Maintenance
Note: Determine the left and right sides of the machine from the normal operating position.
Maintenance Safety
-
Park machine on level ground, disengage drives, set parking brake, stop engine, and remove key. Wait for all moving parts to stop before leaving the operator’s position. Allow the machine to cool before servicing, adjusting, fueling, cleaning, or storing.
-
If you leave the key in the switch, someone could accidently start the engine and seriously injure you or other bystanders. Remove the key from the switch before you perform any maintenance.
-
Never allow untrained personnel to service machine.
-
Disconnect battery before making any repairs. Disconnect the negative terminal first and the positive last. Reconnect positive first and negative last.
-
Keep all guards, shields, switches, and all safety devices in place and in proper working condition. Frequently check for worn or deteriorating components and replace them with genuine Exmark parts when necessary.
Warning
Removal or modification of original equipment, parts and/or accessories may alter the warranty, controllability, and safety of the machine. Unauthorized modifications to the original equipment or failure to use original Exmark parts could lead to serious injury or death. Unauthorized changes to the machine, engine, fuel or venting system, may violate applicable safety standards such as: ANSI, OSHA and NFPA and/or government regulations such as EPA and CARB.
Warning
Hydraulic fluid escaping under pressure can penetrate skin and cause injury. Fluid accidentally injected into the skin must be surgically removed within a few hours by a doctor familiar with this form of injury or gangrene may result.
-
If equipped, make sure all hydraulic fluid hoses and lines are in good condition and all hydraulic connections and fittings are tight before applying pressure to hydraulic system.
-
Keep body and hands away from pinhole leaks or nozzles that eject high pressure hydraulic fluid.
-
Use cardboard or paper, not your hands, to find hydraulic leaks.
-
Safely relieve all pressure in the hydraulic system by placing the motion control levers in neutral and shutting off the engine before performing any work on the hydraulic system.
Warning
Fuel system components are under high pressure. The use of improper components can result in system failure, fuel leakage and possible explosion.
Use only approved fuel lines and fuel filters for high pressure systems.
-
-
Use care when checking blades. Wrap the blade(s) or wear gloves, and use caution when servicing them. Only replace damaged blades. Never straighten or weld them.
-
Do not rely solely on mechanical or hydraulic jacks for support. Use adequate jack stands.
-
Carefully release pressure from components with stored energy
-
Keep your hands and feet away from moving parts or hot surfaces. If possible, do not make adjustments with the engine running.
-
Keep all parts in good working condition and all hardware tightened, especially the blade-attachment hardware.
Recommended Maintenance Schedule(s)
Maintenance Service Interval | Maintenance Procedure |
---|---|
After the first 50 hours |
|
After the first 100 hours |
|
After the first 200 hours |
|
Before each use or daily |
|
Every 50 hours |
|
Every 200 hours |
|
Every 400 hours |
|
Every 800 hours |
|
Every 2,000 hours |
|
Monthly |
|
Yearly |
|
Periodic Maintenance
Engine Maintenance
Important: Refer to the Engine Owner’s Manual for additional maintenance procedures.
Engine Safety
Warning
The engine can become very hot, especially the muffler and exhaust components. Touching a hot engine can cause severe burns.
Allow the engine to cool completely before service or making repairs around the engine area.
Do Not change the engine governor setting or overspeed the engine.
Check Engine Oil Level
Maintenance Service Interval | Maintenance Procedure |
---|---|
Before each use or daily |
|
-
Stop engine and wait for all moving parts to stop. Make sure unit is on a level surface.
-
Check with engine cold.
-
Raise hood to gain access to dipstick.
-
Clean area around dipstick. Remove dipstick and wipe oil off. Reinsert the dipstick and push it all the way down into the tube. Remove the dipstick and read the oil level.
-
If the oil level is low, wipe off the area around the oil fill cap, remove cap and fill to the “FULL” mark on the dipstick. Exmark 4-Cycle Premium Engine Oil is recommended; refer to the Engine Owner's manual for an appropriate API rating and viscosity. Do Not overfill.
Important: Do Not operate the engine with the oil level below the “LOW” (or “ADD”) mark on the dipstick, or over the “FULL” mark.
Check Battery Charge
Maintenance Service Interval | Maintenance Procedure |
---|---|
Monthly |
|
Allowing batteries to stand for an extended period of time without recharging them will result in reduced performance and service life. To preserve optimum battery performance and life, recharge batteries in storage when the open circuit voltage drops to 12.4 volts.
Note: To prevent damage due to freezing, battery should be fully charged before putting away for winter storage.
Danger
Charging or jump starting the battery may produce explosive gases. Battery gases can explode causing serious injury.
-
Keep sparks, flames, or cigarettes away from battery.
-
Ventilate when charging or using battery in an enclosed space.
-
Make sure venting path of battery is always open once battery is filled with acid.
-
Always shield eyes and face from battery.
Danger
Battery electrolyte contains sulfuric acid, which is poisonous and can cause severe burns. Swallowing electrolyte can be fatal or if it touches skin can cause severe burns.
-
Wear safety glasses to shield eyes, and rubber gloves to protect skin and clothing when handling electrolyte.
-
Do Not swallow electrolyte.
-
In the event of an accident, flush with water and call a doctor immediately.
Caution
If the ignition is in the “ON” position there is potential for sparks and engagement of components. Sparks could cause an explosion or moving parts could accidentally engage causing personal injury.
Be sure ignition switch is in the “OFF” position before charging the battery.
Check the voltage of the battery with a digital voltmeter. Locate the voltage reading of the battery in the table and charge the battery for the recommended time interval to bring the charge up to a full charge of 12.6 volts or greater.
Important: Make sure the negative battery cable is disconnected and the battery charger used for charging the battery has an output of 16 volts and 7 amps or less to avoid damaging the battery (see chart for recommended charger settings).
Voltage Reading | Percent Charge | Maximum Charger Settings | Charging Interval |
---|---|---|---|
12.6 or greater | 100% | 16 volts/7 amps | No Charging Required |
12.4 – 12.6 | 75–100% | 16 volts/7 amps | 30 Minutes |
12.2 – 12.4 | 50–75% | 16 volts/7 amps | 1 Hour |
12.0–12.2 | 25–50% | 14.4 volts/4 amps | 2 Hours |
11.7–12.0 | 0–25% | 14.4 volts/4 amps | 3 Hours |
11.7 or less | 0% | 14.4 volts/2 amps | 6 Hours or More |
Recommended Jump Starting Procedure
-
Check the weak battery for terminal corrosion (white, green, or blue “snow”), it must be cleaned off prior to jump starting. Clean and tighten connections as necessary.
Caution
Corrosion or loose connections can cause unwanted electrical voltage spikes at anytime during the jump starting procedure.
Do Not attempt to jump start with loose or corroded battery terminals or damage to the engine may occur.
Danger
Jump starting a weak battery that is cracked, frozen, has low electrolyte level, or an open/shorted battery cell, can cause an explosion resulting in serious personal injury.
Do Not jump start a weak battery if these conditions exist.
-
Make sure the booster is a good and fully charged lead acid battery at 12.6 volts or greater. Use properly sized jumper cables (4 to 6 AWG) with short lengths to reduce voltage drop between systems. Make sure the cables are color coded or labeled for the correct polarity.
