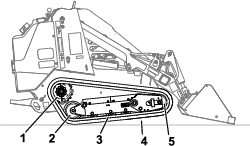
Checking and Adjusting the Track Tension
Lift/support 1 side of the machine and using the weight of the track, verify that the gap between the bottom of the lip of the road wheel and the track is 13 mm (1/2 inch). If it is not, adjust the track tension using the following procedure.
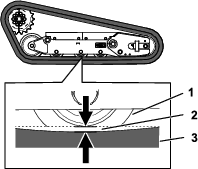
-
Park the machine on a level surface, engage the parking brake, and lower the loader arms.
-
Shut off the engine and remove the key.
-
Raise the side of the machine that you are adjusting so that the track is off the ground.
-
Loosen the bolts on the rear cover and remove the cover.
-
Loosen the jam nut and adjust the tensioning screw until the track deflection is 13 mm (1/2 inch).
-
Tighten the jam nut.
-
Install the cover and tighten the bolts.
-
Repeat the procedure for the other track.
-
Drive the machine, then park the machine on a level surface, engage the parking brake, shut off the engine, and remove the key.
-
Verify that the track deflection is 13 mm (1/2 inch). Adjust if necessary.
Replacing the Tracks
Removing the Tracks
-
Remove any attachments.
-
Park the machine on a level surface, ensuring that only 1 sprocket half is engaged with the track.
-
Lower the loader arms.
-
Shut off the engine and remove the key.
-
Raise the machine off the ground so that the bottom of the track is at least 10.2 cm (4 inches) off the ground. Support the machine using jack stands.
Note: Use jack stands rated for your machine.
Warning
Mechanical or hydraulic jacks may fail to support the machine and cause serious injury.
Use jack stands when supporting the machine.
-
Loosen the bolts on the rear cover and remove the cover.
-
Loosen the jam nut and turn the tensioning screw to release the tension.
-
Remove the segment of the drive sprocket not engaged with the track.
Important: If you do not remove the sprocket segment, it may be difficult to install a new track without damaging it.
-
Start the machine and disengage the parking brake.
-
Move the traction control forward until the other half of the drive sprocket is not engaged with the track
-
Shut off the engine and remove the key.
-
Remove the track from the track frame, drive hub, then front wheel.
Installing the Tracks
-
Wrap the new track around the front wheel.
-
Push the track under and between the road wheels and wrap it around the rear wheel.
-
Start the engine and disengage the parking brake.
-
Move the traction control forward until the drive sprocket half engages with the track.
-
Shut off the engine and remove the key.
-
Apply thread-locking compound to the bolts of the drive sprocket half that you removed and install the other sprocket half. Torque the bolts to 80 to 99 N∙m (59 to 73 ft-lb).
-
Adjust the tensioning screw until the track deflection is 19 mm (3/4 inch).
-
Tighten the jam nut.
-
Install the cover and tighten the bolts.
-
Repeat the procedure to replace the other track.
-
Lower the machine to the ground.
-
Drive the machine, then park the machine on a level surface, engage the parking brake, shut off the engine, and remove the key.
-
Verify that the track tension is correct; refer to Checking and Adjusting the Track Tension.
Cooling System Maintenance
Cooling System Safety
-
Swallowing engine coolant can cause poisoning; keep out of reach from children and pets.
-
Discharge of hot, pressurized coolant or touching a hot radiator and surrounding parts can cause severe burns.
-
Always allow the engine to cool at least 15 minutes before removing the radiator cap.
-
Use a rag when opening the radiator cap, and open the cap slowly to allow steam to escape.
-
Servicing the Cooling System
Maintenance Service Interval | Maintenance Procedure |
---|---|
Before each use or daily |
|
Every 100 hours |
|
Cleaning the Radiator Screen
Maintenance Service Interval | Maintenance Procedure |
---|---|
Before each use or daily |
|
Remove any buildup of grass, dirt or other debris from the radiator screen with compressed air.
Checking the Engine-Coolant Level
Maintenance Service Interval | Maintenance Procedure |
---|---|
Before each use or daily |
|
Capacity: 5 L (5.2 US qts)
Type: 50/50 solution of water and permanent ethylene-glycol antifreeze.
-
Park the machine on a level surface, engage the parking brake, and lower the loader arms.
-
Open the hood and secure the prop rod.
Note: You cannot open the hood after raising the loader arms.
-
Raise the loader arms and secure them with the cylinder locks.
-
Shut off the engine, remove the key, and allow the engine to cool.
-
Check the coolant level in the expansion tank.
Note: The coolant level should be at or above the mark on the side of the tank.