Caution
Connecting the jumper cables incorrectly (wrong polarity) can immediately damage the electrical system.
Be certain of battery terminal polarity and jumper cable polarity when hooking up batteries.
Note: The following instructions are adapted from the SAE J1494 Rev. Dec. 2001 – Battery Booster Cables – Surface Vehicle Recommended Practice (SAE – Society of Automotive Engineers).
Warning
Batteries contain acid and produce explosive gases.
-
Shield the eyes and face from the batteries at all times.
-
Do Not lean over the batteries.
Note: Be sure the vent caps are tight and level. Place a damp cloth, if available, over any vent caps on both batteries. Be sure the vehicles do not touch and that both electrical systems are off and at the same rated system voltage. These instructions are for negative ground systems only.
-
-
Connect the positive (+) cable to the positive (+) terminal of the discharged battery that is wired to the starter or solenoid as shown in .
-
Connect the other end of the positive cable to the positive terminal of the booster battery.
-
Connect the black negative (–) cable to the other terminal (negative) of the booster battery.
-
MAKE THE FINAL CONNECTION ON THE ENGINE BLOCK OF THE STALLED VEHICLE (NOT TO THE NEGATIVE POST) AWAY FROM THE BATTERY. STAND BACK.
-
Start the vehicle and remove the cables in the reverse order of connection (the engine block (black) connection is the first to disconnect).
Check Mower Blades
Maintenance Service Interval | Maintenance Procedure |
---|---|
Before each use or daily |
|
-
Stop engine, wait for all moving parts to stop, and remove key. Engage parking brake.
-
Lift deck and secure in raised position as stated in the Clean Grass Build-Up Under Deck procedure.
-
Inspect blades and sharpen or replace as required.
-
Reinstall the blades (if they were removed) in the following order:
-
Install bushing through blade with bushing flange on bottom (grass) side of blade.
-
Install bushing/blade assembly into spindle.
-
Apply lubricant to threads of blade bolt as needed to prevent seizing. Copper-based anti-seize preferable. Grease acceptable substitute. Install blade bolt finger tight. Place wrench on the top spindle nut then torque the blade bolts to 55-60 ft-lb (75-81 N-m).
Important: On rear discharge decks, the RH blade rotates counterclockwise. Be sure to reinstall that blade onto the RH spindle only.
Warning
Incorrect installation of the blade or components used to retain the blade can be dangerous. Failure to use all original components and assembled as shown could allow a blade or blade component to be thrown out from under the deck resulting in serious personal injury or death.
Always install the original Exmark blades, blade bushings, and blade bolts as shown.
-
Check Safety Interlock System
Maintenance Service Interval | Maintenance Procedure |
---|---|
Before each use or daily |
|
Important: It is essential that operator safety mechanisms be connected and in proper operating condition prior to use.
Note: If machine does not pass any of these tests, Do Not operate. Contact an Authorized Service Dealer.
Note: To prevent engine cut-outs on rough terrain, the seat has a 1/2 second time delay before the engine begins to shutdown.
Check the Normal Engine Starting Chart for All Except 144 Inch Deck Models
System | ||||||
Parking Brake | PTO | Motion Control Levers | Operator | Outcome | ||
State of System | Engaged | Disengaged (Blades) | Both levers out (neutral lock) | In seat or out of the seat | Starter should crank | |
![]() | ![]() | ![]() | ![]() ![]() | ![]() |
||
Engaged | Up position, but blades disengaged* | Both levers out (neutral lock) | In seat or out of seat | Starter should crank | ||
![]() | ![]() | ![]() | ![]() ![]() | ![]() |
*Note: The starter will crank with the PTO switch in the “ON” (pulled up) position; however, the system will disengage the PTO and a reset PTO error will occur. Engaging the PTO will require the operator to reset the PTO switch by turning it “OFF” (pushed down) and then turning it “ON”.
Check the Normal Engine Starting Chart for 144 Inch Deck Models
System | |||||
Motion Control Levers/Parking Brake | PTO | Operator | Outcome | ||
State of System | Both Levers Out=Parking Brake Engaged | Disengaged (Blades) | In seat or out of the seat | Starter should crank | |
![]() ![]() | ![]() | ![]() ![]() | ![]() |
||
Both Levers Out=Parking Brake Engaged | Up position, but blades disengaged* | In seat or out of seat | Starter should crank | ||
![]() ![]() | ![]() | ![]() ![]() | ![]() |
*Note: The starter will crank with the PTO switch in the “ON” (pulled up) position; however, the system will disengage the PTO and a reset PTO error will occur. Engaging the PTO will require the operator to reset the PTO switch by turning it “OFF” (pushed down) and then turning it “ON”.
Check Engine Starting Circuit Chart for All Except 144 Inch Deck Models
Note: In the Check Engine Starting Circuit Chart, the state of system item that is bold is being checked in each scenario.
System | |||||
Parking Brake | PTO (Blades) | Motion Control Levers | Operator | Outcome | |
State of System | Engaged | Disengaged | Both levers moved in, or either right or left lever moved in | Operator in seat | Starter must not crank |
![]() | ![]() | ![]() ![]() ![]() | ![]() | ![]() |
|
Disengaged | Disengaged | Both levers out (neutral lock) | Operator in seat | Starter must not crank | |
![]() | ![]() | ![]() | ![]() | ![]() |
Check Engine Starting Circuit Chart for 144 Inch Deck Models
Note: In the Check Engine Starting Circuit Chart, the state of system item that is bold is being checked in each scenario.
System | ||||
Motion Control Levers/Parking Brake | PTO (Blades) | Operator | Outcome | |
State of System | Both levers moved in, or right or left lever moved in=Parking Brake Disengaged | Disengaged | Operator in seat | Starter must not crank |
![]() ![]() ![]() ![]() | ![]() | ![]() | ![]() |
Check Shutdown Circuit Chart for All Except 144 Inch Deck Models
Note: The state of system item(s) that is bold is being checked in each scenario.
System | ||||||
Engine | Parking Brake | PTO (Blades) | Motion Control Levers | Operator | Outcome | |
State of System | Running idle (1/3 throttle or efficient mode) | Disengaged | Disengaged | Both levers moved out (neutral lock) or both levers moved in | Raise off of seat (but don’t get off) | Engine must begin shutdown within 1 second |
![]() | ![]() | ![]() | ![]() ![]() | ![]() | ![]() |
|
Check Shutdown Circuit Chart (continued) | ||||||
System | ||||||
Engine | Parking Brake | PTO (Blades) | Motion Control Levers | Operator | Outcome | |
State of System | Running idle (1/3 throttle or efficient mode) | Disengaged | Engaged | Both levers moved in | Raise off of seat (but don’t get off) | Engine must begin shutdown within 1 second |
![]() | ![]() | ![]() | ![]() | ![]() | ![]() |
|
Running idle (1/3 throttle or efficient mode) | Engaged | Disengaged | Both levers moved in, or either right or left lever moved in | Operator in seat | Engine must begin shutdown within 1 second | |
![]() | ![]() | ![]() | ![]() ![]() ![]() | ![]() | ![]() |
|
Running idle (1/3 throttle or efficient mode) | Engaged | Engaged | Both levers moved out (neutral lock) | Raise off of seat (but don’t get off) | PTO must begin shutdown within 1 second; engine stays running. | |
![]() | ![]() | ![]() | ![]() | ![]() | ![]() |
|
Running idle (1/3 throttle or efficient mode) | Disengaged | Engaged and Deck wings up | Both levers moved out (neutral lock) | Operator in seat | PTO must begin shutdown within 1 second; engine stays running. | |
![]() | ![]() | ![]() | ![]() | ![]() | ![]() |
Check Shutdown Circuit Chart for 144 Inch Deck Models
Note: The state of system item(s) that is bold is being checked in each scenario.
System | |||||
Engine | Motion Control Levers/Parking Brake | PTO (Blades) | Operator | Outcome | |
State of System | Running idle (1/3 throttle or efficient mode) | Both levers moved in, or right or left lever moved in=Parking Brake Disengaged | Disengaged | Raise off of seat (but don’t get off) | Engine must begin shutdown within 1 second |
![]() | ![]() ![]() ![]() ![]() | ![]() | ![]() | ![]() |
|
Running idle (1/3 throttle or efficient mode) | Both Levers Out=Parking Brake Engaged | Engaged | Raise off of seat (but don’t get off) | PTO must begin shutdown within 1 second; engine stays running. | |
![]() | ![]() ![]() | ![]() | ![]() | ![]() |
|
Check Shutdown Circuit Chart (continued) | |||||
System | |||||
Engine | Motion Control Levers/Parking Brake | PTO (Blades) | Operator | Outcome | |
State of System | Running idle (1/3 throttle or efficient mode) | Both levers moved in, or right or left lever moved in=Parking Brake Disengaged | Engaged and Deck wings up | Operator in seat | PTO must begin shutdown within 1 second; engine stays running. |
![]() | ![]() ![]() ![]() ![]() | ![]() | ![]() | ![]() |
Check Rollover Protections Systems (Roll Bar) Knobs
Maintenance Service Interval | Maintenance Procedure |
---|---|
Before each use or daily |
|
Check that both the mounting hardware and the knobs are in good working condition. Make sure the knobs are fully engaged with the ROPS in the raised position. The upper hoop of the roll bar may need to be pushed forward or pulled rearward to get both knobs fully engaged.
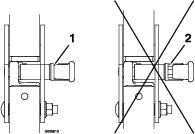
Check Wing Deck Bushings
Maintenance Service Interval | Maintenance Procedure |
---|---|
Every 400 hours |
|
-
Position the machine on a flat surface.
-
Shut off the engine, wait for all moving parts to stop, and engage the parking brake.
-
Raise the center deck and fold the wings by pressing down at the rear of the deck lift rocker switch. Hold the switch down until both wings are completely folded.
-
Push on the front corners of the deck near the lower bushings. If the there is more than 1/8 inch (3 mm) of movement, then the bushings need to be replaced.
Change Wing Deck Pivot Bushings
-
Position the mower on a flat surface.
-
Disengage the PTO and shut off the engine.
-
Remove and retain the clevis pins and hairpins from each wing deck storage location.
-
Be sure that all persons are clear of the deck wings. Press and hold the top of the deck control switch; the center deck will raise first and then the wings.
-
Secure each wing in the up position with the clevis pins and hairpins.
-
Loosen the bolts that secure the upper pivot pins to the deck but Do Not remove.
For 144 Inch Deck Models Only: Remove and retain the large wing springs.
-
Remove and retain the clevis pins and hairpins from each wing deck cylinder. Remove the height adjustment pin from the deck lift plate on the right side of the center deck.
-
Lower the wing decks, but Do Not draw them into the operating position.
-
Remove and retain the left and right wing belt shield lynch pins, belt shield, and the wing deck belts.
-
Remove and retain the locking cotter pins and the cylinder pins that attach to the rod end of the deck fold cylinders and to the wing decks.
Note: The wing decks must not be pulled into the operating position in order to remove the cylinder pins.
-
Remove and retain the bolts that secure the upper pivot pins to the deck and then remove the pivot pins.
-
Pull the wing deck outward to separate it from the center deck section.
-
Remove the flanged bushings from the upper pivot points and clean the bore.
-
Apply a thin bead of Loctite® 680 to the entire circumference of the rear edge of the new bushings.
-
Insert and gently tap the new bushings into the opening and properly seat them into place.
-
Place a block of wood under the inside edge of the center deck to make it easier to work on the lower pivot point bushings.
-
Remove and retain the lower pivot point bolts (reference Figure 37 and Figure 40).
-
Remove and discard the flanged bushing from the front and rear of the wing deck and clean the bore.
-
Apply a thin bead of Loctite® 680 to the entire circumference of the rear edge of the new bushings.
-
Insert and gently tap the new bushings into the opening and properly seat them into place.
-
Reinstall the lower deck pin assemblies and bolts into the lower deck pivot points and hand-tighten.
-
To aid in the ease of reinstalling the wing deck sections, carefully remove the exposed end of the spring that applies pressure to the rear of the wing deck cover.
-
Push the left wing deck back to the center deck. Align and install the upper pivot deck pins in the front and rear of the deck and secure with the bolts that were removed previously (reference Figure 39).
-
Align the lift cylinder arm and reinstall the pin, making sure that the locking tab is aligned with the associated opening in the mount. Reinstall the locking cotter pin to secure.
-
Reattach the spring that was removed in Step 22 that applies pressure to the rear of the wing deck cover.
-
Reinstall the wing deck belts.
-
Reinstall the wing deck belt shields and secure with the lynch pins.
-
Raise the wings to the transport position and secure them in place with the clevis pins and hairpins.
For 144 Inch Deck Models Only: Reinstall the large wing springs.
-
Reinstall the height of cut pin.
Check Seat Belt
Maintenance Service Interval | Maintenance Procedure |
---|---|
Before each use or daily |
|
Visually inspect seat belt for wear, cuts, and proper operation of retractor and buckle. Replace before operating if damaged.
Check for Loose Hardware
Maintenance Service Interval | Maintenance Procedure |
---|---|
Before each use or daily |
|
-
Stop engine, wait for all moving parts to stop, and remove key. Engage parking brake.
-
Visually inspect machine for any loose hardware or any other possible problem. Tighten hardware or correct the problem before operating.
Service Air Cleaner
Maintenance Service Interval | Maintenance Procedure |
---|---|
Every 400 hours |
|
-
Stop engine, wait for all moving parts to stop, and remove key. Engage parking brake.
-
Unhook two air filter canister latches to gain access to the air cleaner element.
-
Remove air cleaner canister cover and remove outer element.
-
Check the condition of the paper element. Replace if dirty, bent or damaged.
-
Check the condition of the inner element. Replace whenever it appears dirty, typically every other time the paper element is replaced. Clean the base around the inner element before removing, so dirt does not get into the engine.
-
Do Not wash or use pressurized air to clean paper element or inner element.
-
Reinstall elements. Position the cover so that the rubber dust ejector is pointing downward and secure with retaining clips.
Check Deck Gearbox Oil
Maintenance Service Interval | Maintenance Procedure |
---|---|
Every 50 hours |
|
-
Position the machine and mower deck on a level surface.
-
Lower the mower deck to the 1 inch (2.5 cm) height of cut.
-
Disengage the PTO, move the motion-control levers to the neutral-lock position, and engage the parking brake.
-
Stop engine, wait for all moving parts to stop, and remove key.