-
If the coolant level is low, remove the expansion tank cap and add a 50/50 mixture of water and permanent ethylene-glycol antifreeze.
Important: Do not overfill the expansion tank.
-
Install the expansion-tank cap.
-
Remove the cylinder locks and lower the loader arms.
-
Close the hood.
Changing the Engine Coolant
Maintenance Service Interval | Maintenance Procedure |
---|---|
Every 500 hours |
|
Have an Authorized Service Dealer change the engine coolant yearly.
If you need to add engine coolant, refer to Checking the Engine-Coolant Level.
Brake Maintenance
Testing the Parking Brake
Maintenance Service Interval | Maintenance Procedure |
---|---|
Before each use or daily |
|
-
Engage the parking-brake; refer to Parking-Brake Lever.
-
Start the engine.
-
Slowly attempt to drive the machine forward or rearward.
-
If the machine moves, contact your Authorized Service Dealer for service.
Belt Maintenance
Checking the Alternator-Belt Tension
Maintenance Service Interval | Maintenance Procedure |
---|---|
Before each use or daily |
|
Every 500 hours |
|
Proper tension of the belt allows 10 mm (3/8 inch) of deflection when a force of 10 kg (22 lb) is applied on the belt midway between the pulleys.
If the deflection is not 10 mm (3/8 inch), perform the following steps:
-
Loosen the alternator-mounting bolt.
-
Increase or decrease the alternator-belt tension and tighten the bolt.
-
Check the deflection of the belt again to ensure that the tension is correct.
Controls System Maintenance
Adjusting the Controls
The factory adjusts the controls before shipping the machine. However, after many hours of use, you may need to adjust the traction control alignment, the NEUTRAL position of the traction control, and the tracking of the traction control in the full forward position.
Contact your Authorized Service Dealer to adjust the controls of your machine.
Hydraulic System Maintenance
Hydraulic System Safety
-
Seek immediate medical attention if fluid is injected into skin. Injected fluid must be surgically removed within a few hours by a doctor.
-
Ensure that all hydraulic-fluid hoses and lines are in good condition and all hydraulic connections and fittings are tight before applying pressure to the hydraulic system.
-
Keep your body and hands away from pinhole leaks or nozzles that eject high-pressure hydraulic fluid.
-
Use cardboard or paper to find hydraulic leaks.
-
Safely relieve all pressure in the hydraulic system before performing any work on the hydraulic system.
Relieving Hydraulic Pressure
To relieve hydraulic pressure while the engine is on, disengage the auxiliary hydraulics and fully lower and retract the loader arms.
To relieve the pressure while the engine is off, cycle the loader arm/attachment-tilt lever between the forward positions to lower the loader arms.

Hydraulic Fluid Specifications
Maintenance Service Interval | Maintenance Procedure |
---|---|
Every 100 hours |
|
Hydraulic-System Capacity: 37.8 L (10 US gallons)
Recommended hydraulic fluid: Toro PX Extended Life Hydraulic Fluid
Note: A machine using the recommended replacement fluid requires less frequent fluid and filter changes.
Alternative hydraulic fluids: If Toro PX Extended Life Hydraulic Fluid is not available, you may use another conventional, petroleum-based hydraulic fluid having specifications that fall within the listed range for all the following material properties and that it meets industry standards. Do not use synthetic fluid. Consult with your lubricant distributor to identify a satisfactory product.
Note: Toro does not assume responsibility for damage caused by improper substitutions, so use products only from reputable manufacturers who will stand behind their recommendation.
Material Properties: | ||
Viscosity, ASTM D445 | cSt @ 40°C (104°F) 44 to 48 | |
Viscosity Index ASTM D2270 | 140 or higher | |
Pour Point, ASTM D97 | -37°C to -45°C (-34°F to -49°F) | |
Industry Specifications: | Eaton Vickers 694 (I-286-S, M-2950-S/35VQ25 or M-2952-S) |
Note: Many hydraulic fluids are almost colorless, making it difficult to spot leaks. A red dye additive for the hydraulic fluid is available in 20 ml (0.67 fl oz) bottles. A bottle is sufficient for 15 to 22 L (4 to 6 US gallons) of hydraulic fluid. Order Part No. 44-2500 from your Authorized Service Dealer.
Checking the Hydraulic-Fluid Level
Maintenance Service Interval | Maintenance Procedure |
---|---|
Every 25 hours |
|
Important: Always use the correct hydraulic fluid. Unspecified fluids will damage the hydraulic system. Refer to Hydraulic Fluid Specifications.
-
Remove any attachments.