-
Lift the footrest, exposing the top of the mower deck.
-
Remove the dipstick/fill plug from the top of the gearbox and make sure that the lubricant is between the marks on the dipstick (Figure 42).
-
If the lubricant level is low, add lubricant. Screw the dipstick all the way back in; remove and check if the lubricant level is between the marks on the dipstick.
Important: Do not overfill the gearbox; overfilling the gearbox may damage it.
Check Drive Wheel Gearbox Oil– (144 Inch Deck Models Only)
Maintenance Service Interval | Maintenance Procedure |
---|---|
Every 400 hours |
|
-
Position the machine and mower deck on a level surface.
-
Stop engine and wait for all moving parts to stop. Engage parking brake.
-
Orient gearbox check plug to the right with fill port on the top (as shown in Figure 43).
-
Remove and retain check plug. Check oil level is up to check port. Reinstall check plug when complete.
-
Repeat on opposite side.
Important: Do not overfill the gearbox; overfilling the gearbox may damage it.
Check Hydraulic Fluid Level
Maintenance Service Interval | Maintenance Procedure |
---|---|
Before each use or daily |
|
-
Position the machine and mower deck on a level surface.
-
Stop engine and wait for all moving parts to stop. Engage parking brake.
-
Raise the deck to extend the lift cylinders, shut off the engine, and remove the key.
-
Raise the seat to access the hydraulic fluid tank.
-
Remove the hydraulic fill cap from the filler neck.
-
Remove the dipstick and wipe it with a clean rag.
-
Place the dipstick into the filler neck; then remove it and check the level of fluid.
If fluid is needed add enough oil to put the level in between the two marks on the dipstick.
Important: Do Not overfill.
-
Replace the dipstick and fill cap; finger-tighten only.
-
Check all hoses and fittings for leaks.
Check Tire Pressures
Maintenance Service Interval | Maintenance Procedure |
---|---|
Every 50 hours |
|
-
Stop engine, wait for all moving parts to stop, and remove key. Engage parking brake.
-
Check tire pressure in drive tires.
-
Inflate drive tires to:
-
18 psi (124 kPa) for 60 and 72 inch deck models.
-
22 psi (152 kPa) for 96 and 144 inch deck models.
-
-
Semi-pneumatic caster tires do not need to be inflated.
Note: Do Not add any type of tire liner or foam fill material to the tires. Excessive loads created by foam filled tires may cause failures to the hydro drive system, frame, and other components. Foam filling tires will void the warranty.
Check Condition Of Belts
Maintenance Service Interval | Maintenance Procedure |
---|---|
Every 50 hours |
|
-
Stop engine, wait for all moving parts to stop, and remove key. Engage parking brake.
-
Remove left and right belt shields on deck and lift up floor pan to inspect belts.
Lubricate Grease Fittings
Maintenance Service Interval | Maintenance Procedure |
---|---|
Every 50 hours |
|
Every 400 hours |
|
Yearly |
|
Note: See chart for service intervals.
-
Stop engine, wait for all moving parts to stop, and remove key. Engage parking brake.
-
Lubricate fittings with one to two pumps of NLGI grade #2 multi-purpose gun grease.
Refer to the following chart for fitting locations and lubrication schedule.
60 and 72 Inch Models
Lubrication Chart Fitting Locations Initial Pumps Number of Places Service Interval 1. Deck drive PTO 1 3 50 hrs 2. Deck idler pivot 1 1 Every 400 hrs or Yearly 3. Caster wheel bearings *0 2 *Yearly 4. Caster pivots *0 2 Every 400 hrs or Yearly 96 and 144 Inch Model
Lubrication Chart Fitting Locations Initial Pumps Number of Places Service Interval 1. Deck drive PTO 1 3 50 hrs 2. Deck idler pivot 1 3 Every 400 hrs or Yearly 3. Caster wheel bearings *0 4 *Yearly 4. Caster pivots *0 5 Every 400 hrs or Yearly * See step 3 for special lubrication instructions on the front caster pivots and the Lubricate Caster Wheel Hubs section for special lubrication instructions on the front casters wheel hubs.
-
Lubricate front caster pivots once a year. Remove hex plug and cap. Thread grease zerk in hole and pump with grease until it oozes out around top bearing. Remove grease zerk and thread plug back in. Place cap back on.
Check Wheel Lug Nuts
Maintenance Service Interval | Maintenance Procedure |
---|---|
After the first 100 hours |
|
-
Stop engine, wait for all moving parts to stop, and remove key. Engage parking brake.
-
Torque to 85-105 ft-lb (115-142 N-m).
Lubricate Caster Wheel Hubs
-
Stop engine, wait for all moving parts to stop, and remove key. Engage parking brake.
-
Remove caster wheel from caster forks.
-
Remove seal guards from the wheel hub.
-
Remove one of the spacer nuts from the axle assembly in the caster wheel. Note that thread locking adhesive has been applied to lock the spacer nuts to the axle. Remove the axle (with the other spacer nut still assembled to it) from the wheel assembly.
-
Pry out seals, and inspect bearings for wear or damage and replace if necessary.
-
Pack the bearings with a NLGI grade #1 multi-purpose grease.
-
Insert one bearing, one new seal into the wheel.
Note: Seals (Exmark P/N 103-0063) must be replaced.
-
If the axle assembly has had both spacer nuts removed (or broken loose), apply a thread locking adhesive to one spacer nut and thread onto the axle with the wrench flats facing outward. Do Not thread spacer nut all of the way onto the end of the axle. Leave approximately 1/8 inch (3 mm) from the outer surface of the spacer nut to the end of the axle inside the nut.
-
Insert the assembled nut and axle into the wheel on the side of the wheel with the new seal and bearing.
-
With the open end of the wheel facing up, fill the area inside the wheel around the axle full of NLGI grade #1 multi-purpose grease.
-
Insert the second bearing and new seal into the wheel.
-
Apply a thread locking adhesive to the 2nd spacer nut and thread onto the axle with the wrench flats facing outward.
-
Torque the nut to 75-80 in-lb (8-9 N-m), loosen, then re-torque to 20-25 in-lb (2-3 N-m). Make sure axle does not extend beyond either nut.
-
Reinstall the seal guards over the wheel hub and insert wheel into caster fork. Reinstall caster bolt and tighten nut fully.
Important: To prevent seal and bearing damage, check the bearing adjustment often. Spin the caster tire. The tire should not spin freely (more than 1 or 2 revolutions) or have any side play. If the wheel spins freely, adjust torque on spacer nut until there is a slight amount of drag. Reapply thread locking adhesive.
Drain Fuel Filter/Water Separator
Maintenance Service Interval | Maintenance Procedure |
---|---|
Every 50 hours |
|
-
Stop engine, wait for all moving parts to stop, and remove key. Engage parking brake.
-
Place a drain pan under the fuel filter and loosen the drain plug approximately 1 turn.
-
Water should drain.
-
When fuel begins to flow from the filter, tighten the drain plug.
Important: Water or other contaminants in fuel can severely damage fuel pump and/or the other engine components.
Change Fuel Filter/Water Separator
Maintenance Service Interval | Maintenance Procedure |
---|---|
Every 400 hours |
|
Danger
Use of improper components can result in system failure, fuel leakage and possible explosion.
-
Ensure that an Authorized Service Dealer replace the fuel filter and any components for the fuel system.
-
Use only approved fuel lines, hose clamps and fuel filters for high pressure systems.
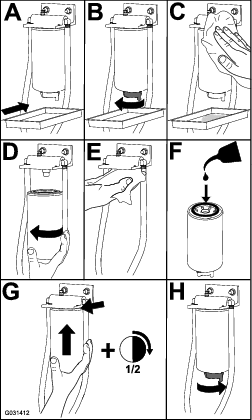
The 3TNV88C and 3TNV86CT engines have two fuel filters; see Figure 48 for locations.
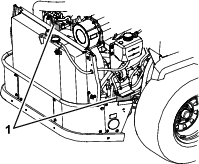
Change Deck Gearbox Oil
Maintenance Service Interval | Maintenance Procedure |
---|---|
After the first 200 hours |
|
Every 400 hours |
|
-
Position the machine and cutting unit on a level surface.
-
Lower the mower deck to the 1 inch (2.5 cm) height of cut.
-
Disengage the PTO, move the motion control levers to the neutral-lock position, and engage the parking brake.
-
Shut off the engine, remove the key, and wait for all moving parts to stop before leaving the operating position.
-
Lift the footrest, exposing the top of the mower deck.
-
Remove the dipstick/fill plug from the top of the gearbox (reference Figure 42).
-
Extract oil through the fill port using a vacuum devise or remove the gearbox from the deck and pour the oil out.
-
Reinstall the gearbox if it was removed to drain.
-
Add enough lubricant, approximately 14 oz (420 ml), until the level is between the marks on the dipstick.
Important: Do Not overfill the gearbox; overfilling the gearbox may damage it.
Change Engine Oil and Filter
Maintenance Service Interval | Maintenance Procedure |
---|---|
After the first 200 hours |
|
Every 200 hours |
|
Every 400 hours |
|
Yearly |
|
-
Stop engine, wait for all moving parts to stop, and remove key. Engage parking brake.
-
Drain oil while engine is warm from operation.
-
Place pan under machine to catch oil. Remove the oil drain plug. Allow oil to drain and replace oil drain plug.
-
Replace the oil filter every oil change. Clean around oil filter and unscrew filter to remove. Before reinstalling new filter, apply a thin coating of Exmark 4-Cycle Premium Engine Oil on the surface of the rubber seal. Turn filter clockwise until rubber seal contacts the filter adapter then tighten filter an additional 1 full turn.
-
Unlatch the hood and lift it up to access oil fill. Clean around oil fill cap and remove cap. Fill to specified capacity and replace cap. Use oil recommended in the Check Engine Oil Level section. Do Not overfill. Start the engine and check for leaks.
-
Start the engine at idle for 5 minutes. Stop engine and wait three minutes, then check the oil level. If required, add oil to bring level to the “FULL” mark on the dipstick. Do Not overfill.
-
Check for leaks, including around the oil filter.
-
Wipe up any spilled oil.
Change Drive Wheel Gearbox Oil–144 Inch Deck Models Only
Maintenance Service Interval | Maintenance Procedure |
---|---|
After the first 50 hours |
|
Every 800 hours |
|
-
Position the machine and mower deck on a level surface.
-
Stop engine and wait for all moving parts to stop. Engage parking brake.
-
Raise the rear of machine up and support with jack stands (or equivalent support) just high enough to allow drive wheels to turn freely once the motor brake is released.
-
Remove wheel and orient gearbox with drain port on the bottom with fill port on the top.
-
Place a pan under each drain port. Remove, retain, and wipe clean the drain plug, check plug, and fill plug to allow the fluid drain.
-
Reinstall the drain plug and add oil (approximately 18 oz) until it runs out the check port. Install check plug and fill plug back in their respective ports.
-
Repeat on opposite side.
Important: Do Not overfill the gearbox; overfilling the gearbox may damage it.
Change Hydraulic System Filter and Fluid
Maintenance Service Interval | Maintenance Procedure |
---|---|
After the first 200 hours |
|
Every 400 hours |
|
Every 800 hours |
|
Hydro Oil | Change Interval |
Exmark Ruby Transmission Fluid. | After first 200 hours*Every 800 hours thereafter |
Mobilfluid 424 | After first 200 hours*Every 400 hours thereafter |
*May need more often under severe conditions.
Note: Exmark Ruby Transmission Fluid is recommended. Refer to the chart for an acceptable alternative.
-
Stop engine, wait for all moving parts to stop, and remove key. Engage parking brake.
-
Raise seat.
-
There are four drain plugs that need to be removed to do a complete fluid change. Place a pan under each drain plug from the following components: hydraulic reservoir, transmission case, and the left and right wheel motors (see Figure 50).
-
Unscrew the filter to remove and allow fluid to drain from reservoir.
Important: Before reinstalling new filter, apply a thin coat of Exmark Ruby Transmission Fluid on the surface of the rubber seal.
Install a new filter and turn the filter clockwise until the rubber seal contacts the filter adapter, then tighten the filter an additional 2/3 to 3/4 turn.
-
Reinstall all four plugs. The wheel motor drain plugs are magnetic; wipe clean before reinstalling.
-
Remove the fill port plug on the top of each wheel motor.
-
Fill each motor with approximately 1.5 qt (1.4 L) Exmark Ruby Transmission Fluid.
-
Replace the plugs.
-
Remove the reservoir cap and dipstick from the fluid tank.
-
Add 8 qt (7.6 L) of oil in the reservoir.
Note: The reservoir will be overfull at this point the level will quickly go down once the machine is started and cooling loop oil fills the transmission case.
Important: Exmark will not assume responsibility for damage caused by improper substitutions.
-
-
Raise the rear of machine up and support with jack stands (or equivalent support) just high enough to allow drive wheels to turn freely.
-
Allow the engine to run about one minute and then shut it off.
-
Start the engine and check for oil leaks. Move the speed control levers to the full speed and run for several minutes. Shut down machine and recheck fluid level.
-
Check the level of the hydraulic fluid; refer to Check Hydraulic Fluid Level section.
Add enough oil to put the level between the two marks on the dipstick. it may take 4-5 qt (3.8-4.7 L) depending how much oil stayed in the cooling loop while draining.
-
Replace the dipstick and reinstall the cap.
Hydro Oil | Change Interval |
Exmark Ruby Tran Fluid. | After first 200 hours*Every 800 hours thereafter |
Mobilfluid 424 | After first 200 hours*Every 400 hours thereafter |
*May need more often under severe conditions.
Note: Exmark Ruby Transmission Fluid is recommended. Refer to the chart for an acceptable alternative.
-
Stop engine, wait for all moving parts to stop, and remove key. Engage parking brake.
-
Raise seat.
-
There are two drain plugs that need to be removed to do a complete fluid change. Place a pan under each drain plug from the following components: hydraulic reservoir, and transmission case (see Figure 52).
-
Unscrew the filter to remove and allow fluid to drain from reservoir.
Important: Before reinstalling new filter, apply a thin coat of Exmark Ruby Transmission Fluid on the surface of the rubber seal.
Install a new filter and turn the filter clockwise until the rubber seal contacts the filter adapter, then tighten the filter an additional 2/3 to 3/4 turn.
-
Reinstall all plugs. Wipe clean before reinstalling.
-
Raise the rear of machine up and support with jack stands (or equivalent support) just high enough to allow drive wheels to turn freely.