-
Park the machine on a level surface and engage the parking brake.
-
Shut off the engine and remove the key.
-
Raise the bracket.
-
Clean the area around the filler cap .
-
Remove the filler-neck cap and check the fluid level on the dipstick.
Note: The fluid level should be within the marks on the dipstick.
-
If the level is low, add enough fluid to raise it to the proper level.
-
Install the filler cap.
-
Lower the bracket.
Replacing the Hydraulic Filter
Maintenance Service Interval | Maintenance Procedure |
---|---|
After the first 8 hours |
|
Every 250 hours |
|
Important: Do not substitute an automotive oil filter; otherwise, severe hydraulic system damage may result.
-
Park the machine on a level surface, engage the parking brake, and lower the loader arms.
-
Shut off the engine and remove the key.
-
Open the hood and secure the prop rod.
-
Place a drain pan under the filter and replace the filter as shown.
-
Clean up any spilled fluid.
-
Start the engine and let it run for about 2 minutes to purge air from the system.
-
Shut off the engine and check for leaks.
-
Check the fluid level in the hydraulic tank; refer toHydraulic Fluid Specifications and add fluid to raise the level to mark on dipstick.
Important: Do not overfill the tank.
-
Close the hood.
Changing the Hydraulic Fluid
Maintenance Service Interval | Maintenance Procedure |
---|---|
Every 500 hours |
|
-
Park the machine on a level surface, engage the parking brake, and lower the loader arms.
-
Shut off the engine and remove the key.
-
Place a large drain pain capable of holding 57 L (15 US gallons) under the drain plug on the hydraulic tank.
-
Remove the drain plug and allow the oil to drain into the pan.
-
When the oil is finished draining, install and tighten the drain plug.
Note: Dispose of the used oil at a certified recycling center.
-
Fill the hydraulic tank with hydraulic fluid; refer to Hydraulic Fluid Specifications.
-
Start the engine and let it run for a few minutes.
-
Shut off the engine and remove the key.
-
Check the hydraulic-fluid level and add fluid to fill the tank if necessary; refer to Checking the Hydraulic-Fluid Level.
Cleaning
Removing Debris
Maintenance Service Interval | Maintenance Procedure |
---|---|
Before each use or daily |
|
Important: Operating the engine with blocked screens and/or cooling shrouds removed will result in engine damage from overheating.
-
Park the machine on a level surface and lower the loader arms.
-
Shut off the engine, remove the key, and allow the engine to cool.
-
Open the hood and secure the prop rod.
-
Wipe away debris from the air cleaner.
-
Clean any debris buildup on the engine and in the oil cooler fins with a brush or blower.
Important: Operating the engine with blocked screens and/or cooling shrouds removed will result in engine damage due to overheating.
-
Clean debris from the hood opening, muffler, heat shields, and radiator screen (if applicable).
-
Close the hood.
Washing the Machine
When pressure washing the machine, do the following:
-
Wear appropriate personal protective equipment for the pressure washer.
-
Keep all guards in place on the machine.
-
Avoid spraying at electronic components.
-
Avoid spraying at edges of decals.
-
Spray the exterior of the machine only. Do not spray directly into openings in the machine.
-
Spray only the dirty parts of the machine.
-
Use a 40-degree or larger spray nozzle. 40-degree nozzles are usually white.
-
Keep the tip of the pressure washer at least 61 cm (2 ft) away from the surface being washed.
-
Use only pressure washers with pressure below 13790 kpa (2000 psi) and flow below 7.6 L (2 US gallons) per minute.
-
Replace damaged or peeling decals.
-
Grease all grease points after washing; refer to Greasing the Machine.
Cleaning the Chassis
Maintenance Service Interval | Maintenance Procedure |
---|---|
Every 100 hours |
|
Over time, the chassis under the engine collects dirt and debris that must be removed. Open the hood, secure the prop rod, and use a flashlight to inspect the area under the engine regularly. When the debris is 2.5 to 5 cm (1 to 2 inches) deep, clean the chassis.
-
Park the machine on a level surface, engage the parking brake, and lower the loader arms.
-
Raise the front of the machine so that the machine is angled backward.
-
Shut off the engine and remove the key.
-
Remove the 2 bolts securing the bottom plate and remove the bottom plate.
-
Remove the front cover; refer to Removing the Front Cover.
-
Spray water into the chassis to clean out the dirt and debris.
Note: The water will drain at the back of the machine.
Important: Do not spray water into the engine.
-
Grease the machine; refer to Greasing the Machine.
-
Install the bottom plate.
-
Install the front screen.
-
Lower the machine.