-
Remove the reservoir cap and dipstick from the fluid tank.
-
Add 8 qt (7.6 L) of oil in the reservoir.
The reservoir will be overfull at this point the level will quickly go down once the machine is started and cooling loop oil fills the transmission case.
-
-
Allow the engine to run about one minute and then shut it off.
-
Start the engine and check for oil leaks. Move the speed control levers to the full speed and run for several minutes. Shut down machine and recheck fluid level.
-
Check the level of the hydraulic fluid; refer to Check Hydraulic Fluid Level section.
Add enough oil to put the level between the two marks on the dipstick. it may take 4-5 qt (3.8-4.7 L) depending how much oil stayed in the cooling loop while draining.
-
Replace the dipstick and reinstall the cap.
Check Engine Coolant Level
Maintenance Service Interval | Maintenance Procedure |
---|---|
Before each use or daily |
|
Note: If the engine coolant level is below the indicator line on the overflow bottle when the engine is cold, the coolant temperature gauge may not register correctly during operation and/or the warning buzzer may not sound if the engine overheats.
-
Position the mower on a flat surface.
-
Stop engine and wait for all moving parts to stop.
-
Check with engine cold.
-
Open the hood and check the coolant level in the expansion tank on the right side of the machine. The coolant level should be between the marks on the overflow bottle.
-
If the coolant level is low, remove the cap to the overflow bottle and fill to the indicator line. Machines should only be filled a 50/50 mix of water and ethylene glycol.
Note: The use of Havoline® Xtended Life coolant is recommended. Havoline® can be identified by its orange color.
Warning
Engine coolant is hot and pressurized and radiator and surrounding parts are hot. Spray or steam from hot, pressurized liquid in the engine cooling system and touching a hot radiator may cause severe burns.
Allow the engine to cool completely before removing the radiator cap or servicing any component of the cooling system.
Caution
Engine coolant is toxic. Swallowing coolant can cause poisoning.
-
Do Not swallow.
-
Keep out of reach of children and pets.
Change Engine Coolant
Maintenance Service Interval | Maintenance Procedure |
---|---|
Every 2,000 hours |
|
-
Position the mower on a flat surface.
-
Stop engine, wait for all moving parts to stop, and remove key. Engage parking brake.
-
Tilt hood forward to gain access to the cooling area.
Warning
Engine coolant is hot and pressurized and radiator and surrounding parts are hot. Spray or steam from hot, pressurized liquid in the engine cooling system and touching a hot radiator may cause severe burns.
Allow the engine to cool completely before removing the radiator cap or servicing any component of the cooling system.
Caution
Engine coolant is toxic. Swallowing coolant can cause poisoning.
-
Do Not swallow.
-
Keep out of reach of children and pets.
-
-
Drain coolant when engine is cool. Remove the radiator cap, place a pan under the radiator, and remove the drain plug at the bottom of the radiator.
-
Remove the coolant hose from the oil cooler and drain the coolant from the engine block (reference Figure 54).
-
Reinstall all drain plugs and hoses.
-
Fill radiator with a 50/50 mix of water and ethylene glycol.
Note: The use of Havoline® Xtended Life coolant is recommended.
Allow some room (approximately 1/2 inch (12.7 mm)) for expansion. Add 50/50 coolant mix to overflow bottle on the left side of the engine as required to bring the level up to the indicator line on the bottle.
Warning
Engine compartment contains open belt drives, fans, and other rotating components that can cause injury. Fingers, hands, loose clothing, or jewelry can get caught by the rotating fan and drive shaft.
-
Do Not operate machine without the covers in place.
-
Keep fingers, hands, and clothing clear of rotating components.
-
Shut off engine, wait for moving parts to stop, engage parking brake and remove key, before performing maintenance.
-
-
Operate engine until the engine thermostat opens and coolant is circulating through the radiator core. As air is purged from the engine block and the coolant level drops, add additional coolant to the radiator.
-
When the radiator is completely full and no additional coolant can be added, continue running and install the radiator cap. Make sure that the cap is completely seated by pressing down firmly while turning until the cap stops. Once the cap is installed, the engine may be stopped.
Thread Locking Adhesives
Thread locking adhesives such as “Loctite 242” or “Fel-Pro, Pro-Lock Nut Type” are used on the following fasteners:
Caster wheel spacer nuts.
Mobil HTS Grease (Or Food-Grade Anti-seize)
Mobil HTS grease (or food-grade anti-seize) is used in the following locations:
-
Between the cutter housing spindle and bearings.
-
Between the cutter housing spindle and sheave.
Copper-Based Anti-seize
Copper-based anti-seize is used in the following location:
On threads of Blade Bolts. See Check Mower Blades section.
Dielectric Grease
Dielectric grease is used on all blade type electrical connections to prevent corrosion and loss of contact. Dielectric grease should not be applied to sealed connectors.
Adjustments
Note: Disengage PTO, shut off engine, wait for all moving parts to stop, engage parking brake, and remove key before servicing, cleaning, or making any adjustments to the unit.
Caution
Raising the mower deck for service or maintenance relying solely on mechanical or hydraulic jacks could be dangerous. The mechanical or hydraulic jacks may not be enough support or may malfunction allowing the unit to fall, which could cause injury.
Do Not rely solely on mechanical or hydraulic jacks for support. Use adequate jack stands or equivalent support.
Deck Leveling–
-
Position the machine on a flat surface.
-
Shut off the engine, wait for all moving parts to stop, remove the key, and engage the parking brake.
-
Check the tire pressure in drive tires and pneumatic front caster tires (if equipped). Proper inflation pressure for tires is 18 psi (124 kPa). Adjust if necessary.
-
Using the deck-lift switch, move the deck height out of the transport position (or 5 1/2 inches (140 mm) cutting height).
-
Insert the height adjustment pin into the 3 inches (76 mm) cutting height location.
-
Release the transport lock and allow the deck to lower to the cutting height.
-
Raise the discharge deflector (side discharge units only).
-
Measure from the level surface to the front tip of the center blade. The measurement should read 3 inches (76 mm).
Note: In most conditions, the back tips on the side blades should be adjusted:Side Discharge Units: 1/4 inch (6.4 mm) higher than the front.Rear Discharge Units: to be level with the front.
-
Adjust the height — to increase, turn the adjuster screw clockwise; to decrease, turn counterclockwise.
Loosen the jam nuts on the top of each deck adjuster. Fine tune the adjuster on the front deck lift assembly by turning it to get 3 inch (7.6 cm) height (see Figure 57).
-
Measure the back tip height. Fine tune rear adjusters as required; the single point adjustment can be utilized to gain more adjustment.
-
Side Discharge Units: The back tips of the side blades should measure 3 1/4 inches (8.3 cm).
-
Rear Discharge Units: The back tips of the side blades should measure 3 inches (7.6 cm).
-
-
Re-measure until all four sides are the correct height. Tighten all the nuts on the deck lift arm assemblies.
-
Lower discharge deflector (side discharge units only).
-
If the four deck adjusters do not have enough adjustment to achieve accurate cut height with the desired rake, the single point adjustment can be utilized to gain more adjustment (see Figure 58).
-
To adjust the single point system, first loosen the front and rear height of cut plate mounting bolts.
Note: On Rear Discharge Units: The mower deck is attached in the front holes at the factory (see Figure 59). If needed, use the back holes for further adjustment when leveling the mower deck.
-
If the deck is too low, tighten the single point adjustment bolt by rotating it clockwise. If the deck is too high, loosen the single point adjustment bolt by rotating it counterclockwise.
Note: Loosen or tighten the single point adjustment bolt enough to move the height of cut plate mounting bolts at least 1/3 the length of the available travel in their slots. This will regain some up and down adjustment on each of the four deck links.
-
Re-tighten front and rear height of cut plate mounting bolts.
Important: Torque the front and rear height of cut plate mounting bolts to 67-83 ft-lb (91-113 N-m).
-
Repeat steps 8 through 12.
Deck Leveling–
Leveling the Center and Wing Decks
-
Position the machine on a flat surface.
-
Shut off the engine, wait for all moving parts to stop, remove the key, and engage the parking brake.
-
Check the tire pressure in drive tires and pneumatic front caster tires (if equipped). Proper inflation pressure for tires is 22 psi (152 kPa). Adjust if necessary.
-
Raise the center deck and fold the wings by pressing down at the rear of the deck lift rocker switch. Hold the switch down until both wings are completely folded.
-
Insert the center height adjustment pin into the 4 inches (102 mm) cutting height location.
-
Unlock the left and right wing deck cam locks.
-
Remove and retain the wing deck height of cut lanyard.
-
Insert the height adjustment pin into the 4 inch (102 mm) cutting height location and reinstall the lanyard.
-
Lock the left and right wing deck cam locks.
-
Start engine. Brake must be engaged and motion control levers out to start engine. Operator does not have to be in the seat. Be sure that all persons are clear of the deck wings. Press and hold the front of the deck control switch until the center deck lowers and both wings are completely unfolded to the cutting height.
-
Stop engine, wait for all moving parts to stop, engage the parking brake and remove the key.
-
Measure from the level surface to the front tip of the LH and RH center deck blades. The measurement should read 4 inches (102 mm).
Adjusting the Center Deck
-
Adjust the height — to increase, turn the adjuster screw clockwise; to decrease, turn counterclockwise.
Loosen the jam nuts on the top of each deck adjuster. Fine tune the adjuster on the front deck lift assembly by turning it to get the correct height for the center deck left and right front blade tips (see Figure 62).
-
Measure the back tip height. Fine tune rear adjusters as required; the single point adjustment can be utilized to gain more adjustment.
In most conditions, the rake (or difference between the back tips and front tips of the blades) should be adjusted 1/4 inch (6.4 mm) higher than the front with a minimum of 1/16 inch (3 mm) and a maximum of 3/8 inch (9.5 mm).
-
Re-measure until all four sides are the correct height. Tighten all the nuts on the deck lift arm assemblies.
-
If the four deck adjusters do not have enough adjustment to achieve accurate cut height with the desired rake, the single point adjustment can be utilized to gain more adjustment.
-
To adjust the single point system, first loosen the front and rear height of cut plate mounting bolts. Fine tune the rear adjusters as required; the single point adjustment can be utilized to gain more adjustment.
-
If the deck is too low, tighten the single point adjustment bolt by rotating it clockwise. If the deck is too high, loosen the single point adjustment bolt by rotating it counterclockwise. Loosen the front and rear height of cut plate mounting bolts. Fine tune the rear adjusters as required; the single point adjustment can be utilized to gain more adjustment.
Note: Loosen or tighten the single point adjustment bolt enough to move the height of cut plate mounting bolts at least 1/3 the length of the available travel in their slots. This will regain some up and down adjustment on each of the four deck links.
-
Re-tighten front and rear height of cut plate mounting bolts.
Important: Torque the front and rear height of cut plate mounting bolts to 27-33 ft-lb (37-45 N-m).
Adjusting the Wing Decks
-
Measure from the level surface to the front tip of the LH wing outside deck blade. The measurement should read 4 inches (102 mm).
-
Measure from the level surface to the front tip of the RH wing outside deck blade. The measurement should read 4 inches (102 mm).
Note: As with the center deck, in most conditions, the rake or the back tips on the wing blades should be adjusted 1/4 inch (6.4 mm) higher than the front with a minimum of 1/16 inch (3 mm) and a maximum of 3/8 inch (9.5 mm).
-
The left and right wing decks have blade height adjustments with front and rear adjust points. To adjust the wing blade height, first loosen the front and rear height of cut hanger mounting nuts (items 1 and 4) as shown in Figure 64. There are four locations — two on each side of the channel.
-
Measure the back of the wing blades. If either has less than 1/16 inch (1.5 mm) rake, raise the back of the deck by tightening the LH and RH rear adjustments (item 2, Figure 64) until all four blades have a minimum of 1/16 inch rake (1.5 mm). Readjust the wing rear wheels so they lightly touch the ground with minimal pressure. Tighten all four rear hanger mount points (item 1, Figure 64).
-
Retighten the front and rear height of cut hanger jam nuts.
Deck Belt Tension
Self-tensioning - No adjustment necessary.
Parking Brake Adjustment for All Except 144 Inch Deck Models
Maintenance Service Interval | Maintenance Procedure |
---|---|
After the first 100 hours |
|
Every 400 hours |
|
Check to make sure brake is adjusted properly. This procedure must be followed after the first 100 hours or when a brake component has been removed or replaced.
Caution
Raising the mower deck for service or maintenance relying solely on mechanical or hydraulic jacks could be dangerous. The mechanical or hydraulic jacks may not be enough support or may malfunction allowing the unit to fall, which could cause injury.
Do Not rely solely on mechanical or hydraulic jacks for support. Use adequate jack stands or equivalent support.
-
Drive the machine onto a level surface.
-
Disengage the blade control switch (PTO), move the motion control levers to the neutral locked position and engage the parking brake (lever is in the “up” position).
-
Stop the engine, wait for all moving parts to stop, and remove the key.
-
Raise the back of the machine up and support the machine with jack stands.
-
Remove the rear tires from the machine.
-
Remove any debris from the brake area.
-
Rotate the drive wheel release handle to the “released” position. Refer to the Drive Wheel Release Valves section in Operation.
-
If the link assembly is attached (see Figure 65)
-
in the front position, the length=8.63 inches (21.9 cm).
-
in the rear position, the length=9.15 inches (23.2 cm).
-
-
The length of the spring should measure 3 3/4 inches (8.9 cm).
-
Once the spring length is achieved, check to see if there is a visible gap between the trunion and the shoulder.
-
Disengage the park brake, the lever should be in the down position. Turn the wheel hub by hand in both directions relative to the caliper; the wheel hub should move freely.
-
If a gap is needed or the wheel hub does not move freely:
-
Disengage the park brake.
-
Disconnect and fine-tune the rear linkage assembly:
-
Shorten the link to create a gap.
-
Lengthen the link to allow wheel hub movement.
-
-
Reconnect the rear linkage assembly.
-
-
Engage the parking brake and check the gap.
-
Repeat steps 11 through 14 until a visible gap is achieved and the wheel hub rotates freely. Repeat for the brake on the right side.
Note: The brake should fully disengage when the brake is in the “released” position.
-
Rotate the drive wheel release handle to the “operating” position. Refer to the Drive Wheel Release Valves section in Operation.
-
Install the rear tires and torque lug nuts to 85-105 ft-lb (115-142 N-m).
-
Remove jack stands.
Motion Control Linkage Adjustment
Warning
Engine must be running and drive wheels must be turning so motion control adjustment can be performed. Contact with moving parts or hot surfaces may cause personal injury.
Keep fingers, hands, and clothing clear of rotating components and hot surfaces.
Caution
Raising the mower deck for service or maintenance relying solely on mechanical or hydraulic jacks could be dangerous. The mechanical or hydraulic jacks may not be enough support or may malfunction allowing the unit to fall, which could cause injury.
Do Not rely solely on mechanical or hydraulic jacks for support. Use adequate jack stands or equivalent support.
-
This adjustment must be made with the drive wheels turning. First raise the rear of machine up and support with jack stands (or equivalent support) just high enough to allow the drive wheels to rotate freely.
-
Unhook seat latch and tilt seat forward.
-
Remove the electrical connection from the seat safety switch, located directly to the left of the seat switch assembly beside the hydraulic oil reservoir.
Temporarily install a jumper wire across the terminals in the connector of the main wiring harness.
-
Run the unit at least 5 minutes with the drive levers at full forward speed to bring hydraulic system oil up to operating temperature.
-
Loosen lock nuts from the ball joints at each end of the pump control linkage (Figure 66).
-
Start engine. Brake must be engaged and motion control levers out to start engine. Operator does not have to be in the seat because of the jumper wire being used. Run engine at full throttle and release brake.
Note: The motion control lever needs to be in neutral while making any necessary adjustments.The left rod assembly controls the left wheel and the right rod assembly controls the right wheel.
-
Bring the motion control lever into the neutral position. Adjust RH pump control rod length by rotating the double nuts on the rod in the appropriate direction until the wheels slightly creep in reverse. Move the motion control lever to the reverse position and while applying slight pressure to the lever allow the reverse indicator spring to bring the levers back to neutral. The wheel must stop turning or slightly creep in reverse. When adjustment is complete, tighten lock nuts onto ball joints. Repeat for LH motion control lever.
-
Shut off unit. Remove jumper wire from wire harness connector and plug connector into seat switch.
Motion Control Damper Adjustment
The top damper mounting bolt can be adjusted to obtain a more desired motion control lever resistance. See Figure 67 for mounting options.
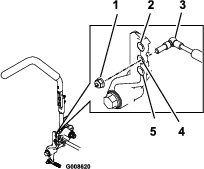
Caster Pivot Bearings Pre-Load Adjustment
Remove dust cap from caster and tighten nyloc nut until washers are flat and back off 1/4 of a turn to properly set the pre-load on the bearings. If disassembled, make sure the spring disc washers are reinstalled as shown in Figure 68.
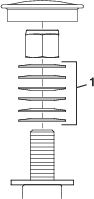
Cleaning
Cleaning and Storing Safety
-
Park machine on level ground, disengage drives, set parking brake, stop engine, and remove key. Wait for all moving parts to stop before leaving the operator’s position. Allow the machine to cool before servicing, adjusting, fueling, cleaning, or storing.
-
Clean grass and debris from the cutting unit, muffler, drives, grass catcher, and engine compartment to prevent fires.
-
Allow the machine to cool before storing the machine in any enclosure. Do Not store the machine or fuel container, or refuel, where there is an open flame, spark, or pilot light such as on a water heater or other appliance.
Clean Engine and Exhaust System Area
Maintenance Service Interval | Maintenance Procedure |
---|---|
Before each use or daily |
|
Caution
Excessive debris around engine and exhaust system area can cause engine, exhaust area, and hydraulic system to overheat which can create a fire hazard.
Clean all debris from engine and exhaust system area.
-
Stop engine, wait for all moving parts to stop, and remove key. Engage parking brake.
-
Clean around flywheel, cylinder head, injectors, and injector pump.
-
Clean all debris from the exhaust system area.
-
Wipe up any excessive grease or oil around the engine and exhaust area.
Important: Do Not use water to clean engine. Use low pressure compressed air. See Engine Owner's Manual.
Clean the Radiator
Maintenance Service Interval | Maintenance Procedure |
---|---|
Every 50 hours |
|
-
Stop engine, wait for all rotating parts to stop and remove key. Engage parking brake.
-
Allow engine to cool.
-
Rotate hood forward
-
Using compressed air, blow out debris stuck between the fins of the entire radiator, both from the top down and from the bottom up.
-
If debris remains, it may be necessary to use water from a low pressure hose. If the radiator is clean, proceed to step 7.
-
Cover the engine with a piece of cardboard, or a plastic sheet. Squirt water through the fins. Blow through with low pressure air from both directions. If debris remains, repeat until clean.
-
Lower hood.
-
Start the engine to ensure the fan is functioning properly.
Clean Debris From Machine
Maintenance Service Interval | Maintenance Procedure |
---|---|
Before each use or daily |
|
-
Stop engine, wait for all moving parts to stop, and remove key. Engage parking brake.
-
Clean off any oil, debris, or grass build-up on the machine and cutting deck, especially under deck belt shields, around the fuel tank, around engine and exhaust area.
Important: You can wash the machine with mild detergent and water. Do not pressure wash the machine. Avoid excessive use of water, especially near the control panel, under the seat, around the engine, hydraulic pumps, and motors.
Clean Hood Screen on Machine
Maintenance Service Interval | Maintenance Procedure |
---|---|
Every 50 hours |
|
-
Stop engine, wait for all moving parts to stop, and remove key. Engage parking brake.
-
Clean off any debris, or grass build-up on the machine hood screen, hood and around engine and exhaust area.
Important: You can wash the machine with mild detergent and water. Do not pressure wash the machine. Avoid excessive use of water, especially near the control panel, under the seat, around the engine, hydraulic pumps, and motors.
Clean Grass Build-Up Under Deck
Maintenance Service Interval | Maintenance Procedure |
---|---|
Before each use or daily |
|
-
Stop engine, wait for all moving parts to stop, and remove key. Engage parking brake.
-
Raise deck to the transport position.
For 96 inch models, raise the center deck and outer wings. Lock each wing in the up position.
-
Lift the front of machine and support it using jack stands or equivalent support.
-
Clean out any grass build-up from underside of deck and in discharge deflector.
Inspect Engine Valve Clearance
Maintenance Service Interval | Maintenance Procedure |
---|---|
Every 800 hours |
|
Inspect the engine-valve clearance. Refer to the engine owner’s manual.
Waste Disposal
Motor Oil Disposal
Engine oil and hydraulic oil are both pollutants to the environment. Dispose of used oil at a certified recycling center or according to your state and local regulations.
Battery Disposal
Danger
Battery electrolyte contains sulfuric acid, which is poisonous and can cause severe burns. Swallowing electrolyte can be fatal or if it touches skin can cause severe burns.
-
Wear safety glasses to shield eyes, and rubber gloves to protect skin and clothing when handling electrolyte.
-
Do Not swallow electrolyte.
-
In the event of an accident, flush with water and call a doctor immediately.
Federal law states that batteries should not be placed in the garbage. Management and disposal practices must be within relevant federal, state, or local laws.
If a battery is being replaced or if the unit containing the battery is no longer operating and is being scrapped, take the battery to a local certified recycling center. If no local recycling is available return the battery to any certified battery reseller.